In this article
Rapid prototyping: building confidence for OEMs
It seems like an obvious choice. When you have to choose between wasting 2 months and €20.000 developing a mould with errors or 1 week and €500 developing a prototype with errors? Seems is the right word here, because in many cases the first option is chosen. Many OEMs don't use the power of rapid prototyping to decrease risk, increase the quality of the final product, and even decrease costs.
Rapid prototyping - An underappreciated process
Why do many companies choose to skip prototype development and go straight to mould development? Why would they risk thousands of euros and months of development time? Mainly, due to two reasons:
- Underestimation of the power of rapid prototyping
- Rapid prototyping is seen as a time-consumer and cost-increaser, instead of a time- and cost-saver
Each of these reasons does not have to be an issue, if handled correctly. How? That will be addressed throughout this guide.
The what of rapid prototyping
Before diving into addressing the misunderstandings of rapid prototyping, let's dissect exactly what rapid prototyping is. In essence, rapid prototyping allows you to create a physical (scale) model of a part or an assembly. You do this using a CAD drawing and a method such as 3D printing or CNCing to create the part.
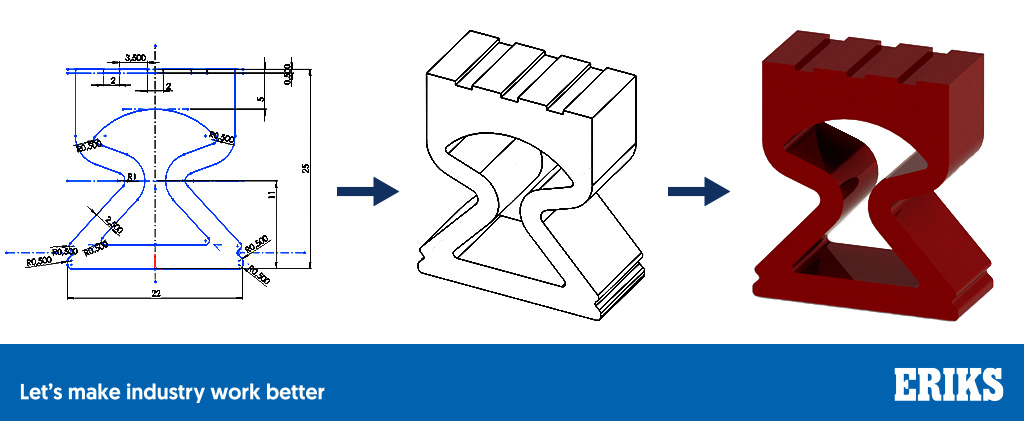
The practical side
The rapid in rapid prototyping refers to the speed with which prototypes are produced. With the use of different product techniques you can quickly make prototypes and iterate on them. Getting prototypes from a mould can take weeks, whereas with rapid prototyping it can be done in a matter of days.
Prototyping starts with thoroughly defining the needs for the specific part and any adjacent demands. The prototypes are then used to verify the assumptions on paper with a real-life model. You can detect any faults, create iterations, and fix any issues. This helps create a robust product and take the first steps towards a capable production process.
As mentioned, in its most basic form rapid prototyping requires no more than a CAD drawing and a method to create the physical model. However, to get the most out of rapid prototyping, you need a complete overview of requirements for the part:
- Product application/function of the product - For example, you need a product in a vacuum. But what is a vacuum and how do you generate that vacuum?
- Critical aspects of the product - This can be a lip seal where the lip has to be at an exact angle
- Required documentation - Product info, work instructions, etc
- Norms/standard/certificates - Food grade, medical, etc
- Quality requirements - Surface finish, color type and consistency, 1 in 1000 products can have a defect
- Delivery requirements - How do you ensure faultless delivery
Gathering these requirements helps you to make the most of the concept of rapid prototyping and reach the true goal of this technique. The drawing allows you to create the prototype, whereas the requirements allow you to verify the prototype. It's important to remember that a drawing is a summary of all choices and assumptions made when designing the part. Drawings often don't mention most of these. The requirements do.
The concept and goal
To truly understand the power of rapid prototyping, you first need to look at Design for Six Sigma. A design philosophy focused on maximizing product quality, and minimizing errors and time-to-market. DfSS is executed through several steps:
- Identifying issues in the design of the machine or component, while capturing all part demands, requirements, and influences
- Using simulations, such as Finite Element Analysis through computer simulations
- Developing prototypes and iterate on them by using rapid prototyping
- Creating a 0-series to test the production process
- Going into series production with confidence your parts and process are up to scratch
By developing prototypes, validating their form and function, and iterating you move into the 0-series stage with confidence. Confidence that you've eliminated any critical or show-stopping issues.
Rapid prototyping is therefore not a goal in its own. It's means to an end. The goal is to deliver a product that meets 3 criteria:
- High quality. To meet quality standards, the product must fall within quality parameters. Parameters that often require a ratio of 1:10,000 or even 1:100,000 when it comes to product faults.
- On time. Yes, rapid prototyping takes time, but less time than first developing a mould to deliver prototypes. It's a matter of 1 week versus 2-3 months. At the same time, finding and eliminating faults takes less time in this stage of the development process compared to when you're producing a 0-series or are in full production.
- Cost efficient. Whereas a single prototype will cost around €500, a mould can easily set you back €25.000 to €300.000. In addition, fixing faults is much cheaper during prototype development than during production, as it requires less rework.
The closer you get to the launch of a new product, the higher the effort becomes to fix any issues that are found. After launch, the effort becomes even greater. Identifying and correcting these issues early on is critical to prevent delays and additional costs later on.
Rapid prototyping - Much more than 3D printing
Rapid prototyping is often underestimated, because of how it is perceived. For many people, rapid prototyping is synonymous with 3D printing. You use a CAD drawing of your part to make a 3D print, and that 3D print is roughly accurate enough to test the form. This view is too narrow, since rapid prototyping is much more:
- A way to test form and function
- An opportunity to reduce costs and Total Cost of Ownership (TCO)
- An opportunity to identify production process improvements
Test form and function
Testing form is integral to rapid prototyping. Testing for fit is one of the main benefits of creating a prototype. In addition to fit, testing form also validates whether a product looks the way you intended and if you can install it.
The prototype turns a drawing into a real product. A drawing is not tangible, a prototype is.
Function testing is a recent development, especially when it comes to 3D printing. This is a huge leap forward in the applicability of rapid prototyping. It allows you to test mechanical and dynamic aspects of a product before moving into mould development.
Especially with materials that are sensitive to environmental influences, testing mechanical properties is crucial. Think about silicone, when this comes in contact with certain materials it can lose its mechanical properties. If you use a silicone seal with poor chemical resistance, you end up with leaks, malfunctions, and costly rework. Having the ability to test the material itself gives you certainty upfront.
Rapid prototyping allows for tests, such as:
- Material tests
- Strength tests
- Process tests (can we manufacture this?)
- Force tests
- Damping tests for vibration dampers
Each of these methods serves as a way to validate the quality of your product, find faults, and fix them in a time- and cost-efficient way.
Practical example - An almost powerless iPad
A drawing is not real, a prototype is. A perfect example of this came in the form of an iPad case. A hospital required terminals with iPads, which of course had to be secured, and the case was produced as a prototype.
What did ERIKS discover during prototyping? The manufacturer had forgotten to implement a slot in the bottom for the charger cable. A 2,5x8mm slot. Had this not been discovered in the prototype, it would have required redoing the mould, or cutting out the slot separately after production. Neither option is very efficient.
Reduce production costs and TCO
Preventing errors means preventing costs, but rapid prototyping does more than just preventing costs. It can be a way to actively reduce production costs, for example:
- Test a more cost effective material to see if this is a valid alternative
- Change the design to use less material and still generate the required functional properties
- Optimize the shape of the product, to reduce the complexity and costs of the mould
While these cost reductions are possible without the use of rapid prototyping, a prototype allows you to verify these decisions. Using less material can pose a huge risk if you do not test whether the product still functions. A prototype allows you to find the limit, without crossing it, in a low-risk way.
Practical example - Would you like your edges round or square?
Spotting cost reductions in rapid prototyping is often the result of an open discussion. If a drawing shows a component with angled corners, you can discuss why this is needed. Developing a mould with angled corners is more expensive than a mould with rounded corners.
If it turns out that it's for a food application, it's advantageous to use rounded corners since this prevents bacteria growth.
Improve the production process
The main focus of rapid prototyping is validating the product. But you can also use it to improve the production process. The improvements come in 2 forms: clearing roadblocks and finding optimizations. A true example of a roadblock is a welding robot that could not reach the welding seam due to the construction of the hose it needed to weld.
On the improvement side, a prototype allows you to answer questions such as:
- Can we remove any unnecessary steps in production?
- Can we combine separate parts into a single part?
Save development time and costs, build confidence
The second misconception about rapid prototyping is that it's a time-consumer and cost-increaser during development instead of a time- and cost-saver. This couldn't be farther from the truth. When creating a part that needs to be produced with a mould, rapid prototyping is the way to go. A prototype prevents having to redo a mould, costing you weeks and thousands of euros. A prototype that doesn't meet your criteria will cost you a week at most.
People that see rapid prototyping as a time-consumer will point to the fact that extra development time and money is involved. While this may be true, it creates a false dichotomy. Not investing upfront, can lead to much greater costs later on. Every engineer knows that eliminating faults from a machine becomes more time-consuming and costly the further you get in the development process. Let's not talk about the time and effort of rework post-launch.
When calculating the costs of rapid prototyping, the 'hidden costs' of not prototyping are often forgotten. A prototype is a fraction of the costs that are incurred when you calculate hours spent on rework, let alone missed or delayed revenue from missed release deadlines.
Verifying a product through rapid prototyping drastically reduces the chances of rework later on. It instills confidence in your design, prevents increased time-to-market, and reduces costs. It is for a reason that every sizable OEM uses rapid prototyping, from automakers like Volkswagen, to semicon companies such as ASML. Even in the MRO world, rapid prototyping is becoming more common. When a beverage company like Heineken introduces a new bottle shape, they will first test their production lines with prototypes of the final bottle.
Moving to the mould with confidence
When the prototype is stable on the critical criteria, you are ready to move on. You want to have answered the question: will this product do what you want it to do in the form you have designed it in? At the same time, you should also look at the production process.
The follow-up to rapid prototyping is the 0-series. Here, you create a demo mould that is used to test the production process of the parts. This demo mould is often made of a material that lasts long enough to finalize the 0-series, but is not robust enough to be used in series production. And whereas rapid prototyping is product focused, the 0-series is very process focused.
With the optimizations you made during the rapid prototyping phase, you can move on with confidence. Confident that there will be no surprises with regards to the form and function of the component. Confident that you won't incur rework, or experience delays because of unforeseen issues with your component. Confident that the 0-series will come out the way you want, without product flaws that will set you back weeks or months.
And in the end, that is what rapid prototyping is about, developing confidence in your product and process.
Frequently asked questions
What is rapid prototyping?
Rapid prototyping is the process of creating a tangible product and allows you to see things you don't see on a drawing. The prototype should represent the final product as best as possible, as soon as possible in the development. It will allow you to get feedback on the technical aspects of the product.
It's also about simply understanding what you are doing exactly and what the consequences of certain design choices are.
When is rapid prototyping the right choice?
There are 3 types of parts:
- Standard parts
- Customized parts
- Customer specific parts
Rapid prototyping is most valuable when creating customer specific parts that requires the use of a mould. It also provides valuable insights when using assemblies. In general, the higher the risk of a faulty part, the higher the added value of a prototype.
Are rapid prototyping and 3D printing the same?
No, rapid prototyping can be done with 3D printing, but 3D printing is not the only method to create prototypes. At the same time, not all 3D printed parts are rapid prototypes.
The main forms of rapid prototyping are:
- Additive manufacturing/3D printing
- CNC machining
- Plotting and cutting
- Vacuum forming - You first create the counter part using 3D printing and then with vacuum forming create the part.
What materials can be used to create a prototype?
To create a prototype that allows you to test both form and function, you need to produce it in its final material. This can be done with the following materials:
- Elastomers
- Plastics
- Metals
- Ceramics
- Fiber reinforced materials
The latter is a relatively new technique. Using carbon fiber and a CNC machine, you can create a prototype that achieves 80% of the strength of a final product.
Subscribe to our newsletter:
For the latest industry news and updates.