In this article
Solve your top 5 stock problems
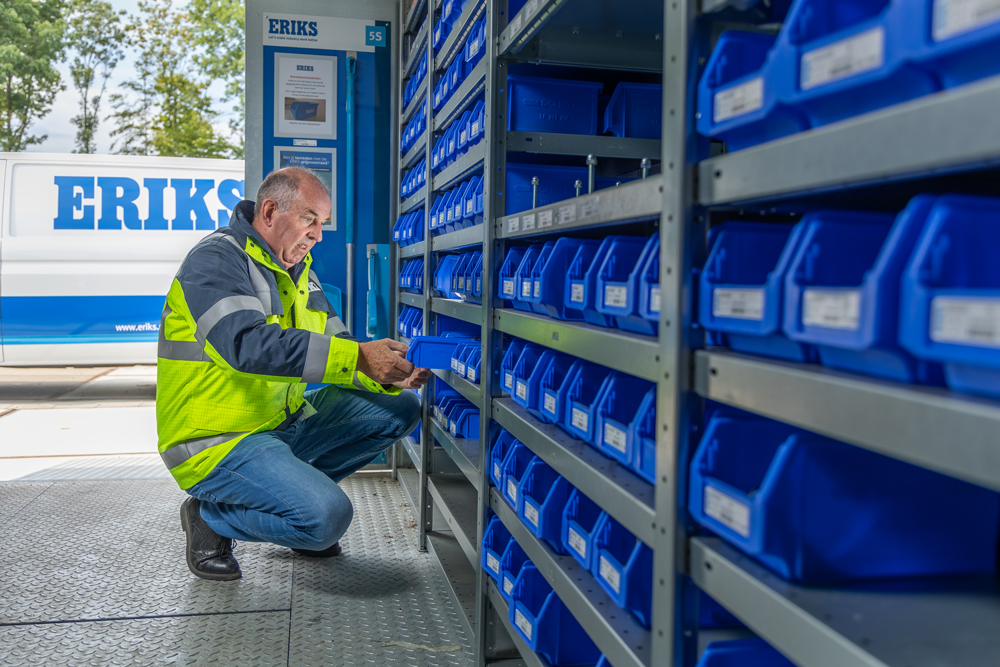
Supply chain solutions to cut costs, reduce downtime, and improve efficiency
Inventory management is a constant balancing act between controlling costs, minimising downtime, and keeping production moving on time. Stock managers are often juggling outdated equipment, changing technologies, and the need for accurate data. How do you keep up? In this article, Ronald Smolders, VMI Manager at ERIKS, talks about Vendor Managed Inventory (VMI) and how it helps companies excel at balancing and managing their inventory.
The challenge of constantly changing day-to-day operations
No matter the industry, companies must forecast supply and demand, prevent stockouts and surpluses, all while managing tricky supply chains. Raw material price fluctuations, delivery delays, and unexpected demand spikes pose major financial risks.
1. Keeping equipment and parts up-to-date
Consider a large food processing plant with conveyor belts and packing machines that have been running for over 15 years. Maintenance costs are creeping up, and every breakdown leads to expensive delays in meeting customer demand. One of their bottling machines, essential for the production line, frequently stalls due to a worn-out motor part that’s no longer manufactured.
Aging equipment and rising costs
As production lines like these age, companies face higher costs to keep up with maintenance and repairs until replacement is feasible. Outdated machinery often demands specialised maintenance skills and parts that can be hard to find.
Using advanced monitoring for maintenance and supplier relationships for rare parts
Companies are turning to advanced monitoring and predictive maintenance systems to tackle these problems. For instance, vibration sensors and real-time data analysis on critical machines help identify signs of wear and tear early on — spotting that stalling motor issue long before it leads to downtime.
Building close relationships with suppliers also ensures quick access to rare spare parts, even for older equipment. By strategically managing maintenance through these technologies and partnerships, companies can spread out costs, avoid disruptive production delays, and make timely replacements before breakdowns affect operations.
2. Data collection and accuracy
“The challenge with data when using VMI is that products are sold by various suppliers,” Ronald explains. “A supplier might change a packaging unit, stop selling a product, or assign it a different item number, which can cause issues with orders. This means we’re constantly managing everything at the item level. Every change must be implemented; otherwise, we may end up scanning something that isn’t in stock. This is a daily reality. For optimal inventory, it’s essential to work with a well-configured system that provides stable, real-time data.”
Industrial companies manage thousands of parts, and without accurate data, stock and maintenance managers risk overstocking or running out of critical items — leading to costly downtime. Vendor Managed Inventory (VMI) systems, along with tools like barcode scanning and Electronic Data Interchange (EDI), help keep inventory data accurate and up-to-date by restocking based on actual consumption patterns and production needs.
3. Valuable warehouse space
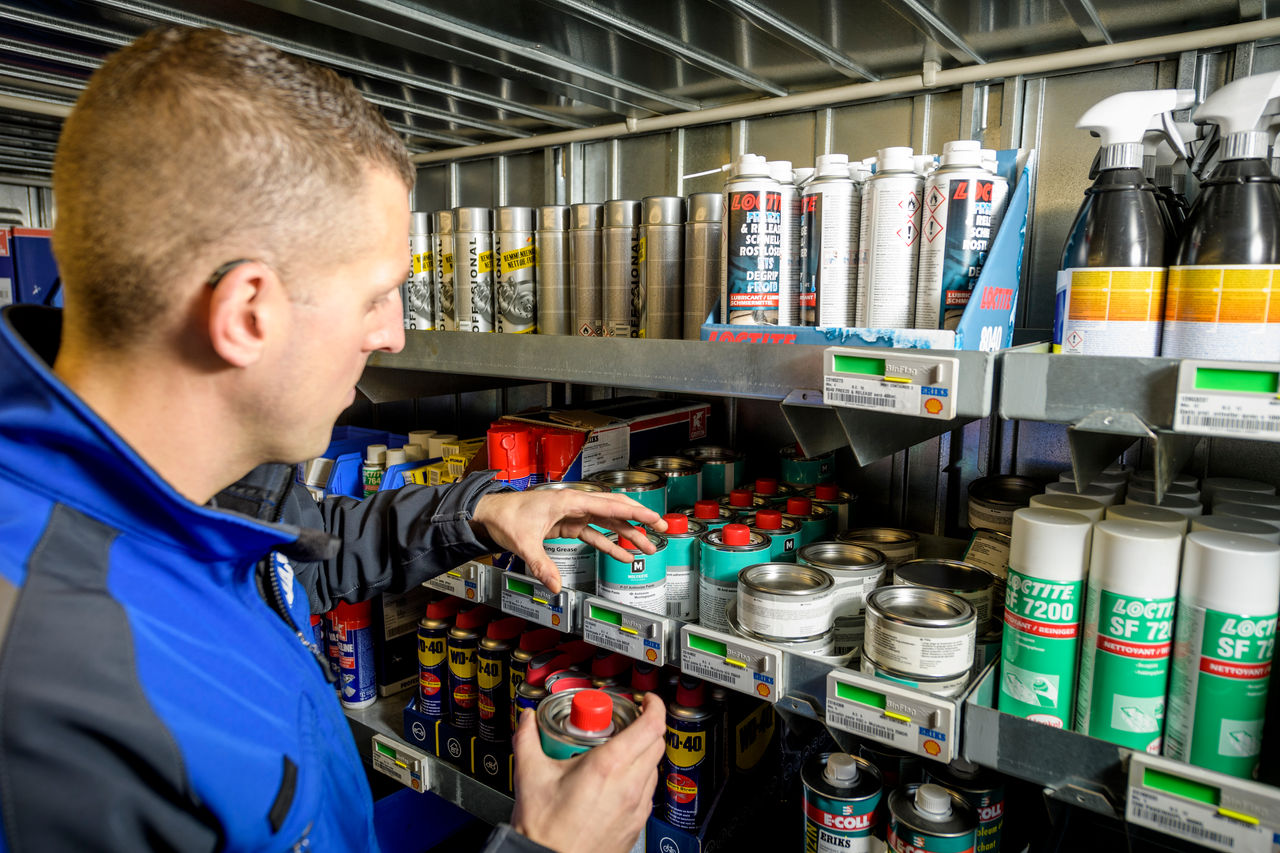
Warehouse space comes at a premium, and inefficient inventory management can lead to costly space shortages, obsolete stock, and waste. As Ronald mentioned before, bad data often results in excess inventory accumulating, occupying space unnecessarily, and increasing the risk of parts aging or expiring before use. VMI optimises space by ensuring only essential items are on-site and improving overall layout efficiency. For frequently used small parts and tools, vending machines make the most of limited space and enhance accessibility.
“Inventory is usually about availability,” says Ronald. “Accessibility is also a major challenge for our clients. They often have the stock, but don’t always know where it is. Our VMI solution introduces logic in stock placement, grouping related products together, and organising by size. We also create visuals so a technician unfamiliar with the warehouse can find what they need quickly, significantly improving their efficiency.”
4. Upping uptime: Lessons from a large Dutch brewery
Predictive maintenance is one of the primary strategies for increasing uptime. By installing sensors to monitor critical components, companies can detect issues early, before they cause major disruptions. Consolidating suppliers further streamlines the ordering process and improves visibility into available spare parts, reducing the risk of missing items and minimising downtime during breakdowns.
Ronald explains how VMI contributes to uptime in situ. “At a large Dutch brewery, for instance, a conveyor belt occasionally stops because a chain breaks. ERIKS' VMI solution ensures that chain is stocked in the disruption inventory. When a chain breaks, it costs tens of thousands of euros per hour in lost production. Having this reserve stock pays for itself quickly. This is a strong argument we present to clients when discussing the necessity of keeping certain items in stock. If the chain has to come from somewhere else, it leads to significant downtime, which is not an option for a producer of this size.”
5. Reducing stock value and total cost of ownership (TCO)
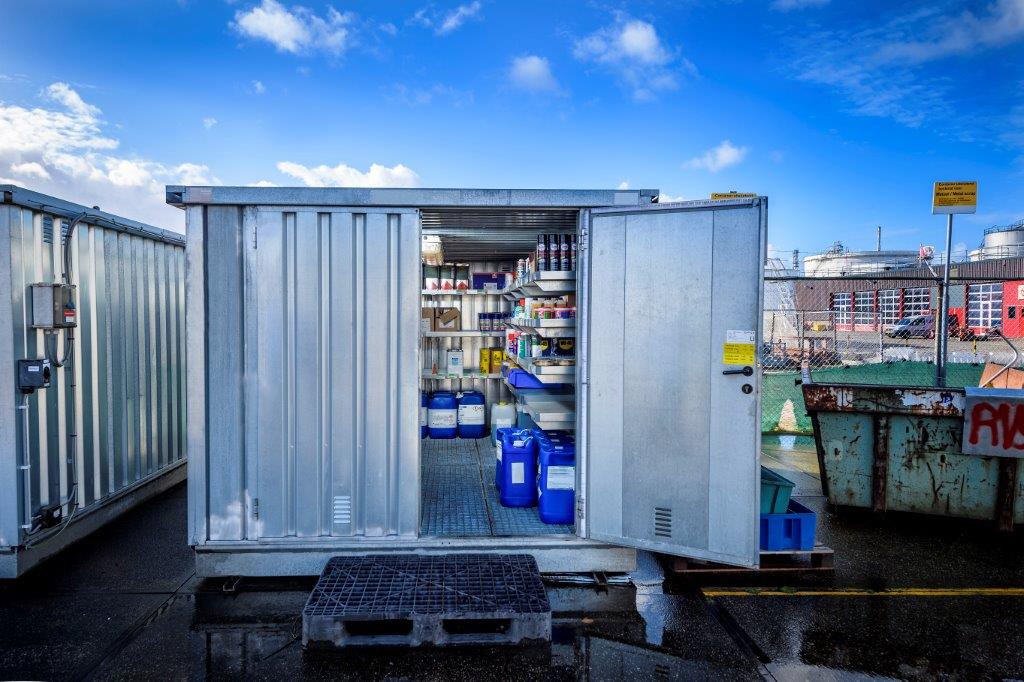
Holding inventory directly impacts total cost of ownership (TCO). While essential parts are necessary, carrying outdated or surplus stock can drive up costs significantly. Without a clear, structured approach, companies may find themselves holding unnecessary inventory that strains the balance sheet and adds little value.
A coordinated inventory strategy — where purchasing, warehouse management, and maintenance teams share responsibility — helps prevent excess stock. Partnering with an experienced external provider like ERIKS can also streamline inventory management, optimise processes, and gradually reduce TCO over time.
Future innovations are likely to offer even more opportunities to enhance inventory efficiency. By seizing these opportunities, companies can not only save costs but also strengthen their competitive edge. For sustainable inventory management, strategic collaboration across departments and the use of appropriate technologies are essential, enabling the flexibility needed to maintain optimal inventory levels.