In this article
Gaskets: key selection criteria
Gaskets are used for a wide variety of applications in every industry. Gaskets are vital for reliable and efficient production. The huge variety of materials, shapes and sizes offers an infinite scope of application possibilities. A clear selection process helps you purchase the right gaskets for your production environment.
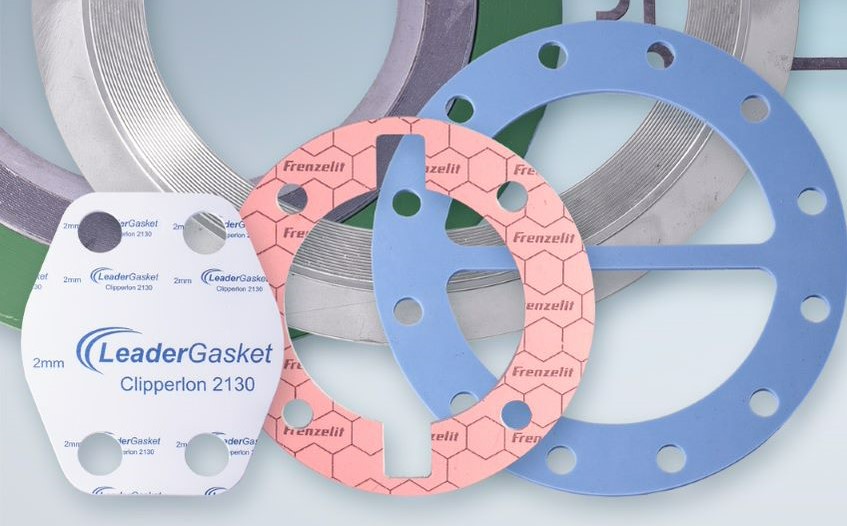
The importance of a suitable gasket
Despite their often small size and 'invisible' role in the production process, gaskets are crucial. Selecting the right gaskets is, therefore, very important. A wrong choice can have major consequences. In the design phase of a machine or component, this can mean extra work, higher costs and longer time-to-market. With ongoing processes, there is a risk of leakages, errors in production or even accidents with far-reaching consequences. High-quality gaskets increase workplace safety and allow machines and components to function better and last longer. All this can lead to a more efficient production process and a significant reduction in downtime.
A gasket for every application
That sounds reassuring. But when you realise that, due to all the possible variations, there are tens of thousands of different gaskets available, a structured selection process becomes an absolute necessity. Meticulous preparation is an essential first step. Before making the final selection, it is advisable to answer the following questions with detailed information from the client:
- In which application will the gasket be used? What role does this application play in the production process? And what environmental factors does this application have to deal with? By accurately describing the production process, it is also easier to determine later in the selection process the special properties required of your gaskets.
- What requirements must the gasket satisfy to meet the applicable production standards at your manufacturing location? Consider the minimum requirements for safety and quality. Available documentation and the traceability of utilised materials play an essential role in this evaluation.
- How long must the gasket last?
- Does the application allow standardisation, or is customisation required? Gaskets are ideal for standardisation, so consider rationalising the number of types and types. They can also be fully customised if required.
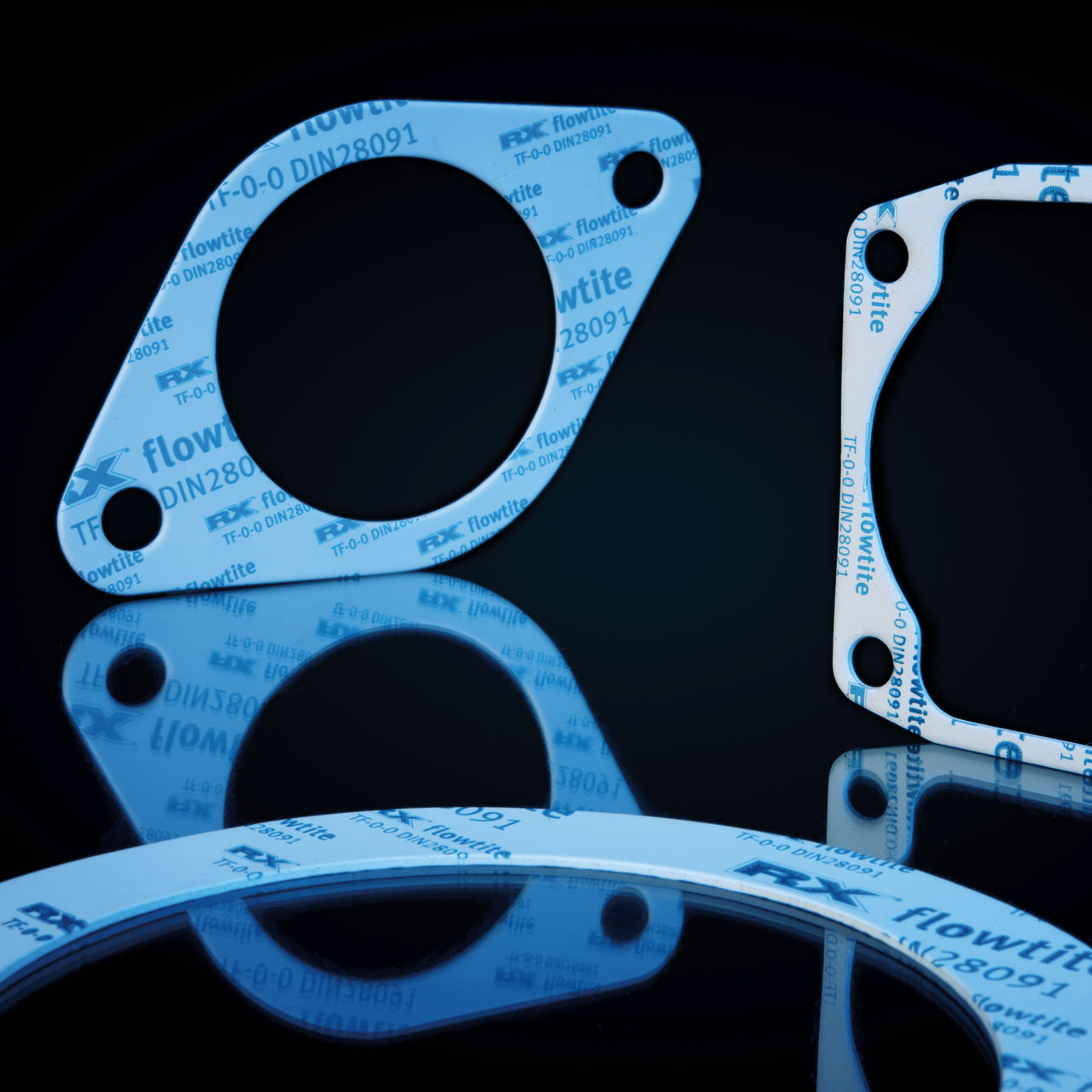
Selecting the right gasket
Gaskets are exposed to various production factors during the manufacturing process. These factors determine the minimum requirements and properties your gaskets must have. Medium, pressure and temperature are the most important of these. To select the right gasket for your application, you need to know exactly what conditions your production process is subjected to. The right gasket will not only withstand each production factor individually, but also perform at its best when the three are combined.
Medium
One of the most important selection criteria is that every component in a gasket must be chemically resistant to all media it comes into contact with. Not every gasket material is suited for exposure to certain liquids, solids or gases. In such cases, the gasket material might wear faster, for example, or show higher permeability. It is, therefore, important to assess the gasket's resistance to each individual medium. Please note that when two or more media are combined during the production process, this may require a new resistance level and different gasket material.
The right gasket must not only be resistant to the media passing through the device or pipes during the production process, cleaning agents, lubricants and other media in close proximity to the application should also be considered in the selection process.
Temperature
Temperatures can vary greatly from one application to another. Gaskets must not only withstand extremely high and low temperatures, but also any rapid changes in temperature. Take, for example, the furnaces at Tata Steel, where you have to deal with temperatures of up to several thousand degrees, or the pipelines of an oil refinery, where temperatures can suddenly increase extremely quickly. When selecting the right gasket, it is also important to factor in temperatures that arise when cleaning the application. It is important to realise beforehand that whatever temperatures you are dealing with, there is a gasket for every application.
Pressure
In production environments, it is quite common for pressures within an application to rise quickly and significantly. Not all gaskets can withstand this. A gasket that malfunctions under high pressure can create life-threatening situations. It is, therefore, imperative to know precisely how high the pressure can rise, and just as important is to estimate how often and how long the gasket has to operate under that pressure. The pressure level in the application largely determines the material from which the gasket should be made.
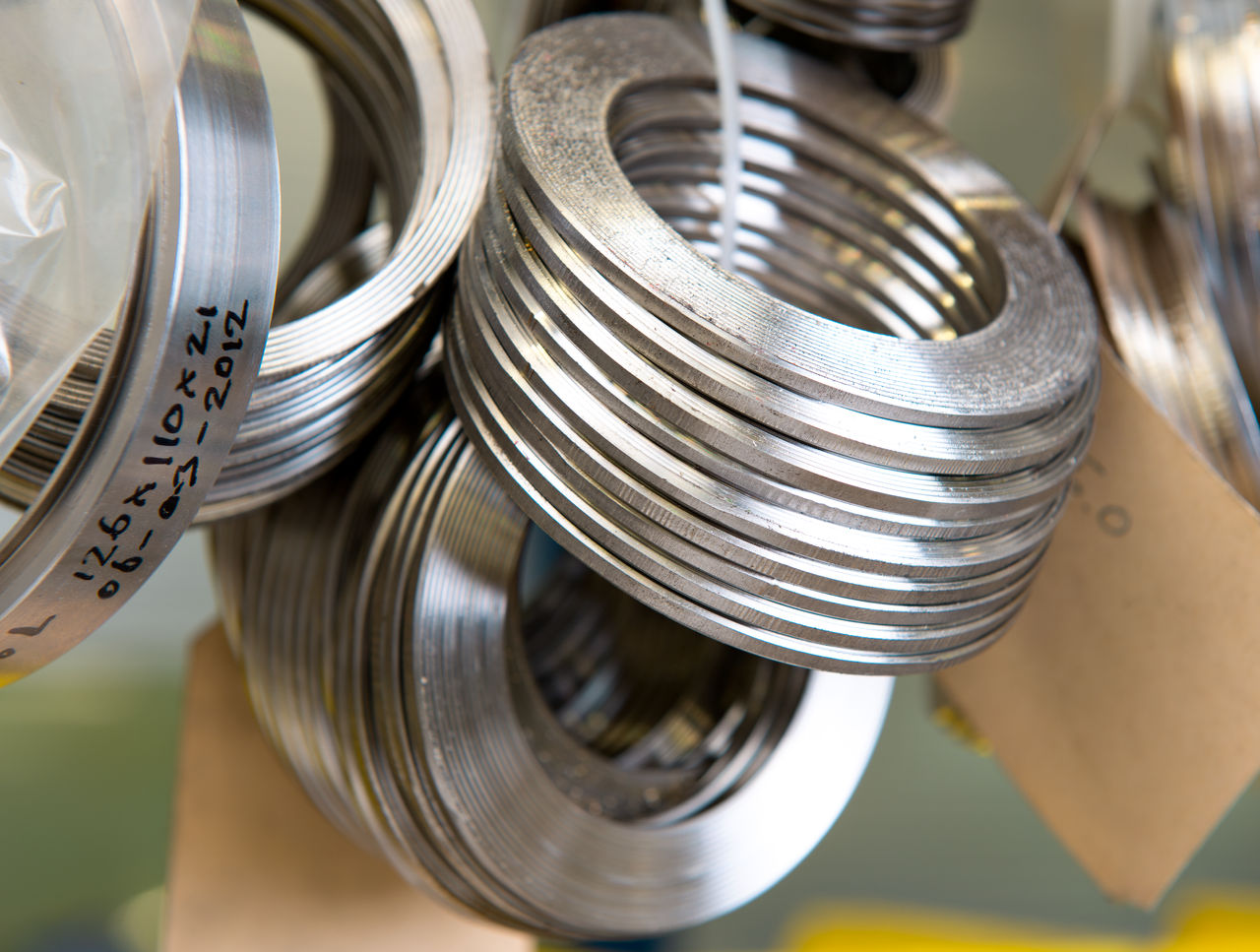
Which materials are most commonly used?
The first thing to do in selecting the right gasket is to use and understand available data from the previously mentioned production factors. Based on this data, you can make a more focused initial material selection. Gaskets are made from a variety of materials. The material used will depend on the minimum resistance levels required for optimal gasket performance. In general, the following resistance limits are applied:
Material
Minimum temperature |
Maximum temperature |
Maximum
pressure
Rubber |
-50ͦ C
70ͦ C - 120ͦ C
25 bar
PTFE
-200ͦ C
250ͦ C
80 bar
Fibre
-100ͦ C
400ͦ C
80 bar
Graphite
-200ͦ C
450ͦ C
100 bar.
Semi/metal
-270ͦ C
700ͦ C
160 - 400 bar
Metal
-270ͦ C
1000ͦ C
> 1000 bar
Material
Suitable for
Rubber |
plastic pipes requiring 'soft' gaskets, pipes through which natural gas passes at low pressure, pipes for waste or tap water.
PTFE
pipes for chemical media, dairy products and production processes in the pharmaceutical industry.
Fibre
pipes for medium-pressure gases, pipes for non-aggressive chemicals.
Graphite
medium-pressure steam, hot oil systems, exhaust systems and other applications particularly in the petrochemical industry and refineries.
Semi-metal
high-pressure reactors, medium-pressure steam and refining processes.
Metaal
high-pressure reactors, drills and pumps under very high pressure in offshore industry.
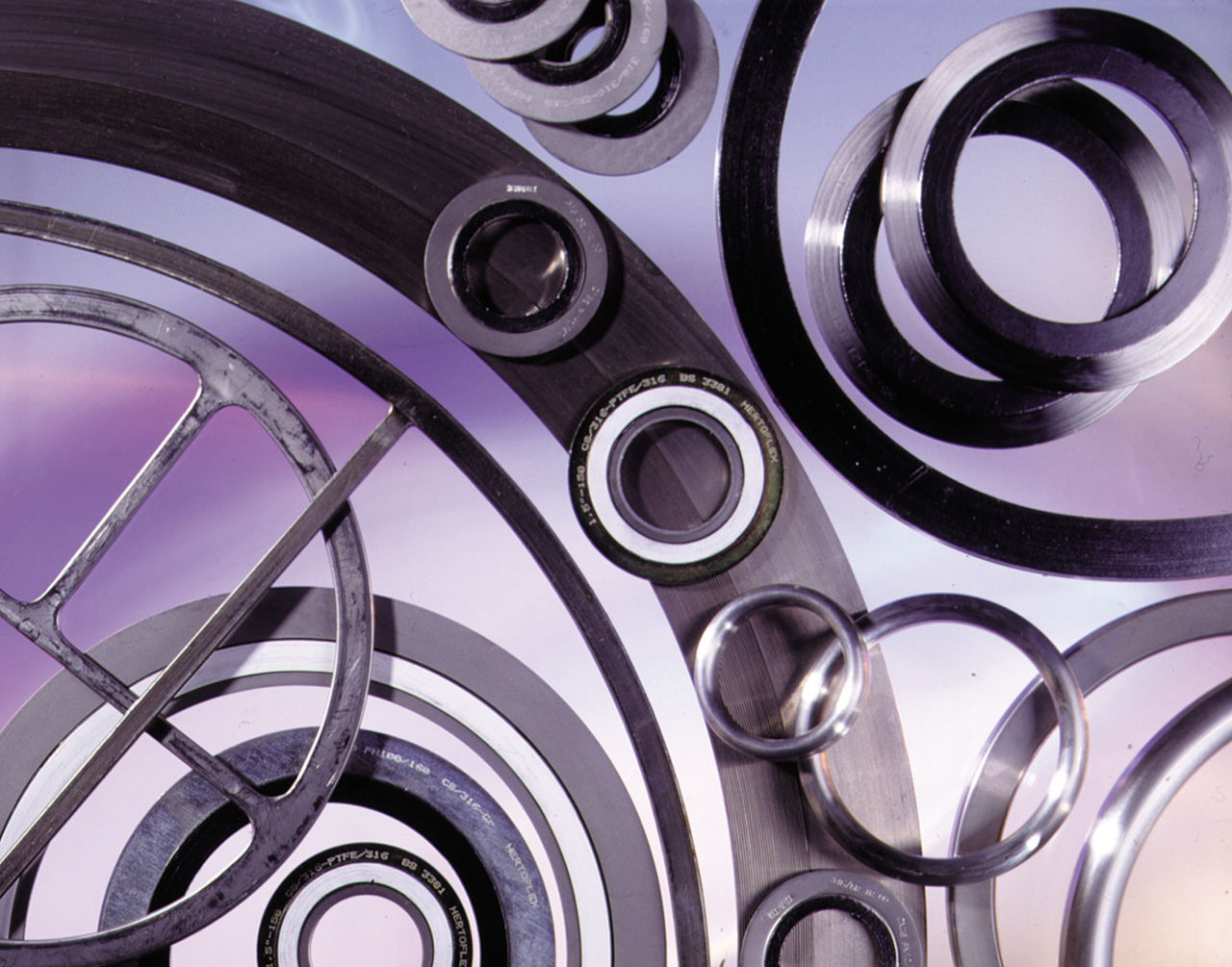
Laying out the above in a clear table shows the standard material requirements. Of course, there are many production environments where applications operate under abnormal conditions. For that reason, numerous variations are available within each material category, so you can always select a gasket that perfectly suits your application.
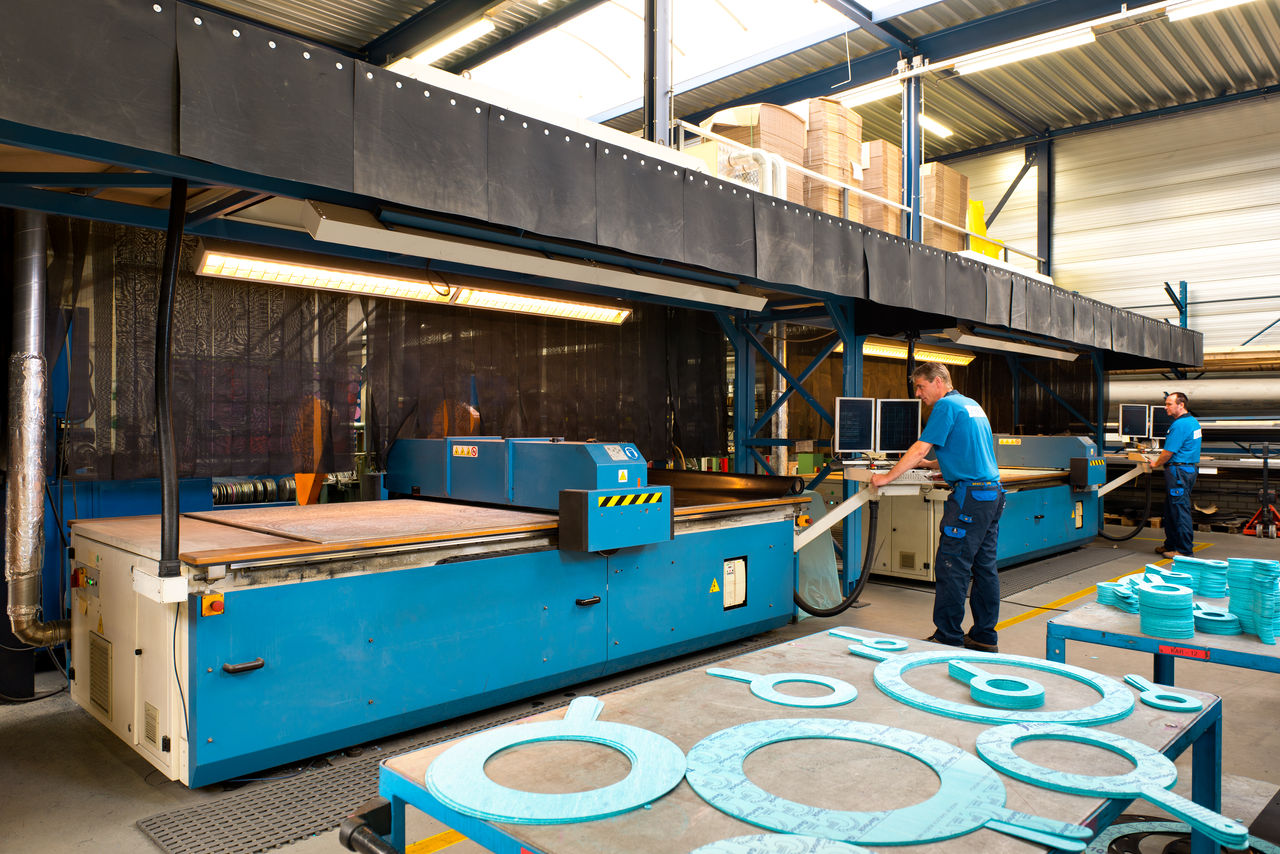
ERIKS as a reliable partner for all your gasket requirements
If you want to select the right gasket and avoid additional costs and extra work, engineers would be well advised to involve ERIKS early in the selection process. We know the questions from different industries, we know the challenges, and we know the solutions. With our unique combination of gasket know-how and expertise, a comprehensive product range and the specialised services to provide standard and customised solutions, we are your ideal partner for any application that requires gaskets.
Subscribe to our newsletter:
For the latest industry news and updates.