In this article
Industrial plastics: key selection criteria
Plastics are present in many applications. Indeed, the complexity of the materials composition has greatly evolved, making them useful in all industries. In addition, the durability and reduced weight of plastics have now widely proven their value in reducing CO² emissions. With so many plastics on the market, here we elaborate on the selection criteria for your application.
Start your Search Early
Like many other materials, when you’re searching for the ideal plastic for a machine development project, it’s best to start the process early. Even if you find that certain aspects and requirements will change as your project progresses, it’s far easier to adapt requirements during the design process, than start from scratch once your project is already well on the way. Getting a plastics expert involved early on will also help avoid unnecessary issues and delays. It is the optimal way to ensure you select the right material for the intended purpose.
Select the Right Material
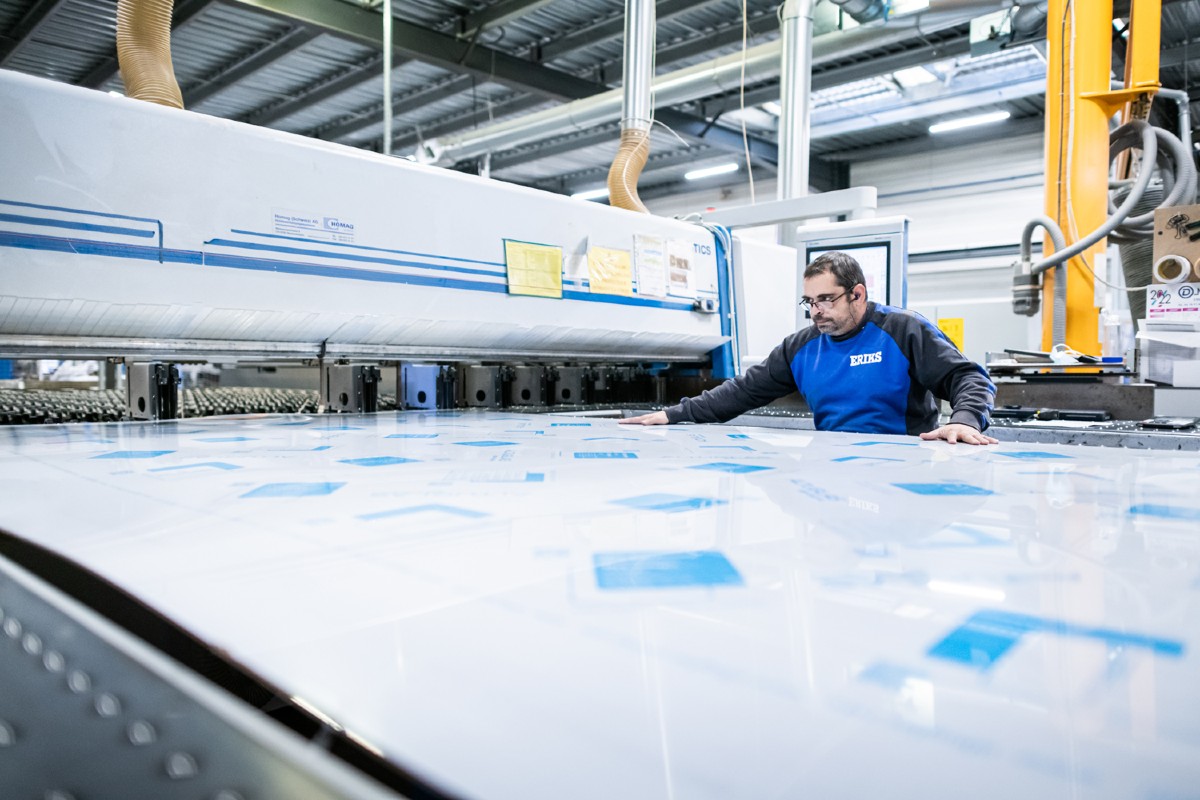
When it comes to choosing the ideal plastic, take time to work out the requirements it must meet and any special properties it must include. For instance, this may involve temperature, pressure, electrical insulation, electrical conductivity, and chemical resistance. Once these properties are identified, a plastics expert will narrow down the selection. In the following sections, we’ll examine some of these common properties and characteristics that are vital to a successful material selection process. When you begin the process of selecting a plastic for your project, there are five key factors to consider: temperature, pressure, insulation, medium and surface quality.
Temperature
Temperature plays a central role in identifying which plastics will be best for certain applications. Once temperature requirements rise above 100ºC, there are fewer options, and for over 300ºC the figure falls dramatically to just 2 plastics PI and PBI. If your machine will be located in a hot environment, this will also need to be taken into consideration.
Pressure
Thermoplastics will deform over time if the pressure around them is too great (so-called cold flow). If your machine stands on a plastic support, weight is decisive as to the type of plastic needed. It may be necessary to reconsider using a thermoplastic and switch to a Duro Plast plastic instead. This plastic (resin) is chemically cross-linked and reinforced, which means it will not deform under pressure.
Pressure also influences the choice of plastic parts to be used inside your machine as some have brittle and hard properties. Ideally, for these components, you would use tough-elastic or impact-resistant plastics, which are not so easy to break.
Insulation
There are two insulation properties. The first is thermal insulation. Quite often the need is not to transmit heat but insulate it – and most plastics are good thermal insulators. But it’s important to remember that to achieve very low insulation values, it’s better to select a foamed plastic containing air as these are good insulators. However, if low insulation values are not important, solid plastic will suffice.
The second insulation property is electrical insulation. There are many plastic options for this category, but it’s a good idea to inform your supplier if the plastic needs to be an electrical insulator (ESD) or conductive (ELS). For instance, in the electrical and electronics industries, the plastic must not become statically charged if it’s an electrical insulator and the current must always be dissipated – and this can be controlled with an antistatic plastic. Alternatively, if you need an electrically conductive plastic, you can achieve this through antistatic additives and conductive additives.
Medium
Apart from mechanical engineering, the type of plastic selected can also be influenced by the medium to be used in the machine. In the chemical industry for example, you need to ensure the plastic has the right level of resistance. To increase the chemical resistance, additives (so-called reinforcing fillers) can be used or it can be polymerised with another plastic during production (so-called co-polymer).
In mechanical engineering, for machines such as grinding machines, cooling oils are used to minimise heat during the milling process. These are usually oil/water emulsions, which are also a chemical preparations that can affect the plastic, so you need to be sure the cooling oil will be tolerated. The same is true for lubricating oils and grease. That’s why it’s important to consider the effect of any media involved when the machine is in operation because the plastic might deteriorate.
Surface Quality
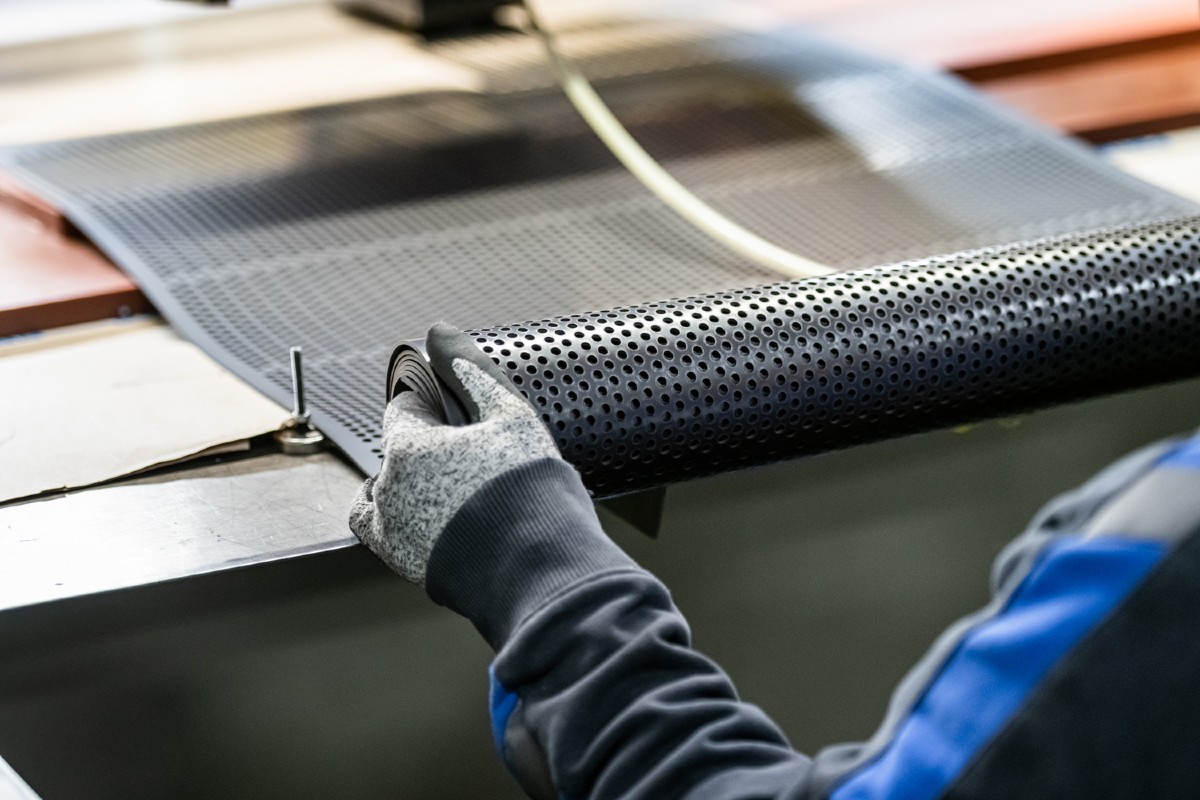
Surface quality is also an important consideration during your material selection process. For example, if you’re developing a punching machine, grinding machine or CNC milling machine, you need to install a window so operators can keep an eye on what’s going on. The window can be easily damaged by materials such as oil or debris. To ensure the window remains transparent, it’s possible to obtain a transparent plastic with a hard, so-called nano coating, which ensures the surface of the window is protected against scratches.
Food and Pharmaceutical Safety Compliance
In the machine construction industry, plastics are also used that require both EU/FDA food and pharmaceutical (USP23 Class VI, NSF 61) conformity. Many manufacturers in the machine industry also produce machines or individual components that come into contact with both food and pharmaceutical substances (e.g. in tableting). These materials must fulfil the conformity for contact with such substances, as well as the traceability back to the polymer manufacturer. For instance, as early as possible it must be known that these plastic parts must not be processed with cool oil CNC.
The cool oil can penetrate the pores of the plastic and as a result, the plastic is no longer suitable for contact with food. As customer, you must therefore be informed at an early stage that the plastic is only to be processed dry – without coolant – to guarantee food or pharmaceutical compliance. Here, too, you can see that a prior discussion with the supplier makes sense so that the plastic can be processed correctly for the intended application.
Increase Possibilities with Additives
Today, there are almost no pure plastics being used. Just about all plastics made contain additives to improve their properties and these present huge potential to expand a plastic’s application opportunities. In fact, additives determine what a plastic is used for and they can be added to influence not only insulation, but temperature and other properties such as electrical/thermal insulation, chemical resistance, pressure, mechanical strength and sliding properties/abrasion. This means that there are frequently additives available that can transform the plastic’s characteristics to meet your machine development needs.
Most of these additives are chemical compounds and substances added to plastic ensure:
- UV resistance
- Chemical resistance
- Thermal insulation
- Electrical conductivity
- Anti-static
- Increased hardness
- Transparency
- Neutron radiation absorption
Meet Industrial Standards and Regulations
An expert supplier will ensure their plastics comply with all relevant standards and produce a plastic to meet the needs of special applications. A wide variety of industry standards exist, which set specific product and performance requirements per industry and country.
Key Standards for the plastics industry, as detailed by the British Plastics Federation (BPF), include standards regarding additives, composites, physical properties, and more. Standards-setting bodies and organizations that impact the plastics industry include the Plastics Industry Association (PLASTICS), the VDMA Plastics and Rubber Industry interest group and the international Standards by EN/ISO/TC 61 for Plastics (ASTM).
Sustainability and Plastics
Sustainability and plastics might seem a contradiction in terms, but the fact is that most plastics found today are recyclable, even when they contain additives. This is because additives don’t usually influence plastic recyclability. Even if they are fibre-reinforced, recycling is still possible in principle, although the effect on the recyclate is significant.
The greatest challenge with recycling plastics is ensuring they’re sorted correctly. If, for example, a fibre-reinforced plastic is mixed with a non-reinforced plastic, it affects recycling as the plastic’s properties cannot be classified and its mechanical qualities will no longer be available.
The effort it takes to sort plastics is considerable and therefore not (yet) financially lucrative for companies. This situation is set to change over the coming few years as fines, regulations and financial incentives are implemented to increase the uptake of sorting and incentives to make recycling more profitable for the industry are part of the Plastics Strategy of the European Union.
Involve an Expert Supplier
During the material selection process for machine development, your plastics supplier will be fully aware of the latest additives and changes. They will be inquisitive about the properties required and the application your machine is being developed to handle. This will mitigate the risk of having to adapt to unforeseen issues and avoid any costly mistakes.
To ensure you choose the best solution, always involve the expert supplier as early as possible. The field of plastics is extremely intricate and many are unaware of the sheer number of types that are available – nor the opportunities and potential they present. A proven supplier will quickly ascertain your needs and recommend either the exact solution or a range of suitable materials to choose from.
Subscribe to our newsletter:
For the latest industry news and updates.