In this article
Innovations in Hydrogen-Compatible Material Development
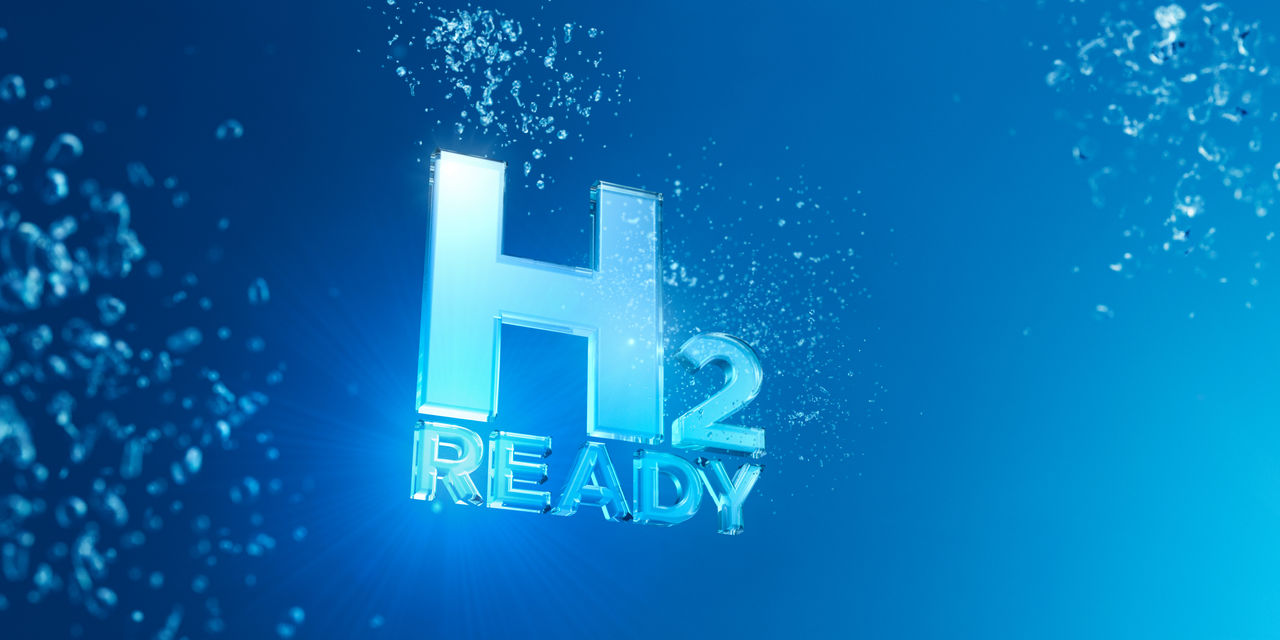
The ambition in the Netherlands is to be climate neutral by 2050. An important spearhead in this is to reduce the use of fossil fuels. Electrification in industry is already in full swing. The applications of hydrogen, which is seen as a future alternative to natural gas, are mostly in the development phase. In this article we take a closer look at the challenges of using hydrogen and how ERIKS contributes to developing products and materials that can be used in an industry with hydrogen applications.
Hydrogen is widely applicable within industry
The applications of hydrogen are found in multiple industrial sectors. And in addition, before you can use hydrogen in these applications, it has to be produced. We define four segments in which the developments of hydrogen applications are increasingly visible: OEM, which includes companies that develop devices and machines that allow you to produce, store, filter or store hydrogen. Transportation, where hydrogen is seen as the solution of the future to replace fossil fuel. HVAC is a third segment, where there is a strong ambition to develop boilers that run entirely on hydrogen. The final segment is EPC projects, in which plants are being developed for clients with the goal of making hydrogen.
What challenges does hydrogen bring?
The uses and applications of hydrogen are relatively new to everyone. Consequently, it is not always known exactly how hydrogen reacts to (a combination of) certain production factors. And whether it is at all possible to apply hydrogen in a particular production environment. This is where the first challenge lies. Indeed, within each sector, standards determine what a device or component must meet, what the requirements are. That gives direction to the end result, because as a machine builder you can then be sure that you are making something that is suitable for a particular application. This is still lacking for hydrogen. But we are currently working hard to realize this in the short term.
Another major challenge is the availability of hydrogen. Partly because of the lack of standardization, uncertainties about the effects within certain applications and the currently very cost-intensive way to produce hydrogen, it is not yet widely available.
A third challenge is more technical. Hydrogen is the smallest molecule we know. For example, sealing such a small molecule is just very difficult because it easily passes through something. A standard indicates the permissible amount of hydrogen that is allowed to pass through certain material. When research into permeability reveals how much that is, then you can work specifically with certain materials. As long as there is no such standard, it will often remain an estimate based on personal knowledge and experience of what is and what is not possible.
Testing for the permeability of hydrogen
Boiler construction is an industry in which materials testing is of great importance. In particular, boilers contain many rubber parts, all of which must be suitable for allowing no or only minimal amounts of hydrogen to pass through. One of the parts commonly found in boilers are seals. Until recently, little was known about the permeability of rubbers in relation to hydrogen. Therefore, ERIKS has also tested four important materials, already used for critical seals within boilers, for hydrogen permeability. The results from the test show very low permeability for these materials.
With this data, a boiler builder can calculate permeability at multiple temperatures. One can also use these data and calculations to demonstrate that seals made from these materials are suitable for applications in a boiler. It should be noted, however, that the studies we have seen so far have still been conducted at fairly low pressures, below 30 bar. Many applications are still conceivable where the pressures are many times higher. When we start working with such applications, new studies will certainly have to follow to see what effect this has on permeability.
Total requirements for proper material development
Permeability is not the only factor in the composition of the right material within a hydrogen application. In consultation with major market players, who are actively engaged in the energy transition and are developing products and technologies for this purpose, we are looking at what materials are needed. And how these are ultimately applied in the product. In addition to permeation requirements, other parameters such as temperature, pressure, chemical and electrical insulation also play a role. Together, these factors determine what the composition of the material will be and what resistance and mechanical properties are required of the material. From this, we can draw up a set of requirements and we start working at Elastomer Research Testing on a recipe with which we perform the initial tests. We make multiple enhancements to the material before integrating it into products for customer field testing. Upon customer validation, this can be converted into an ERIKS compound.
ERIKS as a forerunner in hydrogen development
ERIKS' sustainability strategy is to future-proof the industry. That is why we are working on a range of products suitable for making the transition to hydrogen. ERIKS is by far the largest in the field of product and material development. In combination with the know-how available in companies operating internationally under the ERIKS umbrella, we are working hard to raise awareness of hydrogen applications in Europe. We have already launched various projects to this end in various countries.
ERIKS' added value is mainly in the design and development of materials that are suitable for hydrogen applications. In addition, we often join machine and equipment manufacturers in the design phase to help them think about how materials can best be integrated into the design. For example, in order to anticipate the different production environments in which hydrogen will be used, ERIKS has already developed a range of materials that can be used or are close to being introduced. If we succeed in having more ERIKS compound numbers incorporated into OEM designs, we'll pave the way for a more sustainable future in hydrogen applications within the industry.
Subscribe to our newsletter:
For the latest industry news and updates.