How DSM reduces their TCO with innovative stock management
Case study
Discover how DSM no longer wastes time on searching for replacement parts, increased stock availability and reduced costs by 20%.
Organising, managing and maintaining the warehouse was a complex and time-consuming job for DSM. It’s not part of the core business, but it is a critical aspect of their (and any chemical company) day-to-day operation. It should be well organised and not too expensive.
In this case study, you’ll learn:
- What challenges DSM faced in maintaining their warehouse
- What steps they have taken to find the right solution
- Which solution helped them to increase the efficiency of their stock management, leading to less inventory costs, less administration, higher availability and ultimately higher productivity
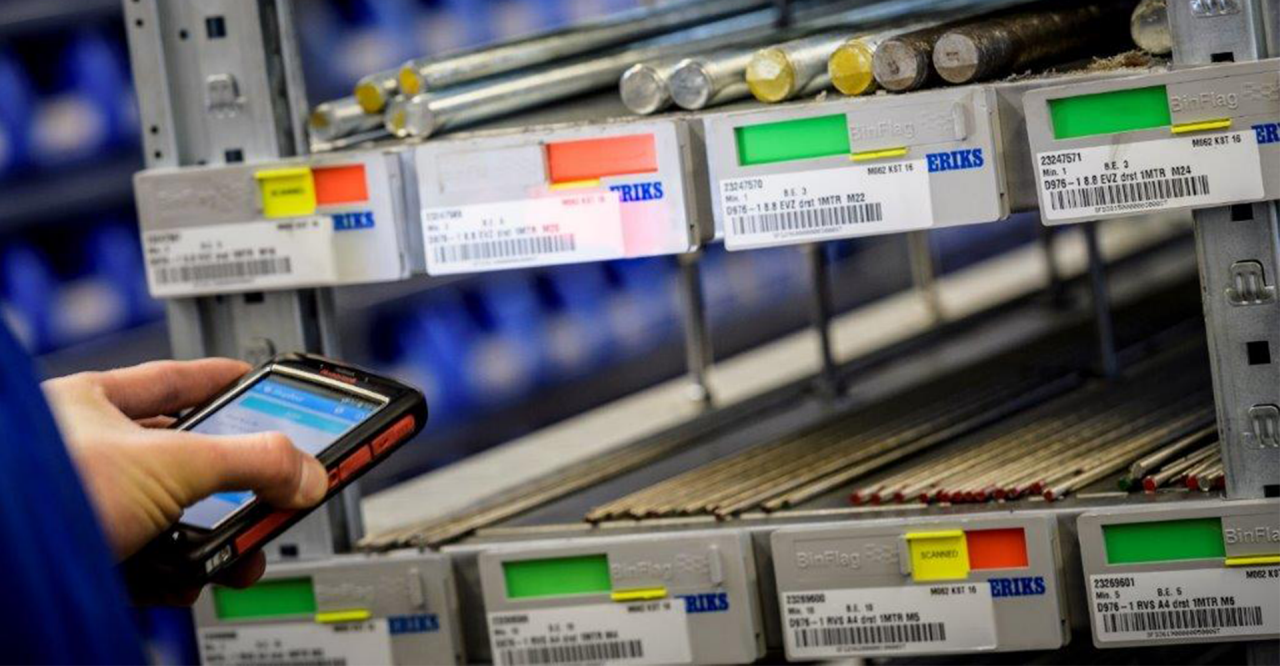
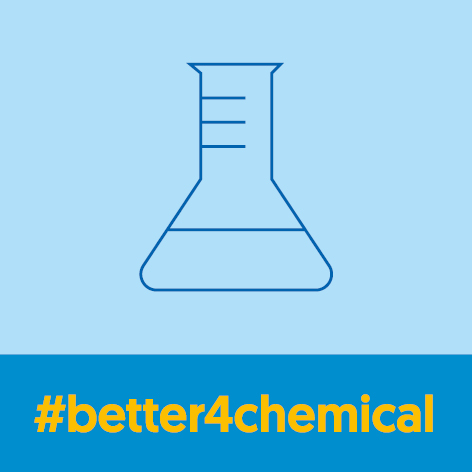
Download the DSM case study
We hope DSM’s story helps you to discover how organising, managing and maintaining the warehouse can be less of a challenge.
Contact
Direct contact
Want to speak directly with one of our employees or specialist? Don’t wait and get in touch
General contact
Get in contact with us. Please fill in our online form and we will contact you as soon as possible.
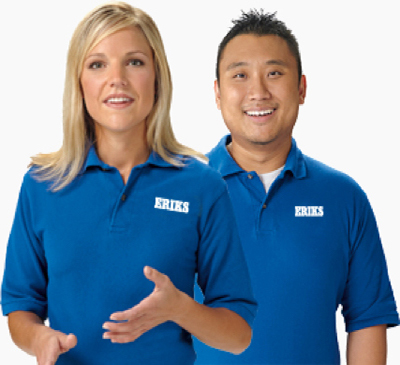