Selected products
Safe components for your production processes
Your applications are often critical. ERIKS has worked closely with the industry to develop many specialties and high-performance products. The many environments and equipment for your plant operations require products that are resistant to chemicals, high pressures and high temperatures.
Go to our extensive chemical product range
To see our complete range of all value adding products, please click here.
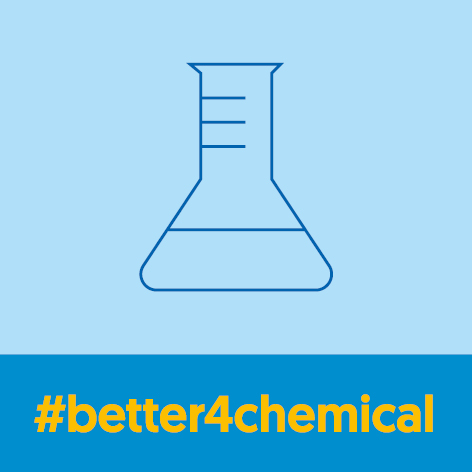
Do you know how to avoid gasket surprises?
As a leading supplier, we develop and manufacture specialized and high-quality rubber compounds and gaskets. To completely cover all applications in a chemical plant, we offer supplementary a mix of premium brands like Garlock Sealing Technologies, SGL Carbon or W.L. Gore & Ass.
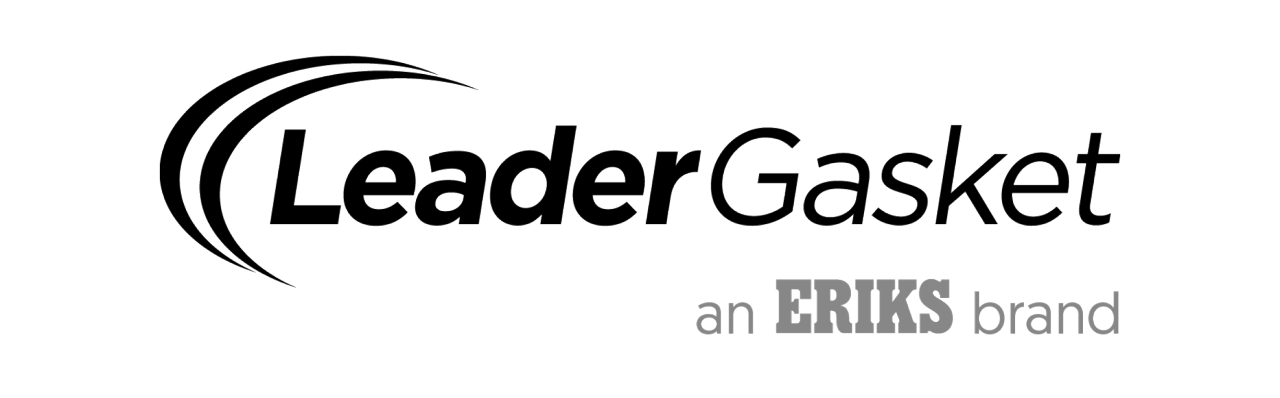
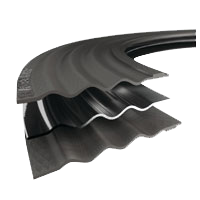

ElastaGraph™
These gaskets simplify your everyday life for standard chemical processes: less effort is required to remove the gasket as there is hardly any contamination due to released graphite. The combination of shape and coating with the different graphite densities enables to provide an up to 50% better sealing effect. The corrugated shape also provides a constant "spring-back" against the flange surfaces and thus reduces the required surface pressure.
Advantages:
- Safer in use compared to other graphite gaskets (higher safe zone at low bolt force)
- Less contamination
- Easier disassembly
- High adaptability to flanges
- Reliable sealing up to a pressure of 64 bar
- Retain uniform prestressing
- Clear marking
- Lower emission value
Clipperlon
We offer you the latest-generation PTFE sealing materials. Our PTFE gaskets have outstanding chemical stability, which makes them ideally suited for use in the chemical industry.
Advantages:
- Excellent seal ability
- Outstanding chemical resistance
- Suitable for high pressure and large temperature range
- Significant reduced creep (non-cold flow)
- Low leak rate
- Good electrical insulation properties
- Non ageing
- Batch code and complete traceability
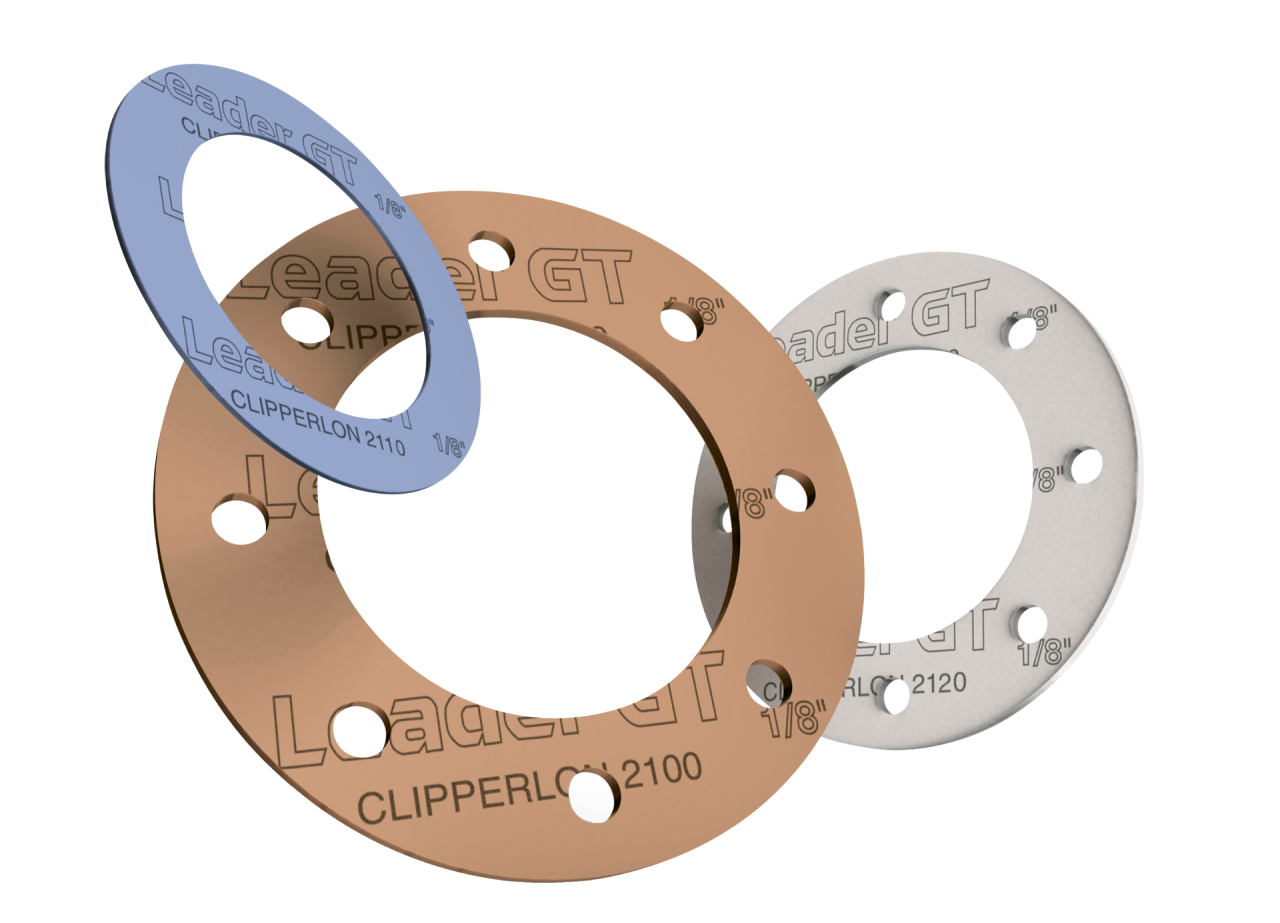
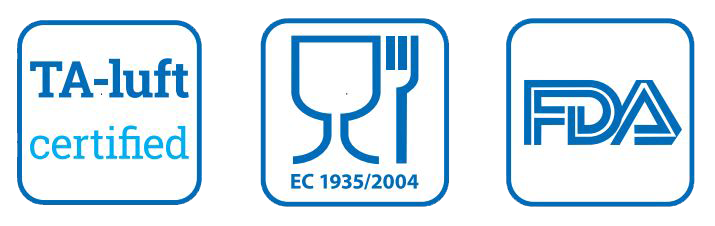
Hoses: Process safety as top priority
One of the major challenges in the chemical industry is to ensure a consistently high level of process workflows for your critical applications. We support you with this by taking on responsibility for the assembly in our own assembly units, testing and certification of your entire hose system.
Testing procedures with extreme conditions for rubber steam hoses, formed the parameters for the ultimate steam hoses. Even a special EPDM compound still has a porous structure, causing tiny water and steam particles to accumulate in the wall resulting in the 'popcorning' effect. To overcome this 'popcorning'-effect, Goodall developed a special, non-porous rubber compound for the inner tube of the steam hoses. This tube is extruded and thus extremely smooth and non-porous. The double braid of galvanized steel wires contributes to higher safety and a longer lifespan.
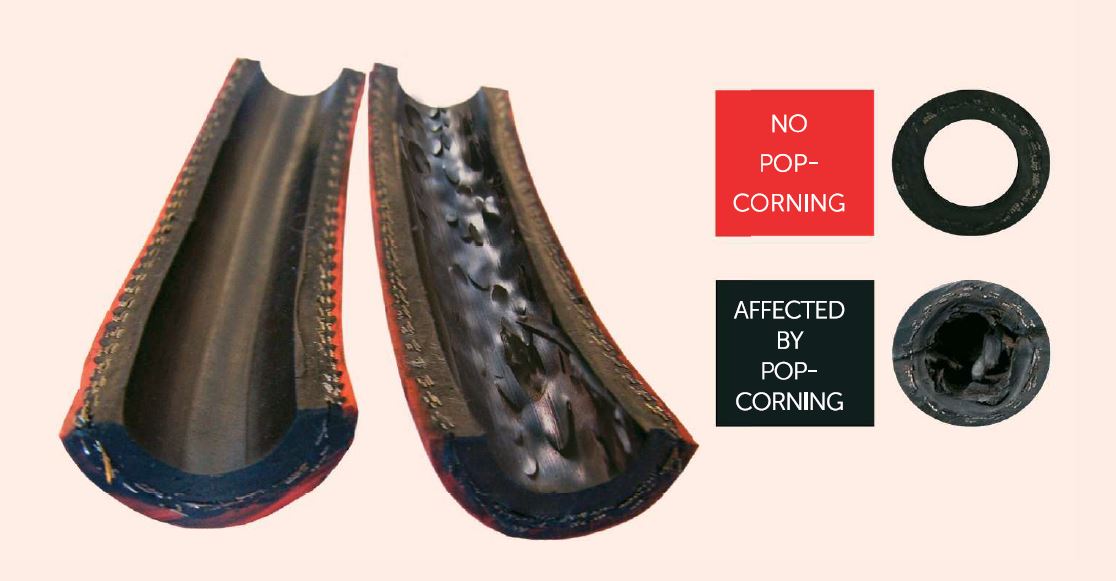
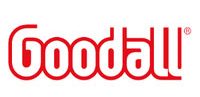
A total solution to keep your plant up and running
An innovative and thoroughly tested crimping system for the new generation of Goodall steam hoses. This exclusive solution offers the following advantages:
- lncreased equipment safety and reliability
- Cost savings
- Original and innovative ergonomics
- ldentifiers with colored identification rings and RFID
- Superior compounds
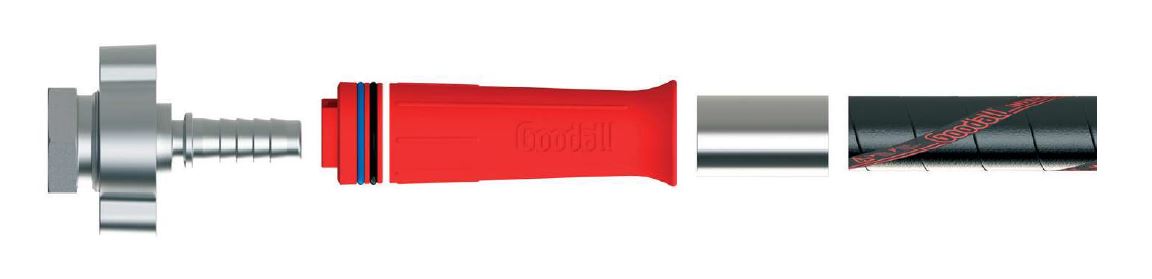
coupling – ferrule – hand grip – hose
Chemical hoses: decreasing safety hazards in ATEX zones
We know the hazards of static electricity in chemical plants. That’s why we have created an innovative line of conductive hose products to minimize risk to you and your employees; thereby decreasing your liability and preventing devastating results. Our innovative conductive compounds assist your grounding the assembly for added security and safety.
METALVISOR® - preventing leaks and guarantees less downtime and maintenance
We have designed the best possible hose and the ideal coupling system. We developed new and efficient assembly techniques and welding procedures to avoid gaps and burrs improve the flow of the hose and avoid corrosion. This complete system will increase safety and improve your productivity and efficiency.
Finding the right hose for your chemical application?
Our chemical resistance guide helps you:
Flow control: systematically conduct your media
ERIKS offers a complete range of valves, actuators and accessories, supplying you with its own brands and products from world-renowned manufacturers. Together with you, we develop also customised solutions.
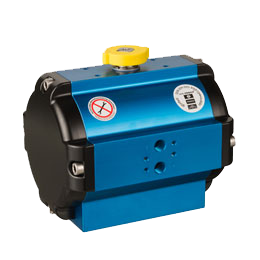
AMG actuators with ECON® ball valves (SIL)
- Specified for applications where fluids are
to be safely and efficiently transmitted - For all fields of flow technology and automation
Why do O-rings fail?
It might be the case that your O-rings fail as the used compound is not adequate for your application. With our chemical resistance guide we help you to find the right material.
ERIKS Sealing Technology is a world leader in high-performance O-rings, elastomeric and polymer seals. We engineer new solutions for your applications, whether your requirement is for individual products, small batches or production volumes. Supported by an outstanding technical and logistical service, we deliver the right seal on time to the critical applications in your chemical plant.
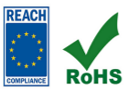
ERIKS O-ring assortments in generic materials:
Teflex encapsulated O-ring range
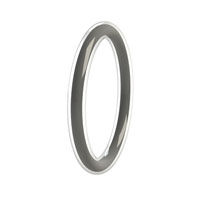
900553 FEP/FKM
- High chemical resistance due to FEP coating
- Temperature range from -20°C to +200°C
- Anti-adhesive properties, no sticking to the surface (stick-slip)
- Deep steam permeability and water absorption
- Good compression set
Vulc O-rings
X-ring assortment
DuPont™ Kalrez® O-rings
These combine high heat and chemical resistance and are an excellent choice for the chemical process industry.
Power transmission: for a smooth operation of your plant
Rexnord couplings
These couplings perform under the most rigorous demands in your chemical applications. With safety in mind we offer you a complete line of flexible couplings for fluid handling systems.
From engineered API compliant Thomas Disc Couplings, to general purpose ANSI Rexnord Omega and Viva Elastomeric Couplings, the portfolio delivers reliable performance for every pump and fluid compressor application.
Gates Poly Chain® Carbon™ Volt®
Antistatic power transmission belts are a must in explosive environments. With this most powerful synchronous belt in the market, you choose the safest and strongest option.
- Static conductive to ISO 9563 throughout the lifetime of the belt
- ATEX directive compliant: suitable for environments with explosive atmospheres
- Clean, quiet, compact, durable and energy cost saving
- Suitable for high torque, low speed drives
Motors: when it comes to hazardous areas, we make it safe
WEG ATEX motors
Non-sparking Ex nA motors are designed to prevent the occurrence during normal operating and certain specific abnormal conditions of arcs, sparks and excessive overheating of all inner and outer surfaces of the machine which could reach the self-ignition temperature of the surrounding potentially explosive atmosphere.
High efficient IE4 motors to reduce energy costs and prolong lifespan
Electric motors account for as much as 68% of industry’s energy usage. Yet a huge amount of this energy is wasted, as chemical plants use solutions which are poorly designed, or inappropriate for their application. By reducing this wastage, you do not only help the environment, but you also cut your cost with a return on investment of three years or even less.
Engineered plastics
In the chemical sector, the materials suitable are determined based on their application. The materials can be exposed to high stresses due to the chemicals used. In most cases, inadequate resistance is manifested by swelling or softening of the plastic, which can lead to loss of usability. The following products represent a selection from our chemical resistant range.
Standard plastics
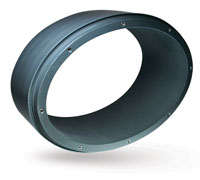
PVC-U
PVC has high chemical resistance to acids, alkalis, alcohol, oil and petrol. It also adheres and welds very well and is used for extraction systems, container linings and in the construction of chemical plants.
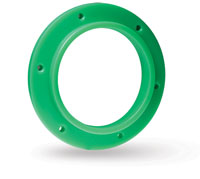
PE (HD, HMW, UHMW)
PE displays average to good chemical resistance to acids and alkalis. This plastic is also very weldable and is used to construct containers.
Fluoroplastics
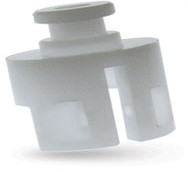
PVDF
PVDF exhibits excellent resistance to chemicals, for example to chlorine and bromine, and can be used in a wide temperature range (from approx. –50 °C to approx. +150 °C). PVDF is used is the construction of chemical plants.
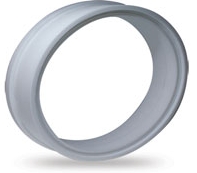
PTFE
PTFE is extremely resistant to acids, alkalis, alcohols, petrol and oil. The interesting thing about this plastic is its strongly anti-adhesive behaviour and very low coefficient of friction. PTFE is used for gasket technology.
Fibreglass-reinforced plastic (FRP) – ideal material for chemical plants
This very interesting alternative to steel convinces through the low tool costs and varied shaping options.
For areas away from production zones, it is the ideal material for a multitude of different constructions. FRP is much lighter than steel – with the same tensile strength and compressive strength. In addition, the material functions as insulation and is resistant to corrosion, alkalis and chemical cleaning agents.
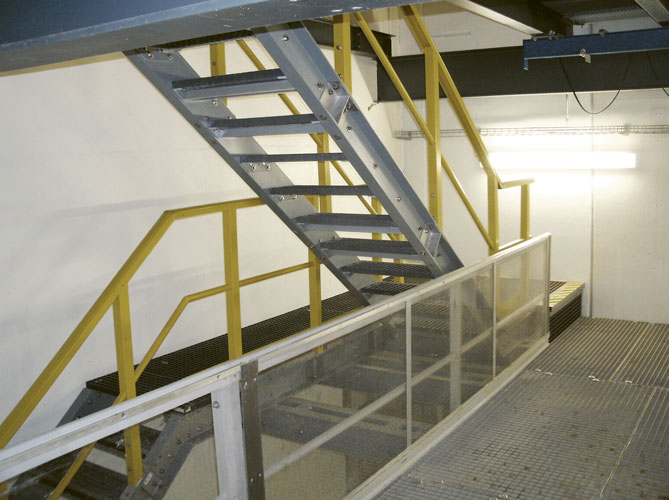
Occupational safety: for optimum safeness and sustainability
With our range of personal protective equipment (PPE), tools and maintenance products, we can provide you with comprehensive advice and offer solutions tailored to your requirements.
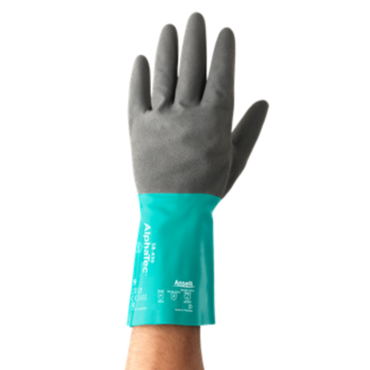
Chemical resistant ANSELL Glove AlphaTec™ 58-430
The glove is ideal for intermittent exposure to lubricants and cleaning agents in chemical plants. This unique design features a premium grade nitrile compound coating, for versatile chemical protection and long-lasting snag, puncture and abrasion resistance, along with a comfortable cotton-flocked liner.
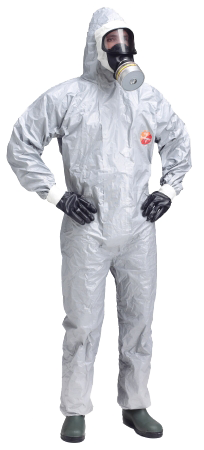
TYCHEM Coverall disposable
TYCHEM F Coverall with hood is an excellent barrier against a broad range of organic chemicals, highly concentrated inorganic chemicals and biological hazards. The protective suite has an antistatic treatment inside.
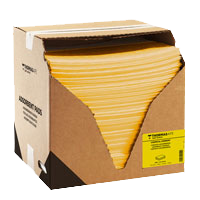
THORMASAFE spill control
These absorbents are a high-quality, high-performance workplace spill control and absorbent solution for incidents, and day-to-day situations involving chemicals and solvents.
Contact
Direct contact
Want to speak directly with one of our employees or specialist? Don’t wait and get in touch
General contact
Get in contact with us. Please fill in our online form and we will contact you as soon as possible.
Request to your team
Found a product, service or solution but you need to first discuss this with your team? We help you to collect and send all the information to your team.
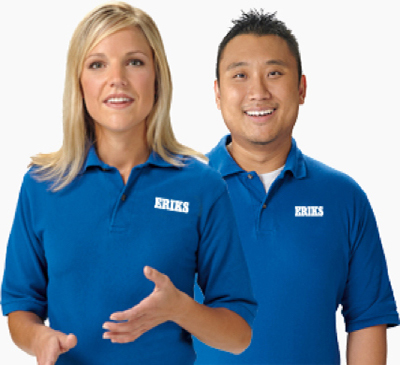