In this article
Reducing Energy Consumption Starts with the Motor
Electric motors are commonplace in industry and form a large part of an organisation’s energy consumption. There are a staggering eight billion electric motors in use in the EU, today, consuming nearly 50% of all the electricity the EU produces.
But did you know that reducing your motor’s electrical energy consumption is the single most effective way you can save costs and improve the total cost of ownership (TCO) of your motor? In fact, 97% of the TCO is entirely down to the cost of electrical energy. The purchase price of a new motor only represents 1% of the TCO and maintenance adds another 2%.
Regularly reviewing your motor’s performance enables you to operate both as energy- and cost- efficiently as possible. However, there are many considerations to take into account when evaluating a motor, for example, legal requirements, the total running costs and motor size?
Choosing a motor that is simply compliant with regulations could actually cost your business thousands of Euros. By considering TCO you can operate with upmost efficiency, while also protecting the company’s bottom-line.
Understanding motor efficiency regulations
The energy efficiency of motors has come a long way since the 1960s. Motors have advanced from having an efficiency of 88% in 1960 to 95.8% in 2013, (as shown in figure 1)
With governments and agencies recognising the positive effects energy efficient electric motors have on reducing consumption and emissions, efficiency standards are now applied worldwide.
For example, in 1999, the European Committee of Electrical Machinery Manufacturers (CEMAP/EU) introduced a voluntary scheme for a limited range of motors. This has since evolved and in 2009, the International Electrotechnical Commission (IEC) created a new standard. The IEC 60034-30 standard defines the international energy efficiency classes as well as establishing the test methods for determining energy losses.
The energy efficiency classes are defined as:
- IE1 - Standard efficiency
- IE2 – High efficiency
- IE3 – Premium efficiency
- IE4 – Super-premium efficiency.
The efficiency for each class is defined for a rated output range from 0.75 to 375 kW and is calculated as the ratio of the mechanical output power to the electrical input power. An IE3 electric motor may achieve approximately 96% efficiency (depending on the power and speed) and an IE4 motor achieves about 97% efficiency. An even higher-efficiency IE5 rating, known as Ultra-Premium Efficiency, will be planned for future regulatory updates.
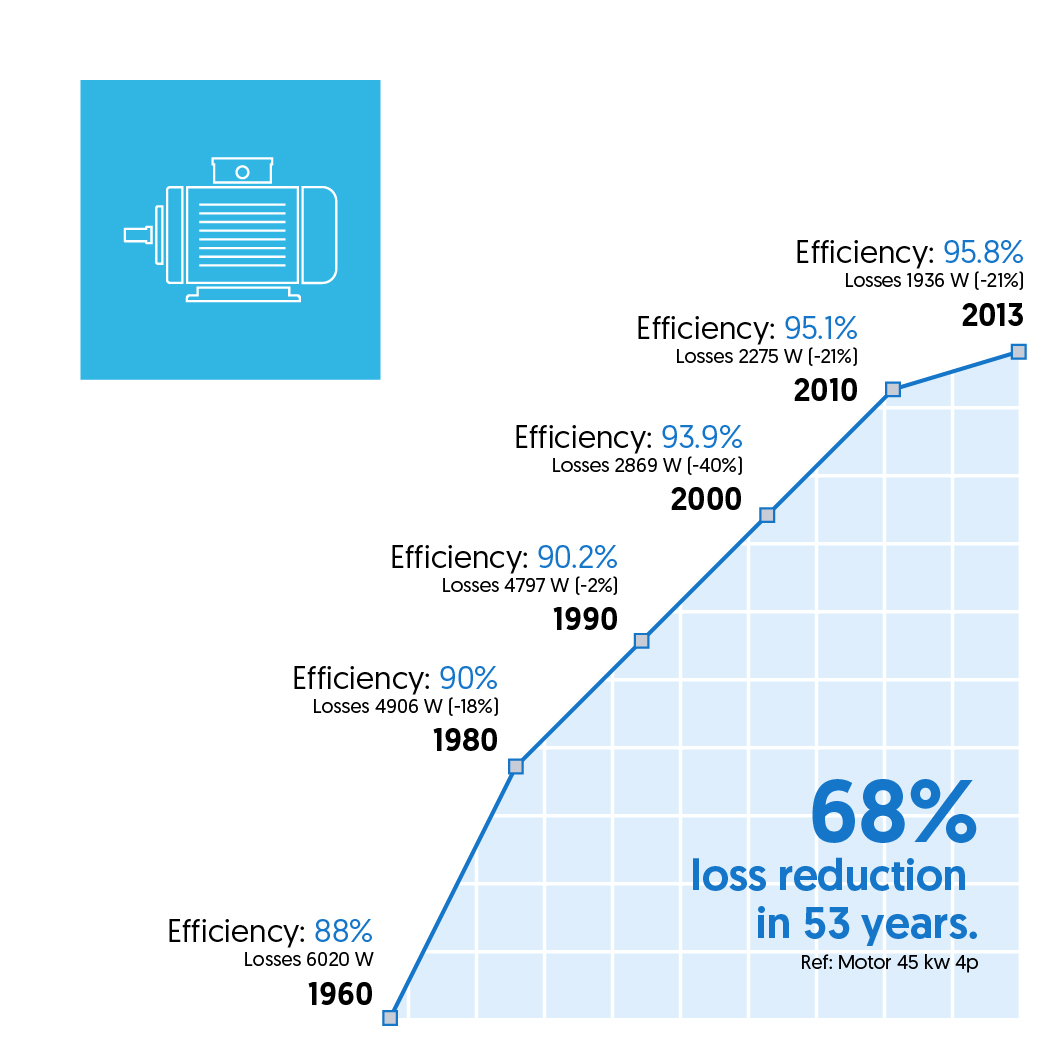
The energy loss with an IE5 motor will be approximately 20% lower than the loss with an IE4 motor. Our main supplier, WEG, can produce IE5 motors with the standard asynchronous technology for motor powers starting from 75kW.
These standards have been applied according to the European Ecodesign 2009/125/EC Directive which was established to specify requirements for the environmentally responsible design of energy-related products (ErPs).
Adhering to the latest legislation
The latest Ecodesign regulation to be introduced in October 2019 is EU 2019/1781. This outlines two phases for progressing energy efficiency levels further and applies to low-voltage induction electric motors rated at less than 1,000 V alternating current (AC) and to variable speed drives (VSD) – also known as frequency inverters. See figure 2 for an overview of the IE norms.
Making IE3 mandatory in Phase 1
In July 2021:
- It became mandatory for all 0.75kW – 1000kW motors, 2-4-6-8 pole, to meet the IE3 Premium Efficiency rating. It is no longer possible to combine an IE2 motor with VSD to achieve the IE3 efficiency levels.
- The regulation covers 3-phase single-speed motors 50 Hz, 60 Hz, 50/60 Hz for direct-on-line operation with continuous duty defined as S3 ≥ 80% and S6 ≥ 80%.
- The regulation also applies to motors that have previously been exempt, for example, ATEX motors with protection types EX ec, EX d, Ex de, Ext, motors with IC418 cooling, and break motors with external brake.
- IE2 efficiency levels are mandatory for 3-phase motors with rated output from 0.12 kW and below 0.75 kW.
- It is also compulsory for all VSDs between 0.12 and 1,000 kW to have a power loss corresponding to a minimum of IE2.
There are a few exceptions to this, as set out in figure 2.
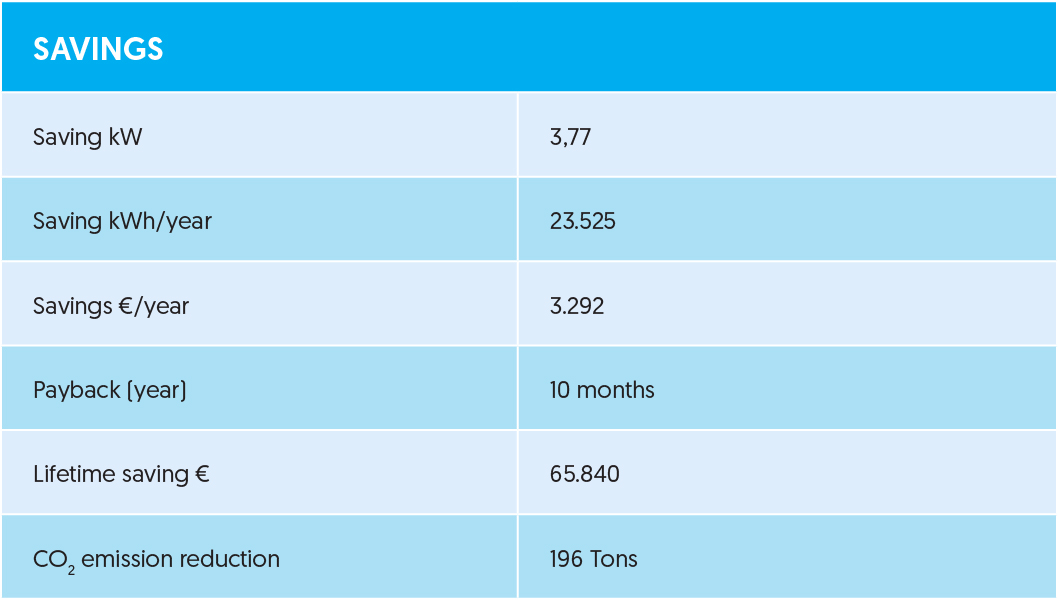
Figure 2 – Savings calculated by replacing an old motor with a more efficient IE3-rated motor
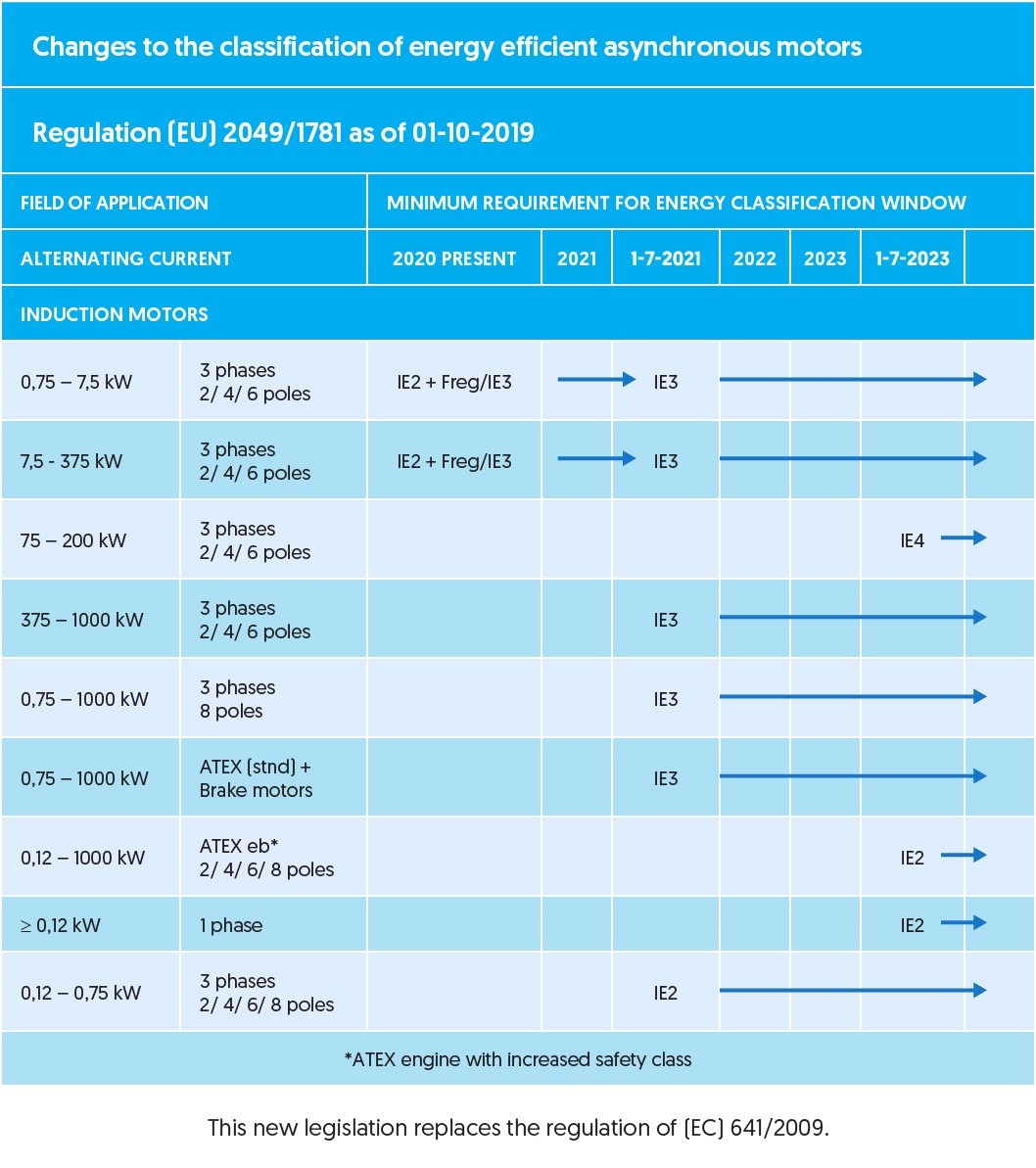
Figure 3 – An overview of the IE norms
Pushing efficiencies higher in Phase 2
The second stage of the regulation will come into effect in July 2023, when it will be mandatory for:
- all 75kW – 200kW motors, 2-4-6 pole, to meet the IE4 Super Premium Efficiency.
- single-phase and Ex eb safety motors from 0.12 to 1000 kW to meet IE2 efficiency ratings.
While IE3 is now the legal requirement, you should consider the return on investment (ROI) of IE3-rated motors vs IE4-rated motors. IE4-rated motors have a slightly higher initial investment, yet the system provides better value and it would pay for itself easily in savings made from energy costs. In fact, it has a similar ROI to an IE3-rated motor. After the motor has paid for itself, it would continue to deliver significant energy saving costs year-on-year, far outweighing those gained from an IE3 motor.
By going above and beyond current regulations means that as well as saving as much energy as possible, your system would be future-proofed for any further legislation changes.
The value of total cost of ownership
As such a vast percentage – 97% – of the TCO is entirely down to the cost of electrical energy, it is clear that this is where you can make most gains. Considering TCO rather than just the initial investment is vital for making cost savings.
For example, the cost of a typical IE4 55 kW 4-pole motor is €3,264, yet the energy cost for running that motor 24/7 is a staggering €50,206.90 (assuming an energy cost of 0.1 €/kWh (see figure 4).
You may be tempted to opt for equipment with the lowest capital cost as it is seemingly seen as a ‘better deal’. However, such immediate cost savings may prove to be detrimental to profits. Considering higher energy efficient products, means that life cycle costs are reduced, improving cash flow in the longer term.
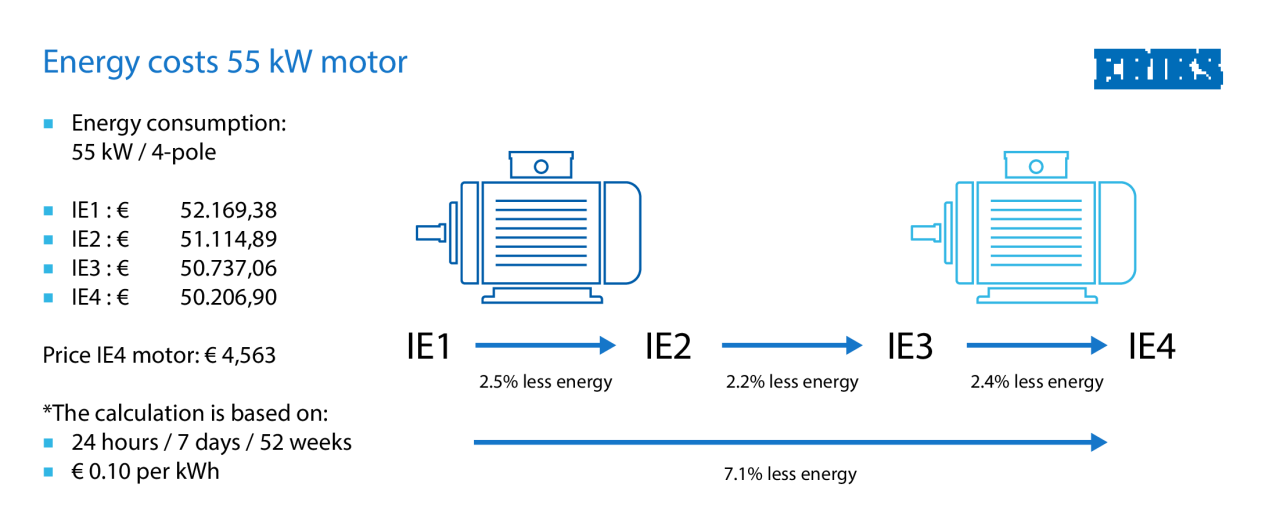
Figure 4 – the running costs of motors
Online TCO calculators provide the answers
Calculating the TCO enables you to make informed decisions on the most cost-effective motor solution. While working out TCO has traditionally been challenging, the development of online TCO calculators means you can now have all the information at your fingertips more easily. For example, the ERIKS TCO Motor Calculator takes into account the application’s running hours and energy costs and gives a clear comparison of repair, replace and upgrade options.
Figure 5 shows a comparison of motors using ERIKS TCO Motor calculator. If you stipulate a motor needs to operate for 22 hours per day, 365 days per year and at 100% load, with an expected lifespan of 15 years and energy cost is 0.08 €/kWh, the calculator provides the two best options of motor. In this case, an IE4 motor provides lifetime cost savings of €26,422.90 and an ROI of 1.5 years and an IE3 motor would deliver a lifetime saving of €22,148.29 and ROI payback of 1.4 years.
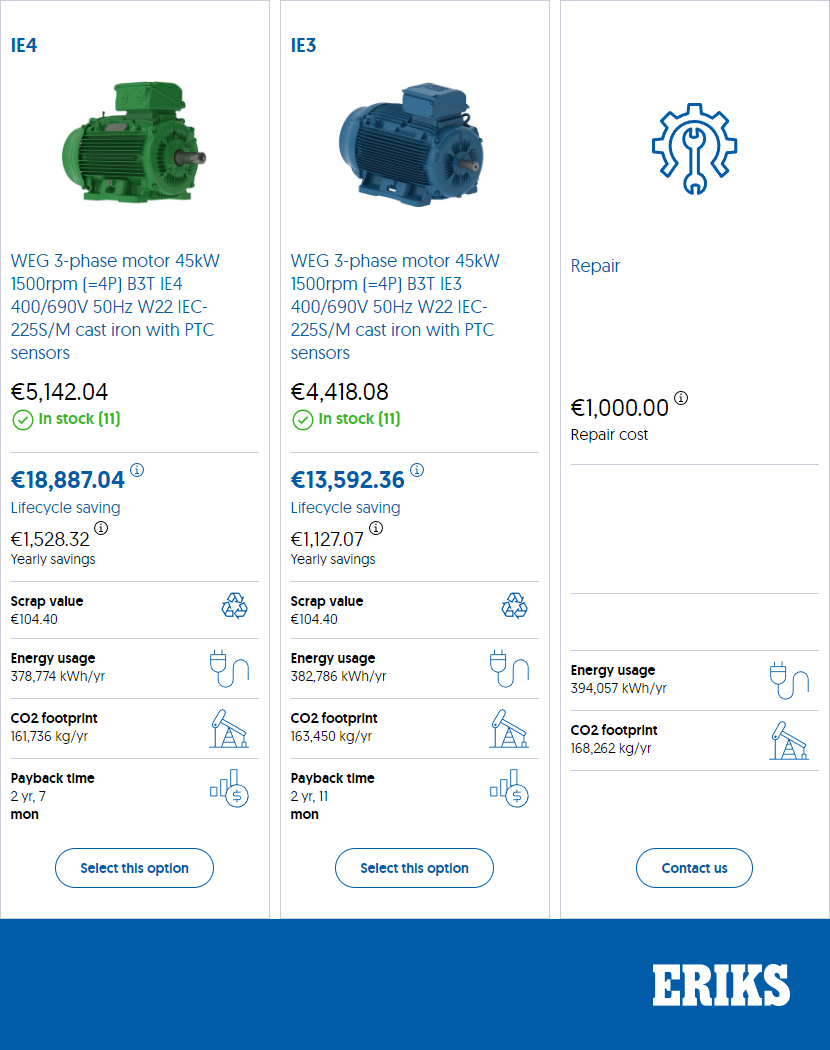
Figure 5 – ERIKS TCO calculator example
Repair vs replace
When a motor fails, repair is often considered initially. This is often seen as a quick-fix and can seemingly cost significantly less than a new motor at first glance (depending on the repair necessary).
However, this could be a false economy a 20-year-old motor that needs regular maintenance and repair will cost you more in the long term. Swapping an older motor with a more modern one, that has been built with energy efficiency in mind, will pay dividends in the long run. If your motor fails, you will need to repair it anyway, or buy a new one. The minimal investment you will need to make is the repair cost. So, if you should choose to buy a new motor, you can subtract the repair cost from the price of the new motor, reducing the total amount of the investment you need to earn back, thus improving the ROI.
For example, in a food industry application, replacing an old fan motor with a newer, more efficient one, proved to have a pay-back of only 10 months and be more cost effective. The existing motor had a power of 110 kw and an efficiency of 91.6%, and was going to cost €3,950 to repair. The new WEG 90kW IE3 motor had an efficiency of 95.6% and investment cost of €6,745. The savings, as shown in figure 6, were calculated to be €65,840 over the lifetime of the motor, and CO2 emissions of 196 Tons.
Additional factors for reducing costs
Selecting the right motor is key to improving reliability and energy-efficiency, but there are also other ways to reduce energy consumption and maintenance costs. The complete drive-chain should also be looked at to have maximum impact on cost savings. Working with trusted partners who have full knowledge of the most energy efficient solutions can pay dividends when it comes to understanding where savings can best be made.
For example, VSDs can play a major role in enhancing efficiency while ensuring reliable performance and reducing maintenance costs. Investing in highly-efficient electric motors combined with VSDs can translate into operational savings as large as 20%.
The largest savings can be made with quadratic torque applications, such as centrifugal pumps or fans where the flow is regulated with a throttle valve. By mitigating the throttle valve, and regulating the motor speed with an inverter, we can achieve enormous savings. Much higher than improving the motor efficiency. ERIKS can assist in calculating these savings and the associated ROI, as well as performing the change.
The significance of sizing
Moreover, it is important to review the motor sizing to check whether the right equipment is being used for the job. For example, does the application have the right size motor, or can a smaller, more efficient one be used instead? Power analyzers are critical here. They can be used to measure the power that is actually required in the system, so the motors can be sized accordingly. The reason for this, is that the efficiency of an electric motor drops exponentially when the load gets below 70% of the nominal load. Mainly in the past, but still today, manufacturers tend to oversize the motor because they don’t want to take any risks.
Also, we can look at other drive train elements that consume energy and reduce the overall efficiency. Chains and belts are often not perfectly dimensioned, and sometimes even not necessary at all. It is possible to analyse the entire drive train and propose the ideal setup in regard to the customer’s needs.
In one application at a dairy company, a 30-year-old 132kW 4-pole motor was used to run a cooling compressor. However, a power analyser showed that the motor only had a power consumption of 88.9kW. The motor ran for 8,000 hours per year with a total energy consumption of 711,200 kWh. The electricity cost was 0.06 ct/kWh, and resulting total energy costs were €42,672 per year.
Since the power analyser proved that the motor required only approximately 90kW, the company upgraded their motor to a smaller and more energy-efficient IE3-rated 90kW one. After installation a new energy measurement was taken. This showed the power consumption was reduced even further, to 82.5kW. Total energy consumption was now calculated as 660,000 kWh with at a cost of €39,600 per year.
As a result of investing in a new, smaller, IE3 motor the company was able to save a staggering €3,072 per year. The ROI was 1.92 years.
Conclusion
Improving the energy efficiency of electric motors can have a great effect on global energy consumption and therefore reduce CO2 emissions and save on running costs.
Although legislation exists to ensure manufacturers operate motors with high energy efficiency, many industrial companies are also striving to meet their own sustainability KPIs to operate as efficiently as possible. Reviewing the motors used throughout processes can go a long way to help you achieve these goals.
There is no one-size-fits-all solution to selecting the most energy-efficient motor and system, and liaising with specialists enables you to gain the most benefits. Access to the right expertise, engineering know-how and an impartial view are all that is needed to find a more sustainable and cost-effective solution.
Let’s face it, who wouldn’t want to save thousands of Euros every year, simply by replacing a motor. But where do you start? Our engineers can help you find the right motor, with the right norm, the right power output, and the highest savings on energy costs.
Subscribe to our newsletter:
For the latest industry news and updates.