In this article
Smart Gaskets: Driving Digitalisation in the Gasket Industry
When Ben Cloostermans, R&D Engineer at ERIKS, attended the renowned 2022 ASME (American Society of Mechanical Engineers) Conference in Las Vegas (NV, USA) this Summer, little did he know that his paper presentation would gain the attention it did. In fact, his presentation was scheduled towards the end of the conference, and secretly he was a little concerned this may unfavourably impact attendance. Nothing could be further from the truth. Not only did Ben present his research findings to a packed and engaged audience comprised of academia and industry specialists - he was also awarded the 2nd prize for best paper in the PhD category. A well-deserved honour, presented by the president of the ASME, Karen Ohland.
Indeed, Ben’s research garnered much attention, as it offers an innovative approach to solving one of the most fundamental problems in gasket technology – difficult to demonstrate thus far, as the technology required was simply not available. Ben was gracious enough to meet with us to explain the ins and outs of his ground-breaking research.
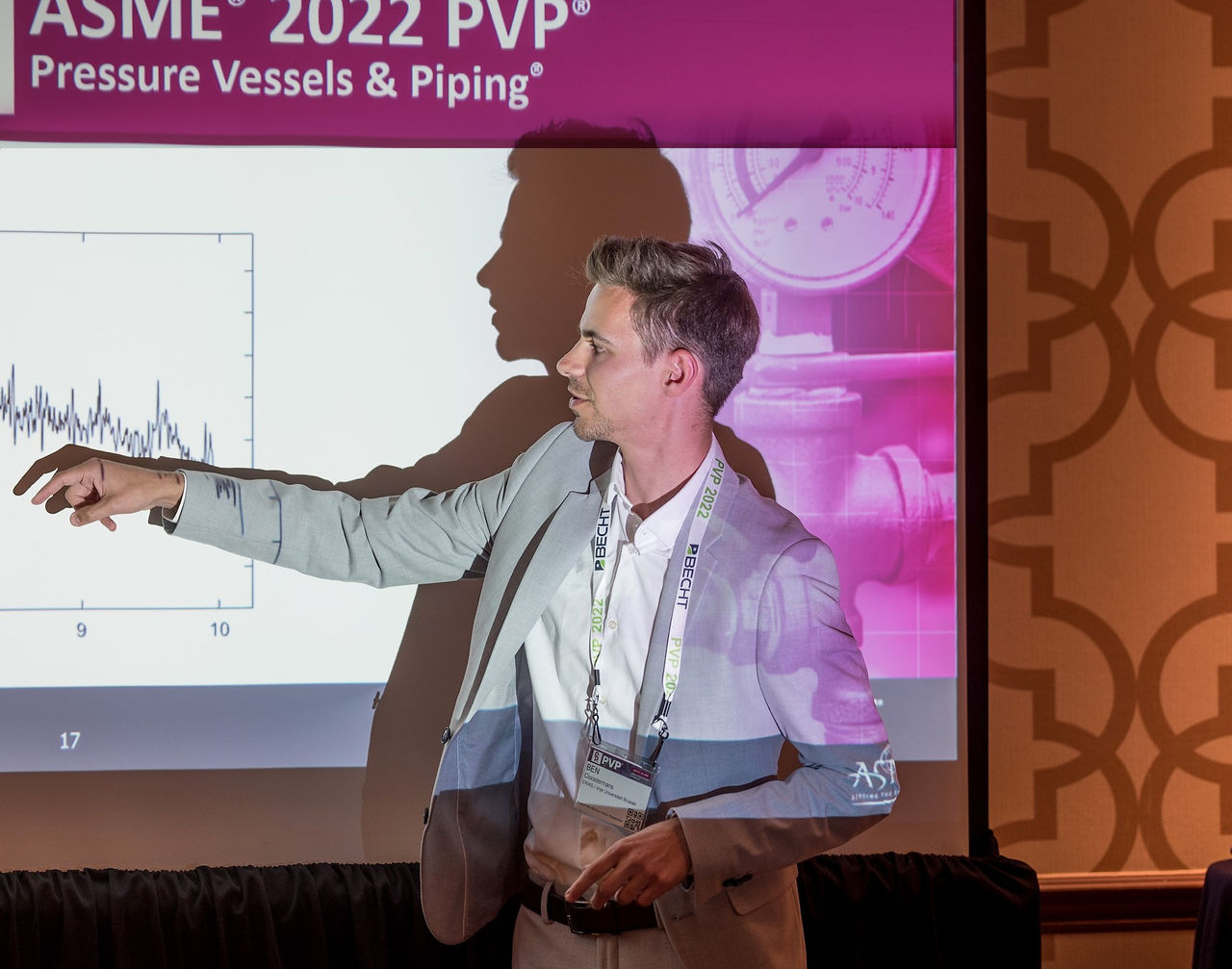
Journal Publication
The first step towards academic and industry recognition for his research came early this year, when Ben published a scientific research article in the peer reviewed journal of Mechanical Systems and Signal Processing (MSSP). This research paper introduced the concept of Smart Gasket technology, in which the gasket performance is directly measured within the gasket. It also defined the framework for his follow up research paper, presented at the ASME conference.
The Smart Gasket research is made possible by the high-level collaboration between ERIKS and B-PHOT, the photonics research institute of Vrije Universiteit Brussel. B-PHOT and ERIKS teamed up under the framework of ACTPHAST, an EU-funded consortium, offering support to European companies who want to boost the innovation of their projects with photonics. A similar programme known as PhotonHub Europe is running now to offer expertise, know-how and technology platforms for businesses and researchers to cooperate on ground-breaking innovations.
To establish this partnership, Ben was awarded a personal research grant for PhD research from VLAIO (Vlaams Agentschap Innoveren en Ondernemen). Indeed, VLAIO’s mandate is to accelerate the adoption of cutting-edge technology within the industry by funding societal relevant research projects.
Gaskets: main challenges
So, what are the main problems Ben’s research is tackling? The challenges with gaskets are twofold, he explains, “First, the gasket must be properly installed to ensure that there is no leakage in the installation during start-up. Then, you must monitor the flange connection to make sure that it remains intact during use.”
Currently, gasket performance is mainly based on calculations that include many assumptions and uncertainties. For standard flanges these are quite accurate, but when the installation becomes more complex – involving heat exchangers or pressure vessels, for example – the flange connection becomes more difficult to evaluate. Slightly different sizes, bolts that are perhaps fixed by design can all cause uncertainties for that gasket.
Optical Fibre Sensors
Accurate evaluation of a gasket’s behaviour is also difficult because a gasket is only a few millimetres thick. Consequently, it is hard to find sensors that will fit within the product. That is why the idea of optical fibre sensors was introduced. These relatively new sensors, as thin as a hair, have been gaining ground over the last 20 years. “Everyone knows about the Internet and optical fibre,” explains Ben “but what few people know is that you can also use them as sensors to measure certain quantities, such as pressure, temperature, electric field and all sorts of variables. And we actually use them to do strain measurements.”
“Through this optical fibre sensor, we are able to measure the status at several points in the gasket to determine the pressure applied to the gasket’s surface. We can observe how much the fibre is stretching and how that gasket will distort. In this way, we can estimate how well the gasket has been installed, so that we can exclude the possibility of a leakage during the entire process.”
It is a very specialized process where knowledge about the sensor itself, how it behaves, is combined with the properties of the gasket. Here the unique combination of University expertise in sensors, and ERIKS specialism in gaskets, is shown to its full advantage.
Experimental process
In terms of experimentation, once the right type of sensor was determined and instrumented, the signals were recorded in the form of raw data. That is mainly where Ben’s expertise comes in: conducting data analysis using sensor and gasket knowledge, to convert the raw data into tangible information. “We analyse the data to see how we can use these signals to say something about the condition of the gasket during installation and service,” Ben explains. “For a researcher, it's all about solving the technical challenges first in vision of the research goal. Can I measure it? And then the next step is to find out – How can I utilize it to create an added-value?”
Technology Readiness
“We are now at the stage where we know that we can measure something within a lab environment” Ben states. In terms of technology readiness levels (TRL), which indicate the maturity of a new technology, this represents TRL level 4 to 5. These levels run from TRL 1, at the fundamental research level, to TRL 9, the full commercial application. “At TRL 9 we basically know what to do with it and it can truly serve to make our lives better,” Ben explains. “At this point, we've observed it; we've tested it in a controlled environment; we're testing it in an operational environment and that's actually where we are right now – the transition from lab environment to real-time field environment.”
So, the challenge currently is to move the research from the lab to the field. To show how the smart gasket concept can truly add value to the customer's application.
Pilot Project
We are going to run a pilot project” says Ben “where we are searching for an early adopter, a customer who is prepared to take on the challenge but is also aware of the possible output.” So, there will be a true synergy between the supplier, on the one hand, and the manufacturer, on the other. “Because we can come up with solutions,” Ben rightly notes,” but ultimately you need to test these on the customer's premises.” The advantage is that at ERIKS we have such a good relationship with our customers, so we have the possibility to do that.”
It is not truly part of ERIKS’ DNA to take a project from the fundamental level to an application level. “Usually, we start somewhere at the halfway point of the TRL levels and lift it to an application” Ben confirms. “But here we really do make the effort towards the community to solve a fundamental problem from the gasket world. With the help of the partnership with B-PHOT, of course.”
Digital Twin
The smart gasket is similar to the concept of the Digital Twin, a digital representation of a physical object. “As we are moving towards an era in which everything is digitised, people no longer want to inspect things manually. We want to offer a solution for the gasket and to digitise it so that we can relieve some of the customer's worries.” The smart gasket itself can give an alert when something is wrong or confirm that it functions properly.
The research is about trying to create such a Digital Twin and propelling the gasket world into the digital age. In terms of benefits, as we have seen, it is about securing the installation, but also, about improving stock management. If you know when a gasket will need to be replaced, you can optimise your stock. Another important benefit concerns liability. The fact that you can prove the gasket has been installed properly, ensures that you conform to government regulations, regarding emissions, for instance. So, when the smart gasket is installed, in the long run, it is also about limiting emissions and reducing the carbon footprint.
Driving Digitalisation
“The essence of what we are trying to do is to drive digitalisation within a rather conservative industry,” Ben concludes. The short-term goal now is to deploy the smart gasket with customers – on pressure and temperature – and prove that it truly brings value to the customer’s application. The long-term aim is to develop the concept and create a business model around it. So that eventually, gaskets will be instrumented with sensors that read out automatically in the customer's dashboard. But of course, this will be TRL 9.
“It's about a product that we have, adding something that makes it smart, so that you end up with data that is fully compliant with the whole industry 4.0 and IoT. And we are trying to achieve this with a partnership at the highest level.” To receive the seal of approval from the reputable ASME was an important milestone in this endeavour. Ben concurs, “If they say that what you are doing is good, that it really is a problem and that you have found a good method to solve it, well, that only motivates you to continue!”
Subscribe to our newsletter:
For the latest industry news and updates.