In this article
The Ultimate O-Ring Guide
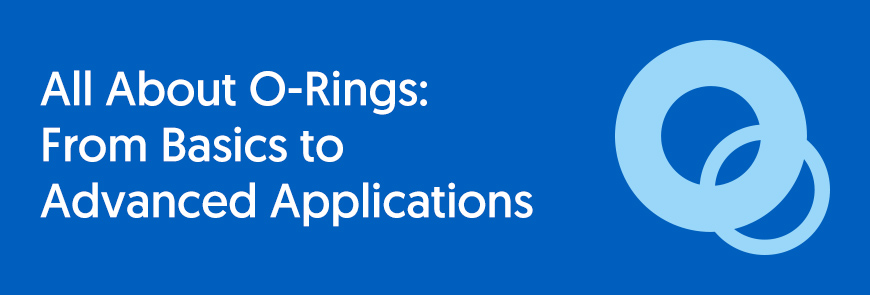
O-rings are highly versatile and widely used as a sealing solution due to their efficiency, affordability, and ease of use in both static and dynamic applications. They are crafted from a wide range of elastomer materials, capable of sealing practically any liquid or gas.
Designing and producing O-rings requires careful consideration of several factors, including quality, quantity, application environment, cost-effectiveness, chemical and pressure compatibility, longevity, and lubrication requirements.
The Versatility of O-ring Seals
O-rings are versatile seals, typically elastomeric but also available in materials such as PTFE or metal, exhibiting a bi-directional, circular design. They function by deforming their material under installation and media pressure to effectively seal gaps between mating components.
However, these seals are not impervious to issues. High system pressures can lead to a phenomenon known as extrusion, where the seal material deforms into the gap, resulting in seal failure. This issue can be mitigated by employing harder seal materials or introducing back-up rings for support.
The strength of an O-ring lies in its ability to behave like a highly viscous fluid under pressure, creating a positive barrier against the medium it's designed to seal. This unique attribute, coupled with its capacity to revert to its original shape post-deflection, makes O-rings invaluable in sealing applications.
Additionally, the O-ring's elastomeric nature allows it to adapt to unit tolerance variations, maintaining a sealed condition. The squeeze, or the degree of compression, is a crucial factor in the design of O-ring seals. For O-rings with smaller cross sections, a higher degree of squeeze is needed to counterbalance larger groove dimension tolerances.
Applications affecting the O-ring
O-rings can be successfully used in static as well as dynamic applications. A seal that does not move, except for pulsation caused by cycle pressure, is called a static seal.
Static applications
There are four varieties of static applications: axial, radial, dovetail and boss seals.
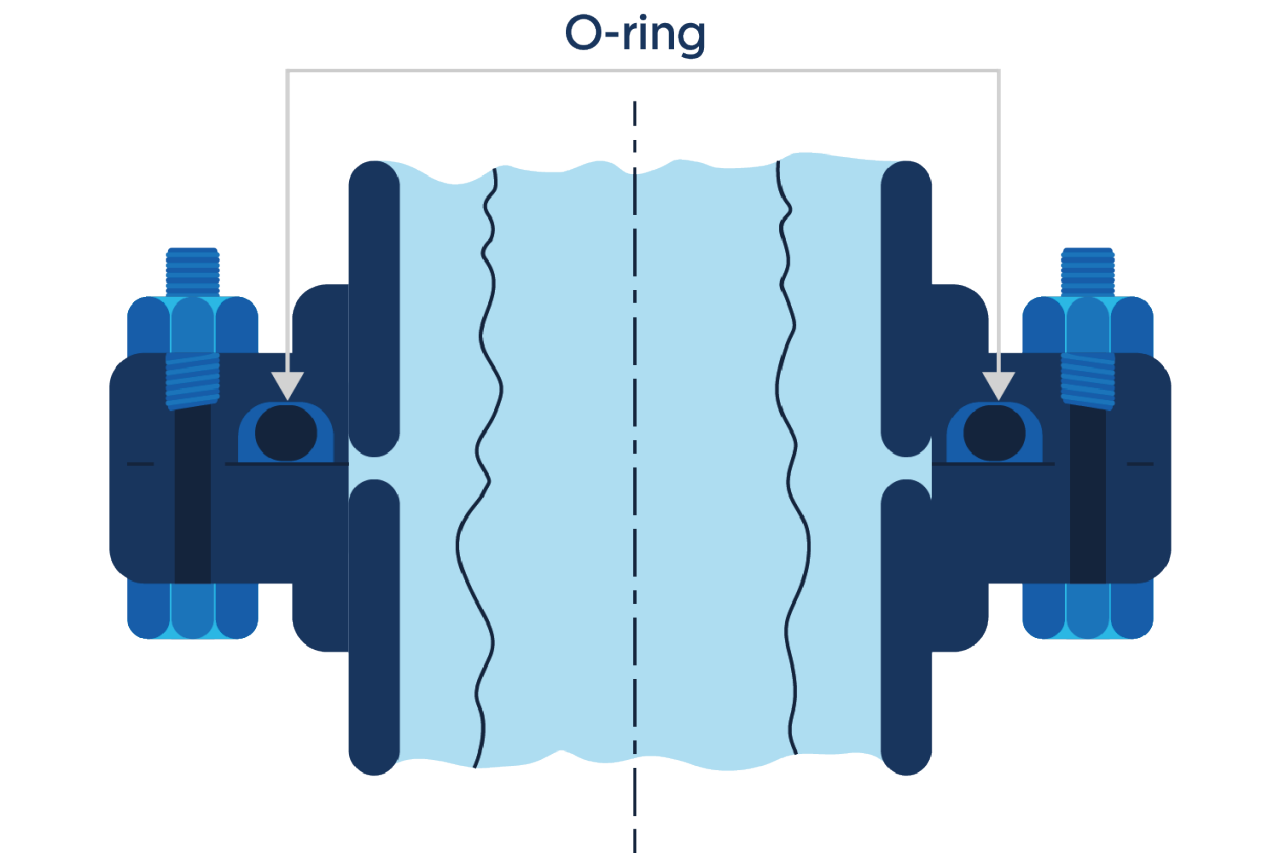
Axial
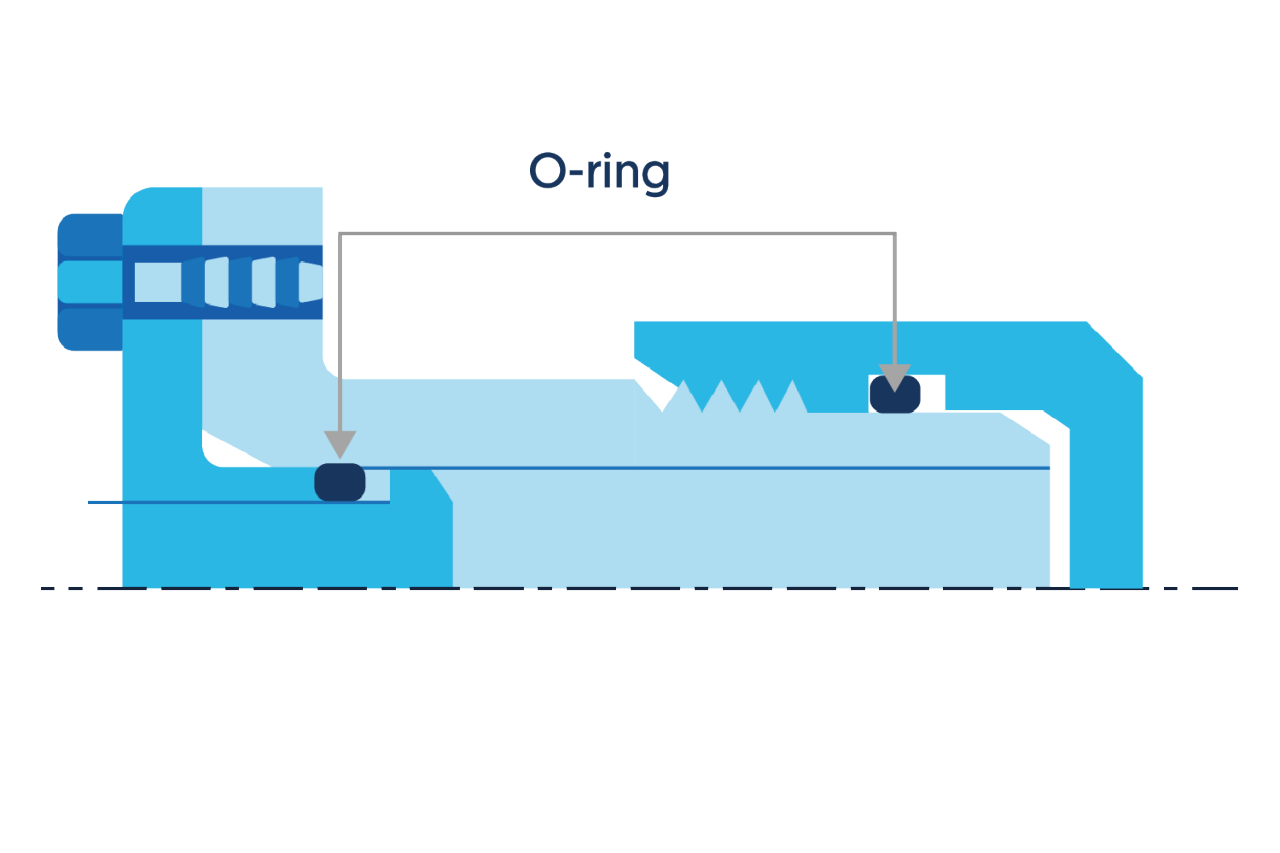
Radial
The O-ring cross section is squeezed radially in the groove between the inside (ID) and outside (OD).
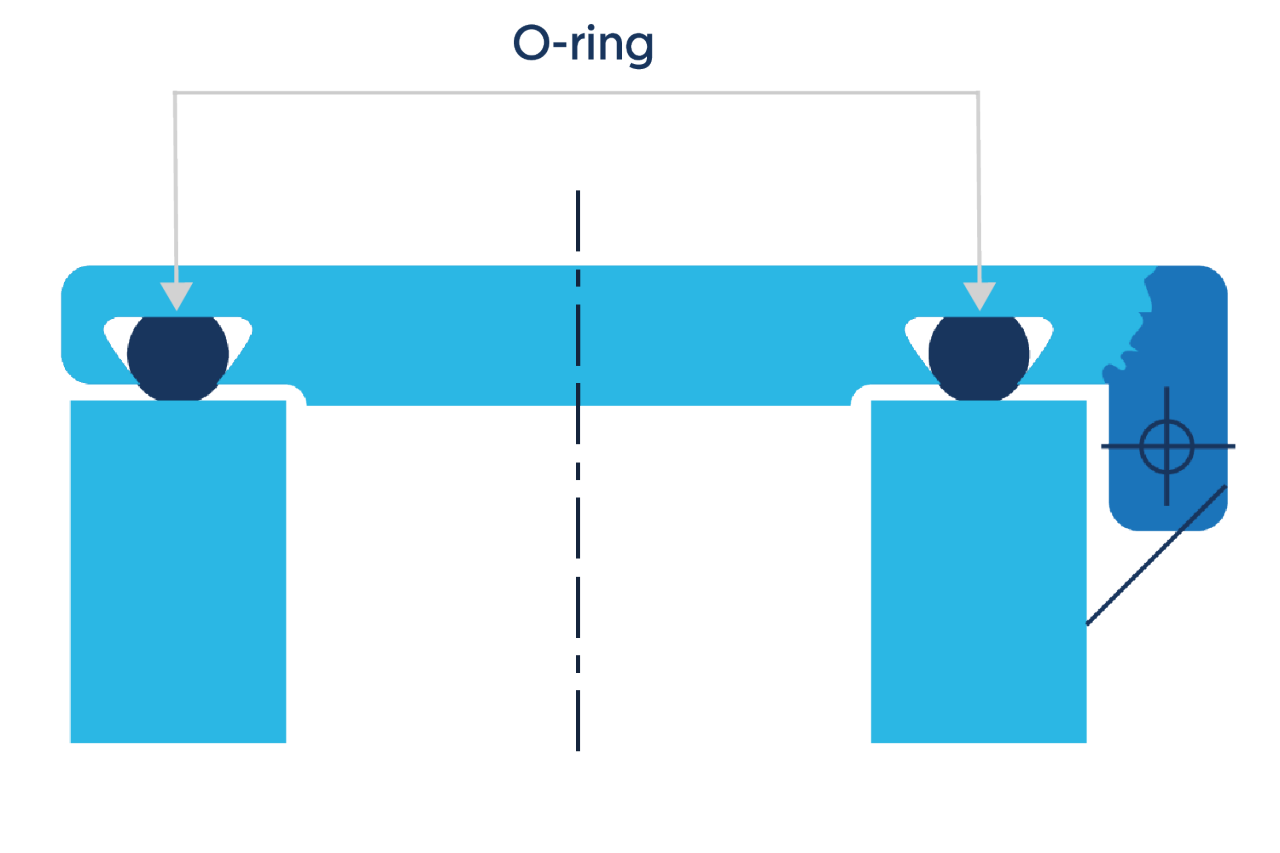
Dovetail
The O-ring is also axially squeezed in a dovetail groove.The groove design allows the O-ring to be retained in the face seal during assembly and maintenance.
This is beneficial for special applications where the O-ring has to be fixed by the groove e.g. a lid which opens regularly.
Bosstail The O-ring is used for sealing straight thread tube fittings in a boss.A boss is a cylindrical projection on a casting or forging. The end of that projection is machined to provide a flat, smooth surface for sealing.Straight threads used with an O-ring provide a better seal than tapered threads used alone.
Dynamic applications
Seals that are subjected to movement are dynamic seals. These are further defined as reciprocating (seals exposed to linear motion), rotary (stationary seals exposed to a rotating shaft) and oscillating.
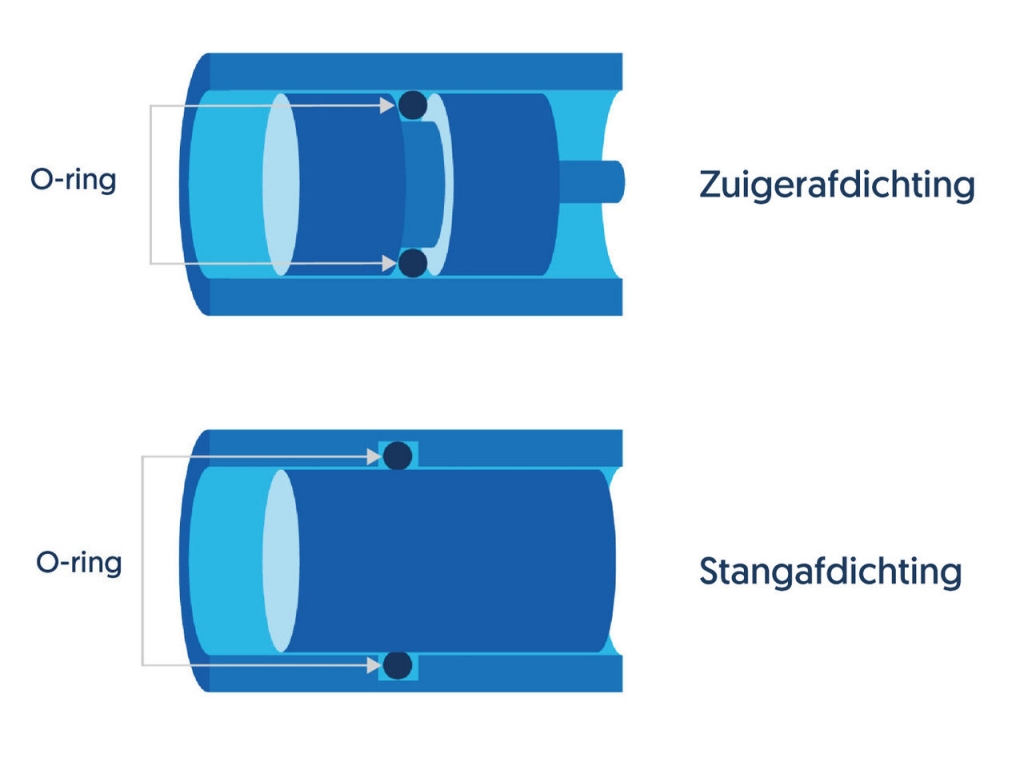
Reciprocating
Seals used in applications that slide back and forth.This motion introduces friction, which creates design considerations different from those of static seals.
The O-ring may be housed in a groove (rod seal) in the cylinder wall instead of a groove in the piston surface (piston seal) without any change in design limitations or seal performance.
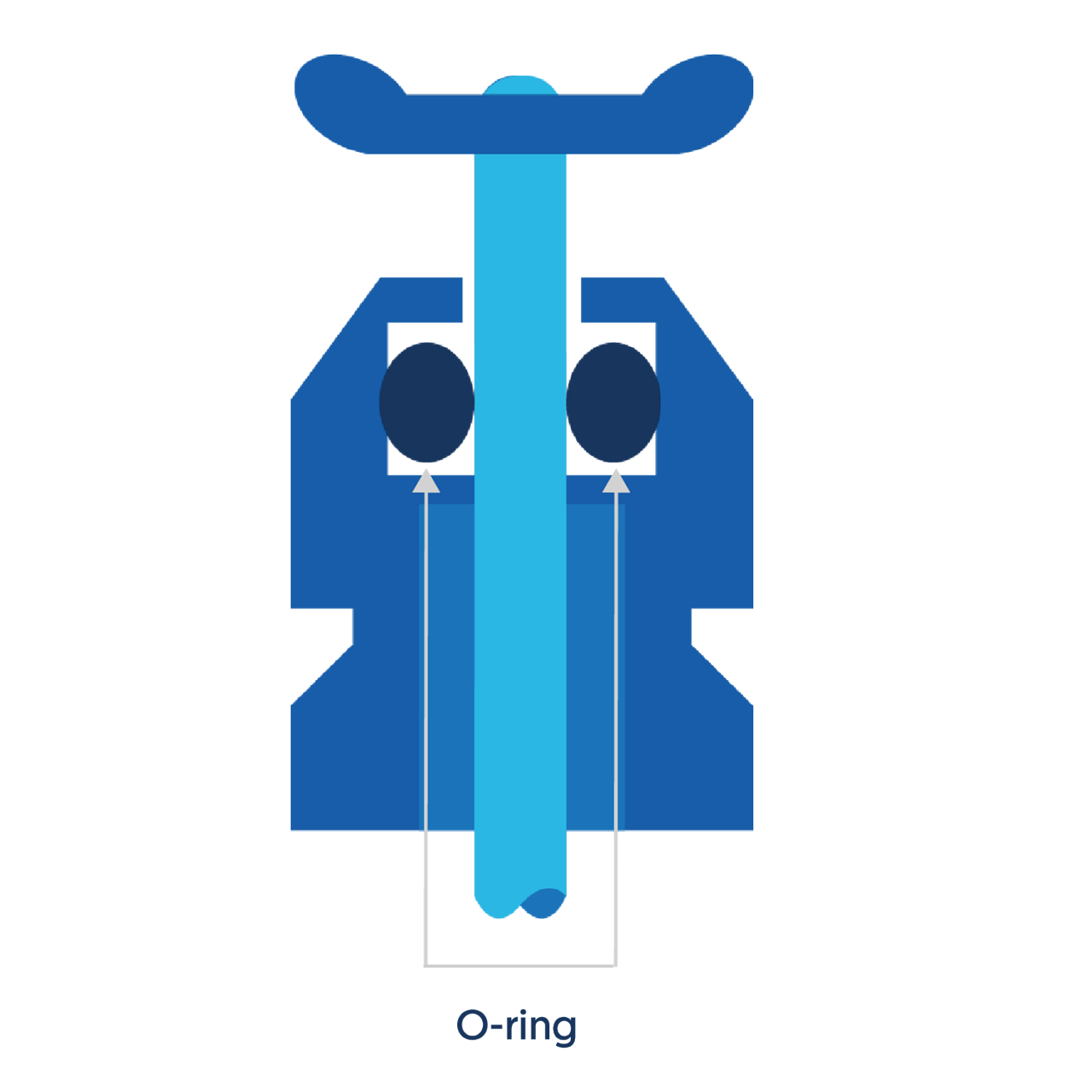
Oscillating
Oscillating applications are those seeing both rotary and reciprocating movement.
A valve spindle is an example of an oscillating application.
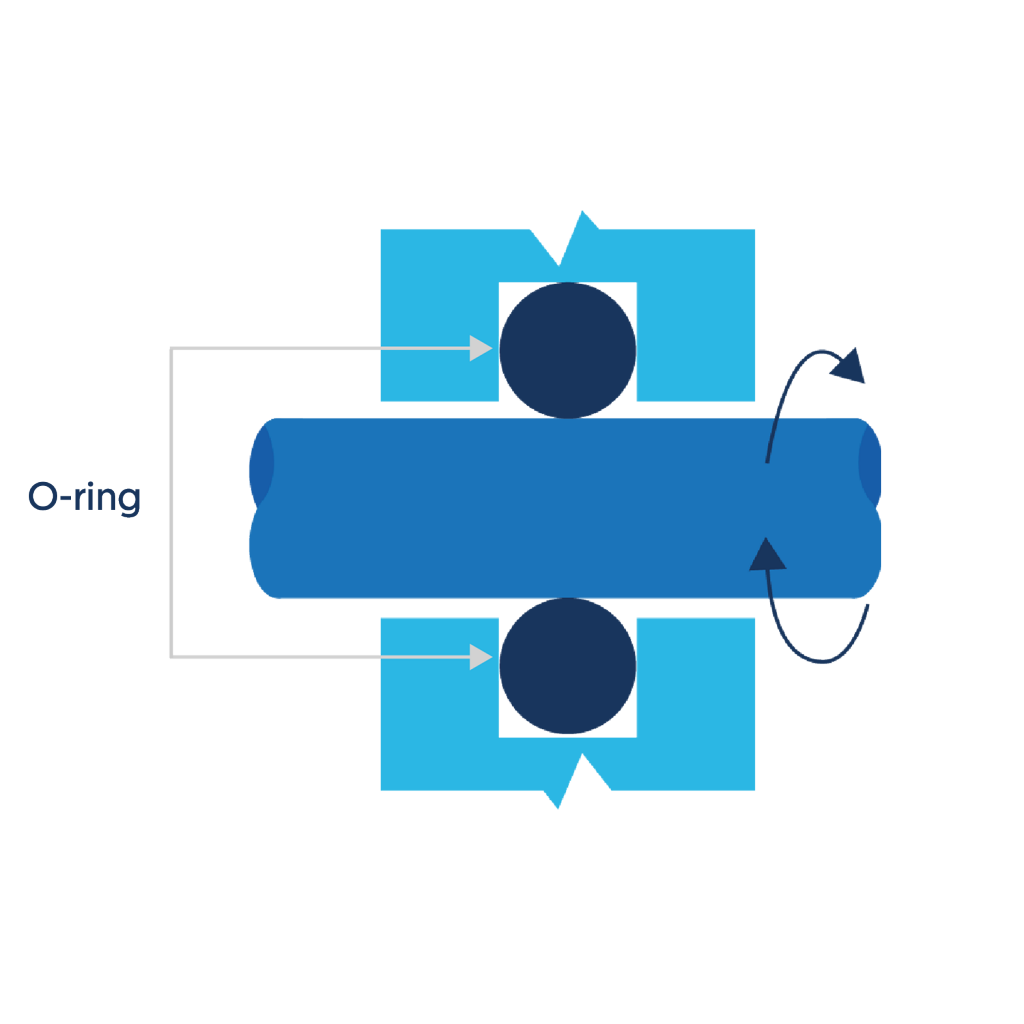
Rotary
Rotary seals refer to seals used in applications that rotate.

O-ring Selection
O-ring groove and size
Calculating O-ring groove and size
It is important to know how deep and wide the groove is into which the O-ring will go. Otherwise, an O-ring size cannot be determined properly. Usually, you have already calculated the groove for the O-ring before choosing an O-ring.
The following is important to consider when calculating the O-ring size & O-ring groove:
Make sure the width of the groove is greater than the depth, i.e. your groove is rectangular and not square. This is because an O-ring is usually pressed into the groove from above (axially). Since an O-ring is not compressible, but deformable, it must be able to release its volume. Free space in the groove is therefore essential. If the groove is not wide enough, the O-ring is pressed squarely and the material loses sealing capacity.
The diameter of the O-ring should be at least 15% smaller than the space of the groove. If this margin is smaller, the risk of damage to the O-ring increases.
Read more about Determining the right o-ring dimensions for your application
The O-ring calculator
Are you calculating the depth of the O-ring groove? Your groove depth determines the compression of your O-ring. Always include the gap space (clearance gap) in your calculations. An O-ring groove should be rectangular.
Do you want to calculate the O-ring and groove size yourself?
The O-ring calculator will help you calculate O-ring and groove sizes.
Indentation - Compression
An important consideration when choosing the right O-ring is the indentation, or compression ratio. Too high a compression ratio can lead to damage, while too low a compression ratio will cause the O-ring to seal inadequately.
Incidentally, compression rate should not be confused with the term Compression Set. The compression rate indicates the deformation of the O-ring, while the Compression Set indicates the elastic memory of the material.
Recommended indentation
The recommended indentation is 15 to 25% in static applications. In vacuum applications, pressures can be even higher. Pressing at more than 25% creates additional stress for an O-ring. This can lead to premature damage.
In dynamic applications the recommended compression rate is 8 to 16%. Due to friction and wear, smaller cross-sections are compressed by up to 20%.

O-ring material selection
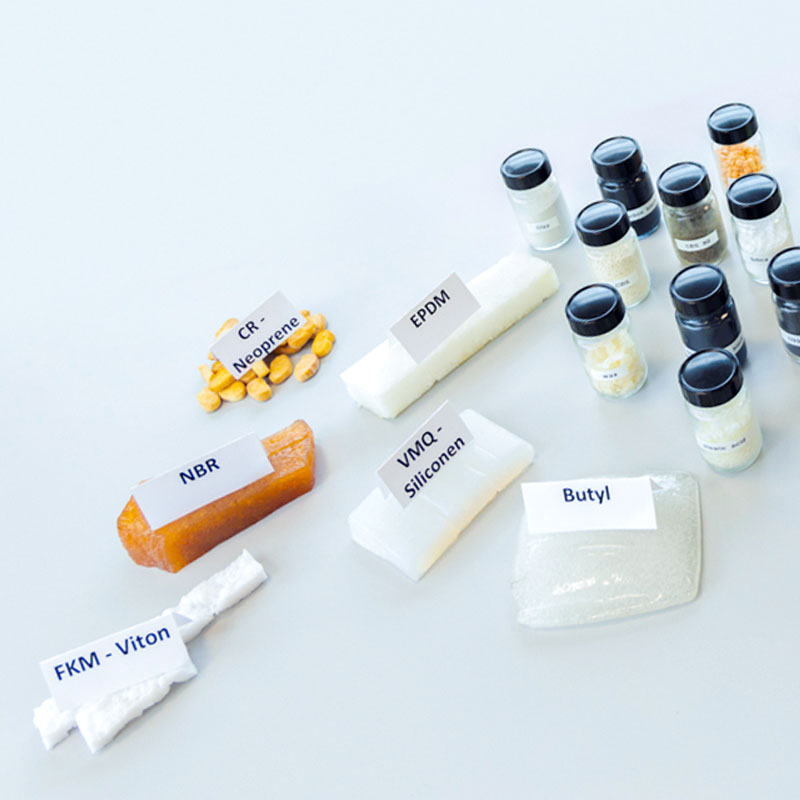
Rubber materials or elastomers used in sealing applications are often described as compounds; meaning that they are a mixture of ingredients manufactured under specific conditions. A compound typically comprises a polymer, cross-link system, fillers and other ingredients used to achieve specific manufacturing-, application- or cost requirements.
The basis of compound design is a selection of the polymer type. To the elastomer, the compounder may add reinforcing agents, such as carbon black, colored pigments, curing or vulcanizing agents, activators, plasticizers, accelerators, antioxidants or antiradiation additives. There may be hundreds of such combinations.
Different circumstances demand various compound properties. That is why so many compounds have already been developed. We have categorised our compounds in standard- (general purpose), specialist-(industry or application specific) and high performance grades.
Hardness of elastomer
One of the most frequently named properties regarding polymer materials is hardness. Hardness is the resistance of a body against penetration of an even harder body of a standard shape at a defined pressure.
There are two procedures for hardness tests regarding test samples and finished parts made out of elastomer materials:
Shore A / D in accordance with ISO 868, ISO 7619-1, ASTM D 2240 Most elastomers are measured on the Shore A scale. Shore A hardness of 35 is soft; 90 is hard. Shore D gauges are recommended where the Shore A rating is greater than 90.
Durometer IRHD (International Rubber Hardness Degree) in accordance with ISO 48 , ASTM 1414 and 1415
The softer the elastomer, the better the seal material conforms to the surfaces to be sealed and lower pressure is required to create a seal. This is particularly important in low pressure seals that are not activated by fluid pressure. The softer the elastomer, the higher the coefficient of friction.
In dynamic applications however, the actual running and breakout friction values of a harder compound with lower coefficients of friction are higher because the load required to squeeze the harder material into the O-ring groove is much greater.
The softer the elastomer the more risk that at high operating pressure the elastomer of the O-ring will extrude into the clearance gap between the mating seal surfaces.
The harder materials offer greater resistance to flow. With an increase in temperature, elastomers first become softer and then eventually harder as the rubber curing process continues with the application of heat.
Rubber Chemical Resistance
This information is only a guideline. Chemical compatibility lists should be consulted, such as the ERIKS Rubber Chemical Resistance Guide
Whenever possible the fluid compatibility of the O-ring compound should be rated "A". For a static seal application a rating "B" is usually acceptable, but it should be tested. Where a "B" rated compound must be used, do not expect to re-use it after disassembly. It may have swollen enough that it cannot be reassembled. When a compound rated "C" is to be tried, be sure it is first tested under the full range of operating conditions.
It is also particularly important to test seal compounds under service conditions when a strong acid is to be sealed at elevated temperatures because the rate of degradation of rubber at elevated temperatures is many times greater than the rate of degradation at room temperature.
Types of elastomers
- NBR - Acrylonitrile butadiene, Nitrile or Buna N
- HNBR - Hydrogenated nitrile, or highly saturated nitrile
- XNBR - Carboxylated nitrile
- NBR/PVC - Nitrile/PVC resin blends
- EPM, EPDM - Ethylene Propylene, and Ethylene Propylene Diene rubber
- CR - Neoprene rubber Polychloroprene
- VMQ - Silicone rubber
- FVMQ - Fluorosilicone
- AU, EU - Polyurethane rubber
- FKM - Fluorocarbon rubber
- FFKM - Perfluorocarbons
- Teflon®-FEP/PFA
- TFE/P (Aflas®) (FEPM)
Selecting the right seal material
Important to consider when selecting the right seal material:
- The primary fluids which the O-ring or Quad-Ring®/X-Ring will seal
- other fluids to which the seal will be exposed, such as cleaning fluids or lubricants
- The suitability of the material for the application’s temperature extremes - hot and cold
- The presence of abrasive external contaminants
- Lubricating the seal and mating components with an appropriate lubricant before assembling the unit
Selecting the right rubber material
Rubber is a commonly used material for O-rings. The material's flexibility allows it to take many different shapes. And its diverse properties make it suitable for use in all kinds of applications. Proper selection of the rubber material is essential to prevent leakage or other possible damage. There are four factors that are very important in this: medium, pressure, temperature and time.
- Medium - Every rubber material reacts differently to the fluids it comes into contact with. Therefore, when selecting the right rubber, you need to consider all the media the material comes into contact with, including, for example, cleaning agents.
- Temperature - Some production environments involve (extremely) low or high temperatures. Can the rubber material of the O-ring withstand this?
- Pressure - It is important to know exactly how the pressure builds up within the application in which the O-ring will be used. This is because not every rubber material can withstand (prolonged) high pressure. The hardness of the selected material plays an important role in this.
- Time - How long the O-ring should seal is also important. For the selection of the right rubber material, it is a big difference whether the seal should only function for half an hour a day or perform continuously.

O-ring mounting/installing
Proper assembly prevents O-ring damage. Therefore, always pay attention to the following aspects during assembly:
- Lubrication (oil or grease)
- Rack and twine
- Good assembly kit
- Lubrication (oil or grease)
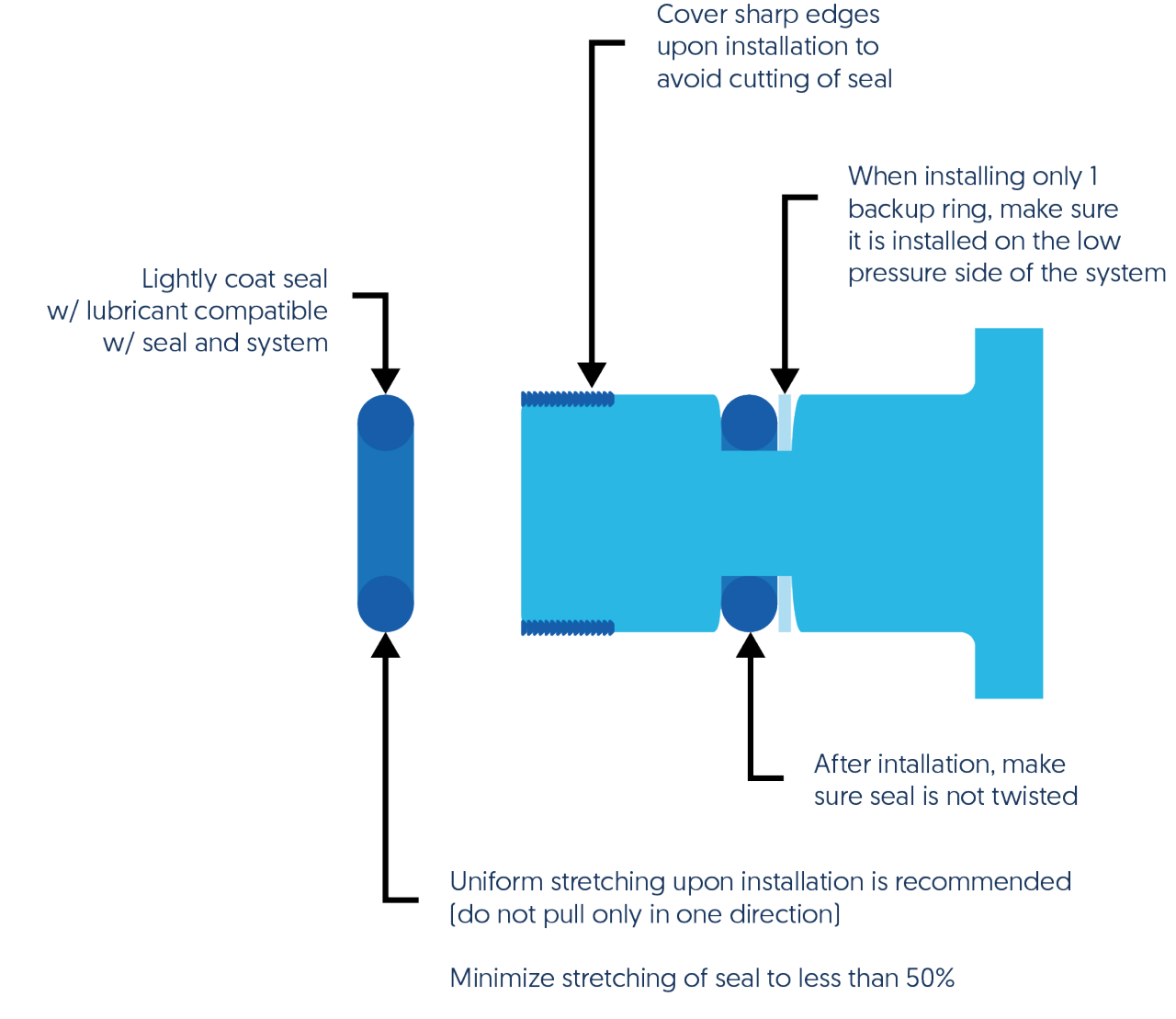
Using (assembly) grease makes fitting an O-ring easier in many cases. It reduces the friction between the O-ring and the parts it sits between. This makes it easier to fit the O-ring into the groove.
Lubrication also extends the life of the O-ring, as it forms a protective layer. A thin layer of mineral oil, grease, silicone oil or application fluid is often sufficient. Make sure that the type of rubber used is resistant to the grease used. For example, a VMQ (silicone) rubber is not compatible with silicone grease. Since both the rubber and the grease have the same structure, the oil can be absorbed by the O-ring and cause swelling and damage.
In any case, never glue an O-ring into the groove. An O-ring should move and set freely in the groove.
Stretching and stuffing
An O-ring is sometimes smaller or larger than the groove in which it is placed. Since rubber is an elastic material, this is not necessarily a problem. It may even be a deliberate choice because of the groove or availability of the O-ring. Quiet stretching or compression of the inner diameter (ID) can solve this and is also allowed. However, the stretch of the ID should never exceed 5%. Stretching should not exceed 3%. For both margins, this is the fitted condition.
During assembly, an O-ring may be stretched. The recommendation is to stretch the O-ring in a gentle manner to a maximum of 50%. Subsequently, do give the O-ring time to return to its original shape before putting the application into service. This depends on several factors, including the material, application and environmental influences (such as temperature). Furthermore, some materials are more elastic than others, an example of an elastic material is VMQ.
Right assembly kit
The wrong tool will cause assembly damage. Avoid sharp parts that can damage the O-ring. Use an O-ring mounting kit when installing or removing O-rings. This allows you to install and remove O-rings more easily, without causing damage. Also be careful not to stretch or twist the O-ring too much during installation.

Storage, shelf life and damage
Storage life of O-rings
Storage life is the maximum period of time, starting from the time of manufacture, that an elastomeric seal element, appropriately packaged, may be stored under specific conditions. After this period of time the O-ring is regarded as unserviceable for the purpose for which it was originally manufactured. The time of manufacture is the cure date for thermoset elastomers or the time of conversion into a finished product for the thermoplastic elastomers. Shelf life of elastomers when stored properly is especially determined by the specific compound.
- NBR, SBR or BR for example have a storage life of up to 5 years.
- CSM, EPDM or EPM can be stored up to 10 years.
- FMK, ACM or FVQM have a storage life of up to 20 years.
The storage life of different elastomers differs according to ISO 2230, indicating an initial and an extension storage period for unassembled components.
Factors that can influence the storage life of O-rings:
- Temperature: Storage temperature should be below 38°C (except when higher temperatures are caused by temporary climate changes), O-ring should be stored away from direct sources of heat (such as boilers, radiators, and direct sunlight).
- Humidity: If the elastomers are not stored in sealed moisture proof bags, the relative humidity should be less than 75 % (65 % with polyurethanes).
- Light: Especially direct sunlight or artificial light with ultraviolet content should be avoided; it is advisable that storage room windows should be covered with a red or orange coating if there are elastomers present.
- Radiation: Protection from all sources of ionizing radiation that might cause damage.
- Ozone: Ozone is damaging to some elastomeric seals, equipment such as mercury vapor lamps, high voltage electrical equipment, silent electrical discharges combustion gases or organic vapor should be avoided.
- Deformation: Seals should be stored away from superimposed tensile and compressive stresses or other causes of deformation. O-rings of large inside diameter shall be formed into at least three superimposed loops so as to avoid creasing or twisting. Note: It is not possible to achieve this condition by forming just two loops, three are required.
- Contact with liquid and semi-solid materials: For example, contact with gasoline, greases, acids, disinfectants, and cleaning fluids - these should be avoided - unless they are an integral part of the component or the manufacturer’s packaging.
- Contact with metals: Certain metals and their alloys (especially copper, manganese, and iron) are known to have deleterious effects on elastomers. Protection by individual packaging is recommended.
- Contact with dusting powder: Dusting powders shall only be used for the packaging of elastomeric items in order to prevent blocking or sticking. In such instances, the minimum quantity of powder to prevent adhesion shall be used.
- Contact between different elastomers: Should also be avoided.
- Elastomeric seals bonded to metal parts: The metal part of bonded elastomeric seals shall not come in contact with the elastomeric element of another seal. The bonded seal shall be individually packaged. Any preservative used on the metal shall be such that it will not affect the elastomeric element or the bond to such an extent that the seal will not comply with the product specification.
- Stock rotation: Elastomeric seal stock should be rotated on the FIFO (First In, First Out) principle.
Proper storage parameters
Proper storage prevents damage to your O-ring. ERIKS recommends the following storage parameters:
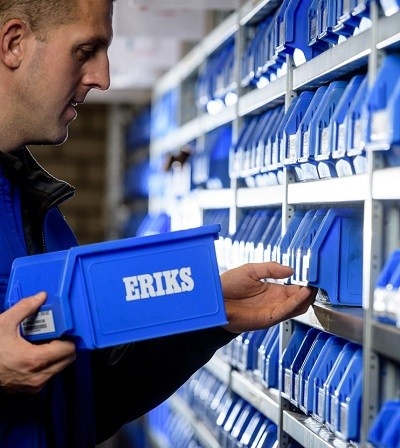
- Ambient temperature (preferably not higher than 25°C)
- Dry environment and exclusion of contamination
- Protection against direct sunlight
- Protection against ozone and (UV) radiation
- Protection against artificial light
- Store part without tension (never hang O-rings!)
- Good packaging (keep the O-rings in the original packaging)
O-ring maintenance
Besides proper storage, it is also important to regularly check the function of fitted O-rings. And that they are cleaned intensively to maintain optimum function. Periodic maintenance of your machines should therefore include O-rings. If this does not happen, chances are that the O-rings within your application will have a shorter lifespan.
If you do clean your machines regularly, you need to be sure that the cleaning process is suitable for your O-rings. This is because not every rubber seal can withstand the chemicals found in cleaning agents. Machines and appliances are also often cleaned with steam cleaners. In those cases, too, you need to be sure that the steam does not damage the O-rings.
O-ring damage
Selecting the right size O-ring, using an O-ring that suits the application and professional assembly usually prevents damage. Nevertheless, it can happen that the O-ring gets damaged. It is then important to know what causes it so that you can fix it in a targeted way.
- Installation damage due to mounting error - Use an O-ring mounting kit for proper mounting.
- Permanent deformation due to excessive load - Select material with better compression rate or higher temperature resistance.
- Hardening and cracking due to overheating - Select compound that can withstand (extremely) high temperatures.
- Hairline cracks due to light/sun influence - Select material that can withstand ageing or ozone well.
- Distortion due to extrusion - Redetermine the groove dimension to avoid too much play.
- Twisting by moving along in the groove - Use proper grease as lubricant.
- Explosion after Decompression (EAD) - Application of special EAD compounds.
Standards and norms
O-rings are manufactured in accordance with a variety of standards for different countries. Standards say something about the size of the O-ring: internal diameter by cord thickness. For most O-rings from ERIKS, the standard AS568 applies. AS stands for 'Aerospace Standard'.
The ISO 3601-1 standard defines the quality requirements, such as tolerance of the material of an O-ring. Production and control of dimensions and imperfections also follow the ISO 3601-1 standard.

O-ring alternatives
The O-ring is by far the most commonly used seal. Yet there are applications for which alternative seals are better suited, for example the X-ring:
Preventing early leakage in a dynamic, sliding (piston/rod sealing) application - An O-ring may twist in a sliding application, creating a possible leakage path. This twisting will not happen with an X-ring due to its stability.
Longer life in a dynamic application - An X-ring requires less contact pressure, has more contact surfaces and can be better supplied with grease than an O-ring.
Lower deformation force - The X-ring is good to use in applications where the materials or housing are not as strong, for example thin-walled plastic cylinders or housings. The housing must be strong enough to deform the seal and not the other way around.
Subscribe to our newsletter:
For the latest industry news and updates.