Machine design: making the right choices
Design for Six Sigma and good stakeholder management for a better design process
As an engineer, you are responsible for the design of the machine. It is up to you to ensure that the machine performs optimally and is ready for use on time. A wonderful job, but not without challenges. During the development process, you will be called upon by various factors and stakeholders.
Whether we are talking about inefficient design processes, conflicting interests between departments, or thinking about the seals in a machine too late. You do everything in your power to prevent issues that cause delays, higher costs or other 'hassles'. Design for Six Sigma is a proven method to optimise your (production) processes. Statistics, risk analysis, appropriate documentation and measurable results are central to this process and ensure that you make choices based on factual information.
DMAIC versus DIDOV: existing or new product?
Within Design for Six Sigma there are two different methods. One can be applied to the development of new products (proactive), the other is often better suited to the improvement of an existing product (reactive). Both methods are suitable for the development of machines and parts, such as seals.
DMAIC - Define, Measure, Analyse, Improve, Control
DMAIC is characterised by a mostly reactive approach. This can be very useful. For example, when an existing product needs to be optimised or when you are dealing with relatively standard designs. DMAIC is also often chosen when it is appropriate within a new machine design to change the design (of a specific part) instead of realising the machine design 'from scratch'.
DIDOV - Define, Identify, Design, Optimise, Verify
The DIDOV method is used when developing new products within a machine design, or for more complex challenges where you go beyond the current standard. In these cases, DIDOV serves as a guideline for the design process.
The 5 steps within DIDOV are:
- Define: determining the direction in the run up to a concept. What is expected from a machine (component)?
- Identify: the step towards a conclusive concept. What are 'critical to quality' requirements, how do you identify and reduce failure modes?
- Design: determining the essential product components – materials, moulds, tools, production methods etc.
- Optimise: ensuring consistent and high quality; further reducing risks using proven test methods.
- Verify: the zero series is in sight, verify if the product (part) will function properly.
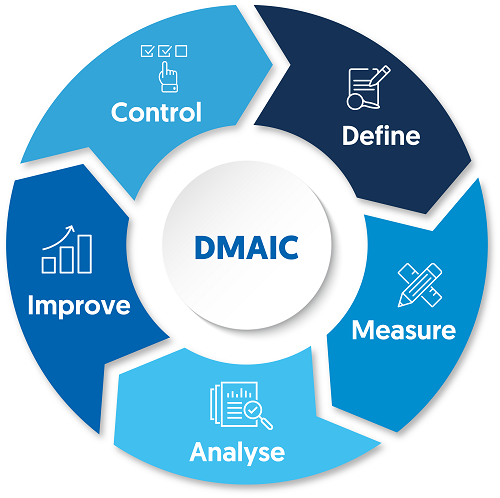
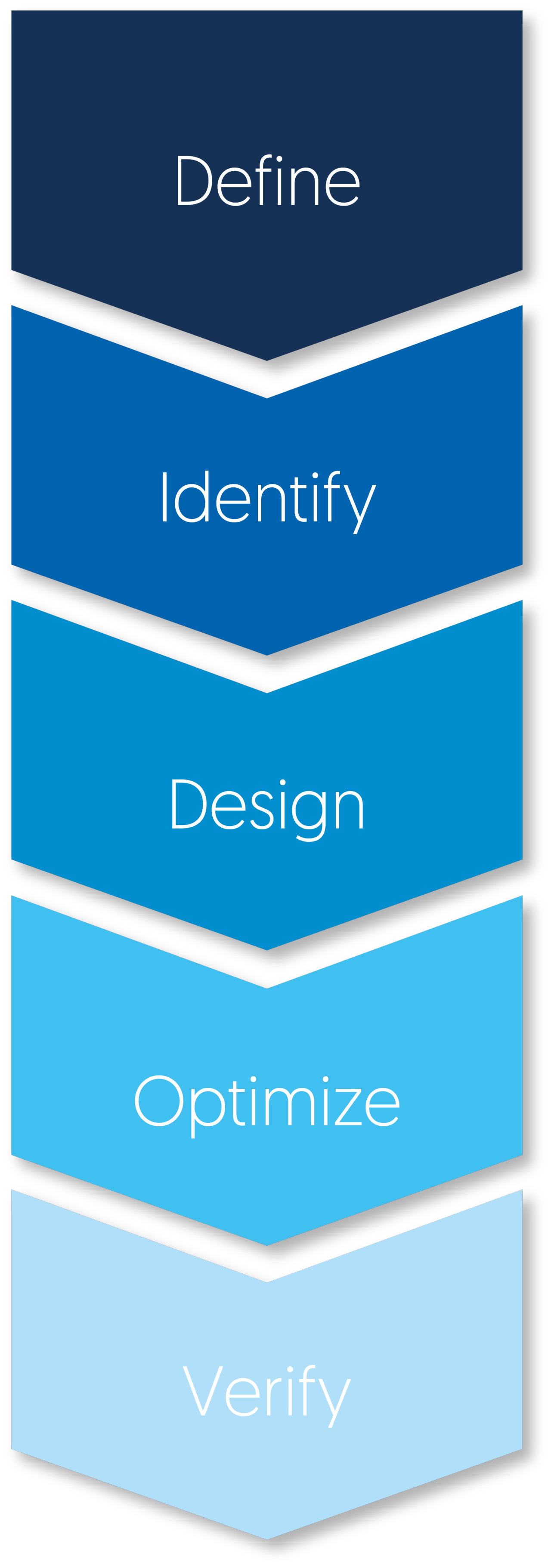

Stakeholders: the ideal project team for your machine design
In addition to the design process, your stakeholders also play an important role in the journey towards a new machine. That is why you want to consider the various interests of your stakeholders and their influence on the project early. This allows you to inform all stakeholders about the course of your project, and get them on board in time.
Mechanical Engineer and/or Project Leader
Depending on the size of the project, the (mechanical) engineer is often also the project leader. It is therefore possible that you are wearing two hats. The data that is produced, analysed, interpreted and distributed in a project is very extensive.
Buyer
How do you bridge the gap between procurement and engineering? The higher the budgets involved in the project, the sooner the buyer will claim a seat at the table. In general, the following applies: you want the part with the best specifications, they want to reduce costs where possible. There is an obvious area of tension between the two. It is therefore important to not merely discuss pricing, but above all focus on the safety and minimum quality of the machine (parts).
Supplier
Selecting the right supplier for machine parts is essential. Look for a party that acts as a technical partner and has the right people in-house to make the crucial difference to your designs. From the actual design to packaging materials and the supply chain, a good supplier will think along with you in all areas.
RACI-model
Use proven methods such as the RACI model to decide what information is important to which stakeholders, and where responsibilities lie.
The RACI model helps you to determine who should be involved for each step in the process:
- Responsible: this person is responsible for the successful completion of this step.
- Accountable: the person who approves the step, once the work has been done. Only one person can be accountable per step/activity.
- Consulted: these are the people who are participating/actively giving input in the activity.
- Informed: you have to keep these people informed of what is happening. However, they are not actively involved and have no decision-making authority.
Mapping out the people involved in each step and what their role is will help you keep the project on track. The chance that you will forget to ask someone for input or send out information is a lot smaller this way. It also prevents people from feeling left out. Everyone knows how annoying it is if your project is delayed because someone thinks you should take two steps back.
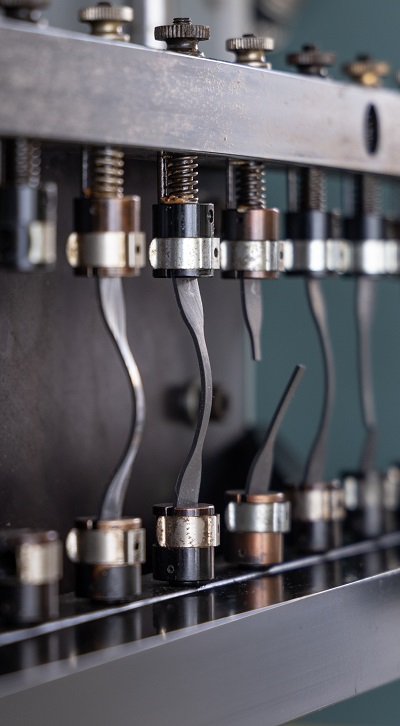
Contact
Direct contact
Want to speak directly with one of our employees or specialist? Don’t wait and get in touch
General contact
Get in contact with us. Please fill in our online form and we will contact you as soon as possible.
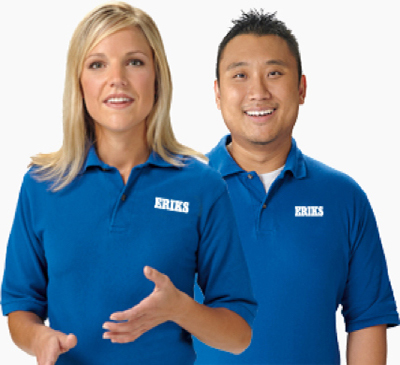