O-ring degradation: characteristics, causes and solutions
Prevent the degradation of your O-ring, identify the possible causes.
The degradation of an O-ring can have many causes and unpleasant consequences. It can crack, loosen or leak. Of course, you would prefer to avoid all damage, but this is not always possible. You need to recognise, repair and prevent the different types of damage that an O-ring can suffer.
In this article
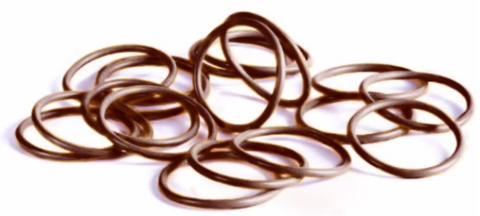
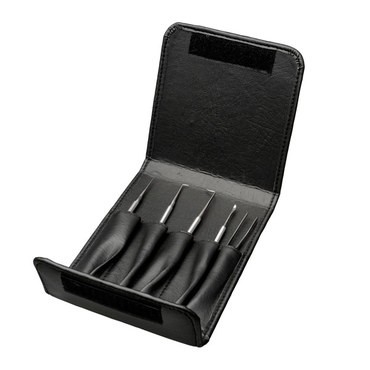
Avoid damage to your O-ring
If used incorrectly, an O-ring can deform, harden, crack and eventually leak, with all the consequences that this entails. The most common mistakes made when choosing an O-ring are the following:
- Incorrect O-ring size
- Installation or assembly error
- Selection of an O-ring not suitable for the intended application
With proper preparation, you can avoid damage to your O-ring:
1. Correct size: Use the O-ring calculator to calculate the size of the O-ring groove. If you select the correct size O-ring, you can be sure that it will fit the groove precisely and provide a good seal. This prevents leakage of the medium the O-ring is in contact with (such as liquids and gases).
2. Assembly and installation: You can avoid assembly or installation errors by using the appropriate tools. Install and remove an O-ring safely with an O-ring assembly kit. This assembly kit contains various tools with which you can assemble and disassemble the O-ring without excessive stretching or compression.
3. The application: The O-ring you need depends on the application. In short, you need to understand which production process or purpose are you using the O-ring for as this determines the material or compound (a very specific mixture of ingredients) of the O-ring. To find out more about chemical resistance by compound, see our chemical resistance guide. You can also use the O-ring selector to choose the correct O-ring.
Identify and repair a damaged O-ring
Whether it's micro-cracks, twists or permanent deformations, your O-ring can be damaged in many ways. Here's how to identify and repair the different types of O-ring damage:
Installation damage due to assembly error
The O-ring may have been damaged during installation. For example, the O-ring may come into contact with a sharp part and be partially cut.
Cause and effect
Incorrect installation or the use of an inappropriate tool is usually the cause of installation damage. This is often due to difficulty in accessing the location of the O-ring installation, or because the O-ring is very small.
An assembly error can result in the O-ring not fitting properly into the groove, or in the O-ring being stretched or compressed. The O-ring is then no longer tight, which leads to leakage.
Solving a problem related to an assembly error
Using a suitable tool ensures correct installation of the O-ring, without stretching, pressing or forcing the O-ring unnecessarily. Therefore, use an O-ring assembly kit. In this kit you will find various tools that allow you to install the O-ring correctly.
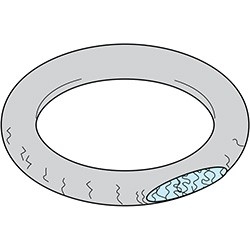
Residual deformation due to excessive load
Remanent deformation of an O-ring is normal. The O-ring partially regains its shape when the load is removed. Is this not the case? The load on the O-ring is too high. The compression set is too high.
Cause and effect
The deformation may be permanent due to incorrect compression settings – the degree of compression set. An incorrect groove size can also affect the compression set of an O-ring. If compression set occurs, the O-ring will no longer seal properly and leakage may occur.
Solving a problem related to permanent deformation
There are significant differences in compression set depending on the type of O-ring. To solve this problem, choose a material with better compression set or higher temperature resistance. Ideally, compression set should be between 15% and 25%. This also depends on the application.
In some applications it is essential to use an O-ring with low compression set, for example in a boiler. In this case the temperatures fluctuate causing the O-ring to compress and decompress. A low compression set is therefore necessary in this case, as it offers a more durable elasticity.
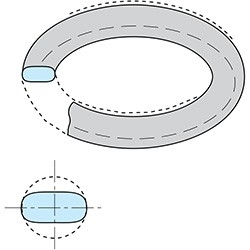
Hardening and cracking due to overheating
An O-ring can harden if the application temperature is too high. Hardening causes cracks in the O-ring. These cracks can go in any direction. Does your O-ring have micro cracks perpendicular to the direction of the stress? If so, this is the result of exposure to light or ozone. For more information, see the next section.
Cause and effect
Hardening of the O-ring is due to overheating. This means that the O-ring material (or compound) is not suitable for the temperature of the application. Hardening makes the O-ring material more brittle or fragile, which leads to cracking.
Solving a problem related to hardening and cracking
By choosing the right compound, you avoid future overheating. Some special types of compound can be used up to 327°C. O-rings that can withstand high temperatures are silicone seals or FFKM seals.
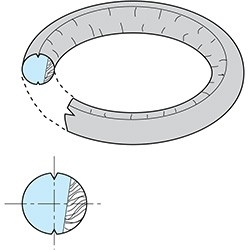
Microcracks due to light/ozone exposure
An O-ring can also develop micro-cracks rather than a large crack. If you stretch the O-ring, the micro-cracks will be clearly visible. Micro cracks are a sign of accelerated ageing. They always occur perpendicular to the direction of stress.
This is in contrast to the cracks that occur in the event of overheating, which run in all directions.
Cause and effect
Not all types of O-rings are resistant to UV light or sunlight. Micro-cracks occur when an O-ring is exposed to direct sunlight or ozone and the material is not suitable for this. Cracks in an O-ring can ultimately lead to leaks.
Solving a problem related to microcracks
Choose a material (component) that can withstand ageing or ozone such as HNBR, EPDM and Viton seals. Make sure the compound is resistant to the media the O-ring comes into contact with, such as certain gases or liquids.
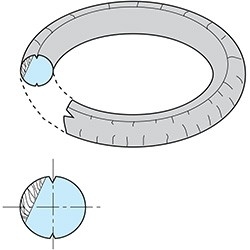
Extrusion distortion
Extrusion occurs when the O-ring is compressed into a gap (clearance) that is too large between the moving parts. The O-ring compressed in the gap is deformed by the moving parts of the application. The O-ring is effectively torn to shreds in this circumstance.
Cause and effect
Extrusion can occur if the maximum clearance is exceeded and the application pressure is too high. The O-ring material cannot withstand this and is therefore not hard enough. As a result of extrusion, the O-ring is no longer installed correctly in the groove, which can lead to leaks.
Solving an extrusion-related problem
Recalculate the size of the groove to avoid excessive play in the O-ring. Alternatively, choose an O-ring material with a higher hardness. The O-ring selector helps you to make the right choice. You can also use a rigid support ring. Place this extra ring between the O-ring and the groove side to prevent extrusion.
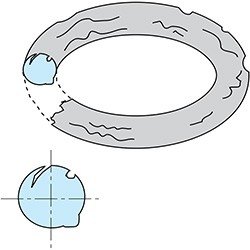
Torsion by displacement in the groove
In a dynamic application with moving parts between the seal, the O-ring can sometimes move in the groove. The O-ring may twist (rotate), which thins the seal material.
Cause and effect
Damage to an O-ring due to torsion can be caused by lack of lubrication, excessive load on the O-ring, or its use in an inappropriate groove. In case of torsion, the O-ring will come loose from the groove and move. This can lead to cracks and possibly leaks.
Solving a problem related to torsion
It may be useful to lubricate the O-ring. With a suitable lubricant, the O-ring will not move or will move less quickly when used with rotating parts. Use silubrinegrease or silicone oil as a lubricant. You can also use an X-seal. X-seals require less compression and therefore experience less friction. For dynamic application, the sealing and stability of an X-seal is better than that of an O-ring.
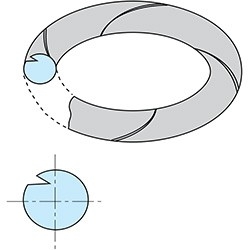
Explosion after decompression (EAD)
Is the pressure dropping too quickly in your application? This means that the gas cannot escape normally from the O-ring material. The sudden expansion of the gas then generates an EAD, also called rapid gas decompression (RGD).
Cause and effect
An explosion after decompression (EAD) can occur when gases under high pressure penetrate the O-ring rubber. This is most common in oil and gas industry applications. When the pressure on the O-ring is normal there is no problem. The gas in the rubber escapes when the pressure drops.
Solving an EAD problem
There are special EAD compounds that can prevent this type of damage. Some of these compounds have been tested according to the NORSOK M710 standard, developed by the Norwegian oil industry. This standard defines the requirements for seals in the oil and gas industry and applies to FFKM 0090 and HNBR 886516.
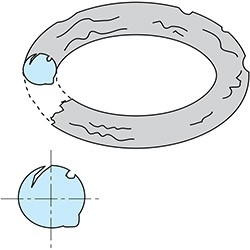
Find out how Demcon and ERIKS joined forces
Sometimes speed is essential to respond adequately to market developments. As a machine manufacturer, you want to be able to adapt quickly. Demcon called on ERIKS at the beginning of the health crisis to modify its ventilator used in intensive care units and to scale up production extremely quickly.

Related articles
Kontakt
Direktkontakt
Sie möchten mit einem unserer Mitarbeiter oder Experten persönlich sprechen? Zögern Sie nicht, kontaktieren Sie uns
Allgemeiner Kontakt
Nehmen Sie Kontakt mit uns auf. Bitte füllen Sie unser Online-Formular aus, wir werden Ihnen schnellstmöglich antworten.
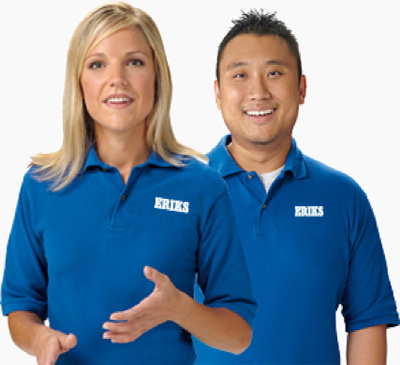