The 7 Key Factors to Select the Right Industrial Hose
Hoses aren’t usually a priority when designing a machine, but they should be. After all, just like tires aren’t the first consideration in automotive design, they’re essential to its operation. Hose selection is a complex process that requires you to strike the right balance between cost and performance. Keeping the performance requirements of the hose top of mind from the beginning will help avoid costly rework and keep your project on schedule.
The Hose Selection Process
Most important in the selection of a hose is making sure you have access to the right information. Do the materials you’re considering comply with legal, technical, and quality standards? Are there requirements to meet regarding documentation and traceability? It can also be an advantage to try out different options during the prototyping phase as you will more easily determine benefits and potential weaknesses.
To ensure you get exactly the right hose solution for your project, involve experts as soon as the engineering process commences. Even at the prototyping stage of a machine development project, an application engineer can offer valuable input.
So, what are the most important factors to consider when choosing the right hose for your industrial application?
The 7 Key Factors for Hose Selection
A widely used method to select the correct hose can be summed up in the acronym STAMPED: size, temperature, application, medium, pressure, ends and delivery. Note that these criteria do not stand alone; the combination of these internal and external factors is decisive when choosing the correct type of hose for your specific needs.
Size
DSizing is the most basic yet essential factor in industrial hose selection. Sizing specifications for industrial hoses include the hose’s inner and outer diameters, and length.
Inner diameter
The correct size will keep pressure loss to a minimum and avoid hose damage during heat generation or excessive turbulence. Inner diameter (ID) is the span of the empty space in a circular hose’s cross section. It is the most important factor in hose sizing because it affects the fluid’s flow velocity within the hose. A hose with an oversized ID will result in sluggish system performance, while an undersized ID can cause excessive pressure drops, leaks, and even system damage.
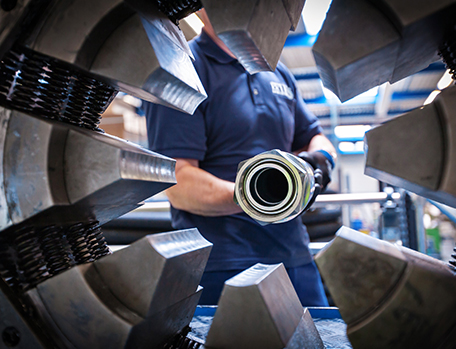
Outer diameter
Outer diameter (OD) measures the entire span of the hose cross section, including the inner tube, reinforcement, and outer cover. The difference between the OD and ID reveals the thickness of the hose wall. Outer diameter is important for sizing industrial hoses to appropriate fittings and system components.
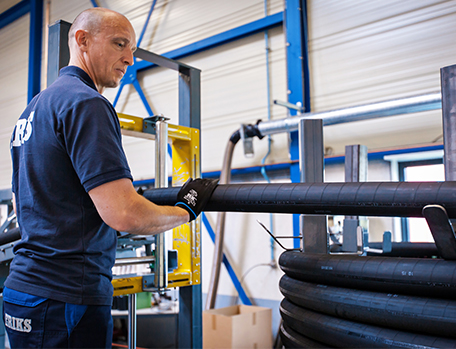
Length
The length of an industrial hose defines its maximum reach between end points. Increasing length can also increase pressure drop in the system, since hose length is a function of head loss due to friction. It is important to always cut a new hose to size. If it's too long, this can lead to extra bends and abrasions, which in turn can shorten the hose life. In addition, extra length incurs unnecessary costs. Conversely, if the hose is too short, you can damage the reinforcement and integrity of the assembly.
Temperature
When selecting a replacement assembly, two types of temperature must be considered: fluid temperature and ambient temperature. The hose selected must be capable of withstanding the minimum and maximum temperature encountered by the system.
Fluid temperature
Hose construction material is affected by temperature and operation time. A hose in an application operating at 200°C under a service pressure of 20 bars will need to be constructed from metal rather than elastomer. Material selection means considering the expected operating temperature and how long it will operate at that temperature.
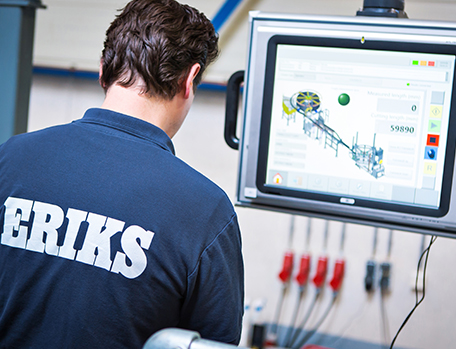
Ambient temperature
Extreme temperatures will impact on hose performance and can frequently be affected by internal and external influences, such as weather conditions, and factors like UV radiation or the temperature of the environment where the machine is situated.
Once you’ve established the pressure level required and expected operating time, any potential peak intervals and possible temperature fluctuations – particularly extremes – you will be one step closer to finding the ideal hose for the application.
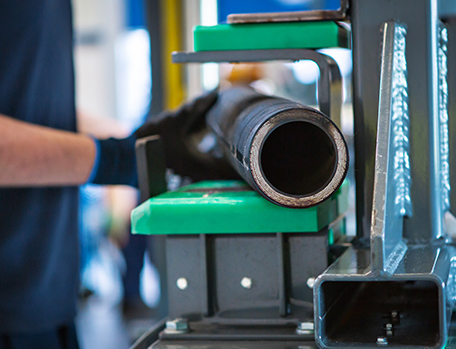
Application
Application refers to the usage requirements but also to environmental factors and industry standards. A wide variety of industry standards exist, which set specific product and performance requirements per industry and country. Standards include EN (European Norm), DIN (Deutsche Institute fur Normung) as well as the international ISO specifications for hoses and hose assemblies.
Medium
Medium refers to the substance that the hose will have to hold. A medium selection chart can guide you on which hoses are the best to use with a specific substance. For example, on this chart <link> you can choose the medium that the hose will have to handle and you will then be offered some possible choices.
Some applications require specialised oils or chemicals to be conveyed through the system. Hose selection must therefore ensure the hose tube, cover, couplings and O-rings are compatible with the fluid used.
Determine what kind of liquid (medium) will be used in the hose when the machine is in operation. Not all hoses tolerate the same media and hoses transporting certain fluids, such as milk, need to meet regulations. Similarly, water can be transported by a normal quality hose, but if the hose is later cleaned with another liquid like acid, it will not suffice. For example, a hose used for waste water was destroyed. The cause was initially unclear until it was discovered that some of the chemicals in the waste water were damaging to the hose material. A reputable supplier will submit a questionnaire for you to complete to avoid such issues. Chemical Resistance Guide.
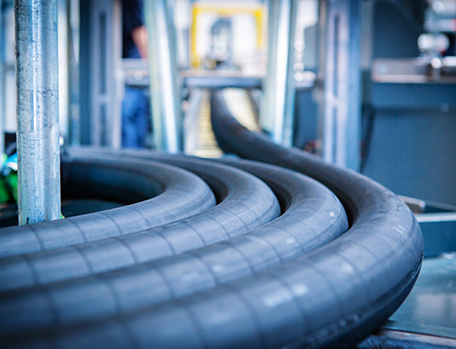
Pressure
Post installation, hoses can stand hundreds of bars but not all materials work optimally under high pressure. This can lead to reduced performance or even a burst. To define the ideal material, you need to establish the exact amount of pressure that will be applied to the hose as well as any spikes the application may incur.
Pressure also determines the bending radius. For instance, a high-pressure hose will require reinforcement around the inner ring, which will ensure it is more difficult to bend. A good supplier will be able to pressure test the expected service pressure the hose will need to cope with in the machine to avoid a burst and increase safety.
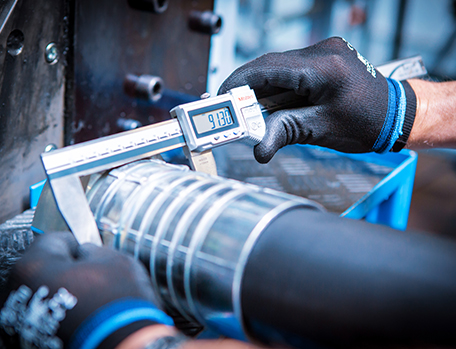
Ends
To avoid too many hose-coupling combinations, it’s a good idea to minimise the number of coupling ends or connections.
Today’s hose coupling combinations minimise waste water due to their reduced leakage risk and more secure connections, which also reduce air waste. Altogether, this increases operating sustainability. And, while recyclable hoses are still something for the future, you can still have a positive impact by improving the efficiency of current applications so that they produce less waste.
Delivery
A new system will require a new hose and an expert partner will be able to provide you with samples to test in-house. And, to ensure you determine the best solution before any final decisions are made, they will also be able to tell you what’s possible and what’s not. This will also apply to machines already in operation where replacement hoses are difficult to make.
Expert Guidance
If the area of application is critical, investing in a quality hose ultimately brings peace of mind and involving an expert early in your decision-making process will likely lead to savings. Bear in mind, however, that the definition of quality varies among suppliers and producers, as do the materials they use in production. This applies to both customised and off-the-shelf products, which is why it’s prudent to research suppliers and producers to find one best able to meet the needs of your particular project.
Related Articles
General contact ERIKS Global Head Office
Chamber of Commerce
37 01 32 89
VAT Number
NL003.076.490.B02
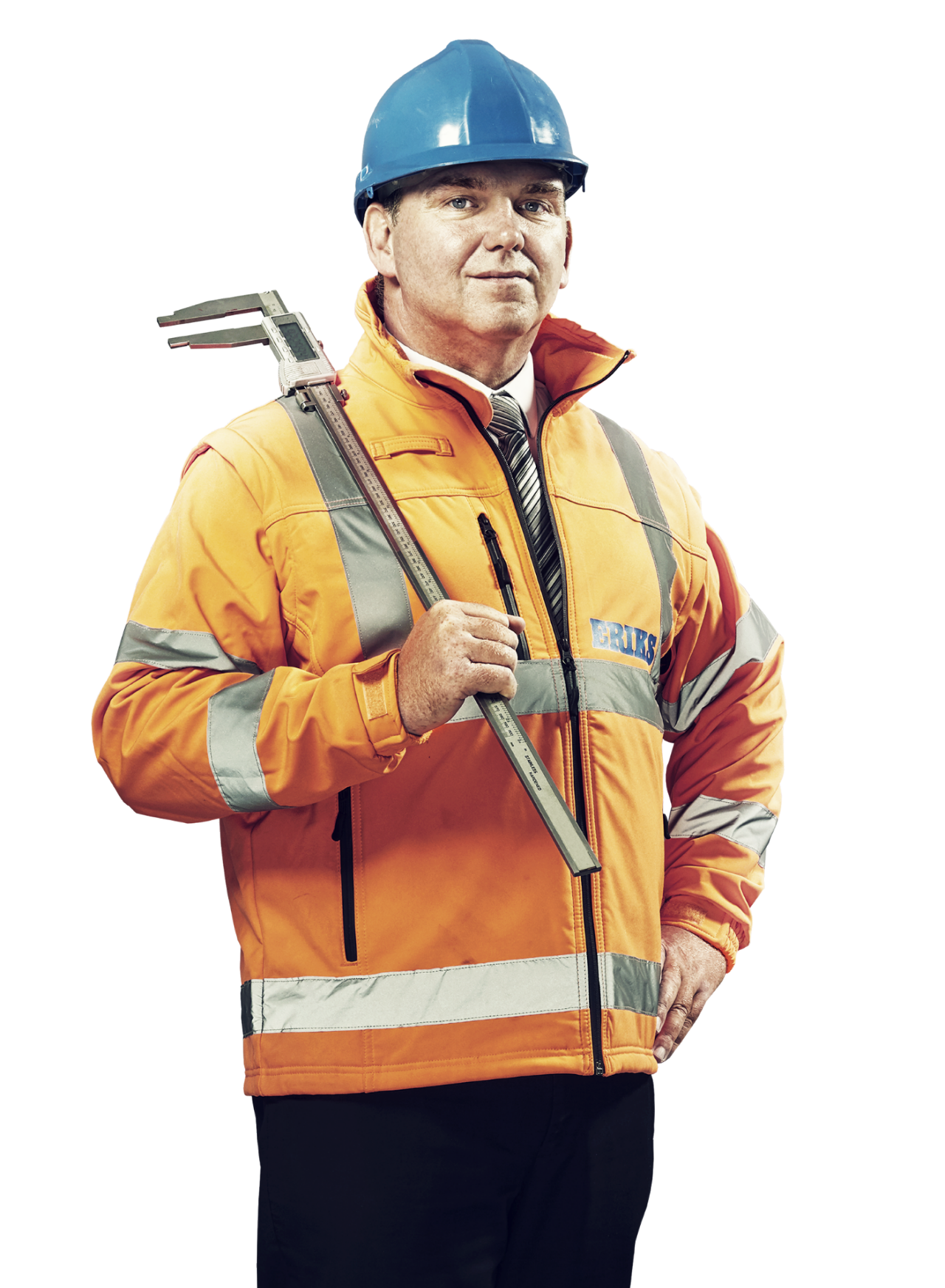