Finite Element Analysis (FEA) by ERIKS offers tailored sealing solutions through advanced simulations, ensuring optimal design and material selection.
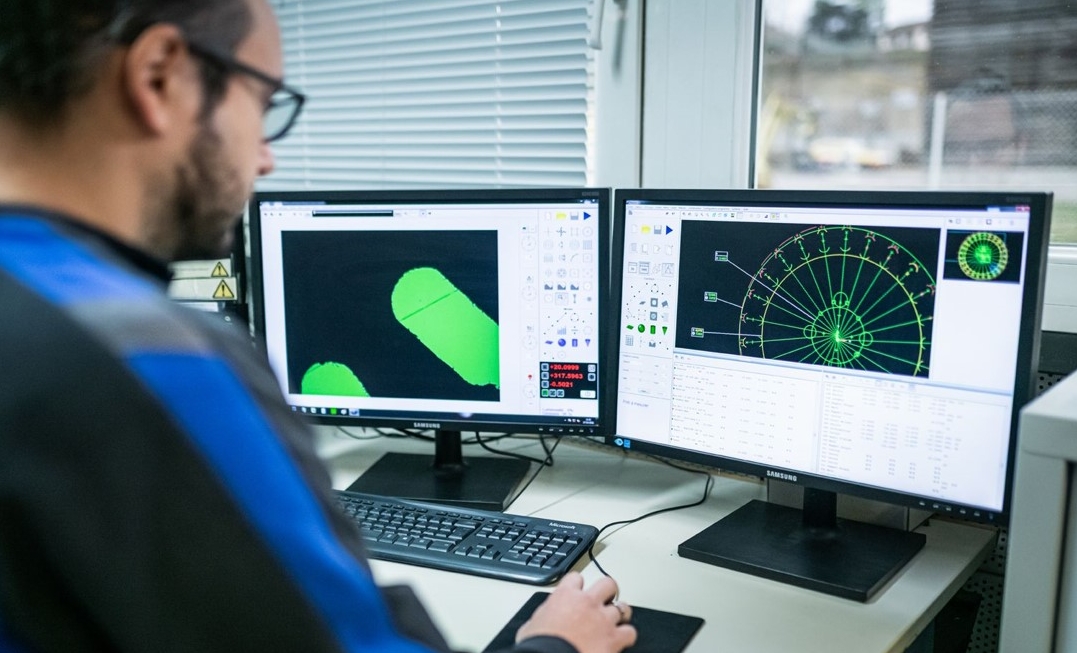
Engineering Your Success
Our engineering process, guided by Design for Six Sigma best practices, delivers high-quality products that meet stringent industry standards. Through a streamlined approach, we turn your ideas into practical, robust solutions, ensuring your project’s success from concept to production.
Avoid substandard quality, delays and budget overruns in your product development. By integrating early into your development processes, we ensure smooth collaboration, improved quality and cost efficiency. Our specialized engineers design and develop products from scratch to meet your specific needs.
With early involvement and joint technology roadmaps, we anticipate future needs and technological advancements, keeping you ahead of the curve. Whether you need solutions in Engineered Plastics, Flow Control, Gaskets, Hydraulic Systems, Industrial Hoses, Precision Motion & Control or Sealing & Polymer - ERIKS offers a comprehensive range of product groups tailored to your requirements.
A Customer-Centric Guide to Product Development
The Importance of Early Involvement
We actively seek opportunities to integrate into your development processes through various innovative approaches. Early involvement is crucial because it buys us valuable time to collaborate more effectively, fostering innovation, improving quality, and reducing costs. Addressing potential issues at the outset ensures that we can navigate the development process more smoothly and efficiently, avoiding costly mistakes later on.
- Collaborating on joint technical roadmap sessions
- Aligning our IT systems with yours
- Providing access to ERIKS' extensive 3D CAD repositories for easy integration into your engineering projects
These strategies ensure that we're involved from the very beginning, helping to steer the project toward success from day one. The engineering process is a structured, repeatable method for addressing challenges and creating solutions. It involves several critical steps, each essential for transforming ideas into practical products or systems. By following the same process, we ensure that all our energy is focused on developing solutions rather than figuring out our current status.
Following the Design for Six Sigma best practices, our engineering process is designed to deliver high-quality products that adhere to rigorous industry standards. This comprehensive approach ensures that the products we develop meet the stringent industry standards set by ISO 16949 (Automotive, HVAC, Semicon), ISO 13845 (Pharma) and EC1935 (Food), among others.
Define
Translating the voice of the customer into a development project
At the outset, we dedicate ourselves to comprehensively understanding your requirements. Through initial discussions, we aim to grasp the challenges you're facing and identify the critical quality drivers of your solution. It’s crucial for us to gather as much information as possible, including drawings, requirements and applicable norms/standards. A meticulous project intake, registration in necessary systems (e.g., CRM), and proper documentation storage (e.g., PDM system) are our top priorities. Preparing for the Triage / Stage Gate 1 meeting, we evaluate the opportunity’s attractiveness and complexity to strategically allocate our resources.
Design
Developing and documenting the essential components of the product
With the order confirmation in hand, we break down the problem into manageable subproblems, leveraging previous experiences for efficiency. Alternative designs are explored for each subsystem, with the best options moving forward for development. This phase includes risk analysis, prototype testing, and planning for tooling and production processes. Essential documentation such as PPAP or MRB's is drafted during this stage.
To further enhance the process, we establish a detailed project plan and provide an initial quotation for future development or series production. Here, the V-model methodology ensures a structured approach. This model emphasizes verification and validation at each stage, from defining requirements to design, implementation and testing. By systematically checking each phase against initial requirements, we improve the quality and reliability of the final product.
Optimize
Combining and optimizing the components into a robust product and production process
Following successful subsystem development, we integrate these components into the final product/assembly. Utilizing both advanced analytical tools and initial non-analytical methods, we determine the optimal configuration and begin creating the first versions of the work instructions. This leads to the creation of the 'First Article,' which undergoes rigorous testing to ensure robustness in both the product and the production process. After successful testing, the product is ready for null series production, marking a significant milestone towards launch.
Verify
Verification, testing, and delivering needed documentation
The verification phase begins with a null-series production, incorporating improvements identified during the first article's testing. A capability study and final measurement system analysis validate the robustness of the design, production, and quality control processes. We document all final versions of necessary work instructions, quality plans, and packaging details in our ERP system. This process culminates in the Stage Gate 3 - Release for Production meeting, where the product is officially approved for production and its care is transferred to the operations department.
Through this customer-centric approach, we ensure that the journey from concept to production is seamless, efficient, and aligned with your specific needs and industry standards.
Featured Knowledge Articles
Seal optimisation with Finite Element Analysis
3D printing supports innovation
In this article, we tell you exactly what 3D printing is used for and what benefits it brings to our customers.