Food safety: legislation and regulations
Complex laws and applications. How do you keep an overview?
A handful of straightforward food safety laws are easy to deal with. But when the sector gets flooded with rules and regulations (which is the case), it becomes tricky for food professionals too.
All materials that come into contact with food products, such as packaging or even the rubber of a conveyor belt, must meet legal standards. These requirements are relatively easy to manage. But food safety legislation becomes increasingly more complex due to the sheer number of regulations. EC1935/2004, EU 10/2011, EC2023/2006, FDA and HACCP are just a few of them.
How do you keep an overview within this maze of rules and regulations? Read the overview and discover how all these rules relate to food safety legislation.
Quickly navigate to topic

EC1935/2004
The EU legislation EC1935/2004 became effective on 24 October 2004 and applies to all food contact materials, packaging and other objects that (potentially) come into contact with food. EC1935/2004 identifies 16 groups of food contact materials:
- 1. Active intelligent materials and objects
- 2. Adhesives
- 3. Ceramics
- 4. Cork
- 5. Rubber
- 6. Glass
- 7. Resins with ion exchangers
- 8. Metals and metal alloys
- 9. Paper and cardboard
- 10. Plastics
- 11. Printing ink
- 12. Generated cellulose
- 13. Silicone
- 14. Textiles
- 15. Varnishes and coatings
- 16. Wax

No. 2023/2006
In order to guarantee the (food) safety of materials mentioned above, the EU has implemented Regulation 2023/2006, listing Good Manufacturing Practices. In addition, the Dutch government has drafted national legislation in the 'Packaging and Utensils Regulation’.
EC1935/2004 framework
Article 4
Article 4 describes requirements for 'active and intelligent materials’
Article 5
Article 5 describes special measures. This includes the list of authorised substances.
Article 6
Article 6 describes that EU-members may formulate their own regulations as long as they comply with EC 1935/2004.
Article 16
Article 16 describes that materials and objects are required to carry a written declaration stating their compliance with the conditions set out in Article 5.
Article 17
Article 17 describes traceability, meaning that products can be tracked through all stages of production, processing and distribution. Read more in our blog on Traceability.
Read more about EC1935/2004 legislation (pdf)
Declaration of Compliance
A written Declaration of Compliance (DoC) confirms that production materials meet all legal requirements and do not exceed the permitted migration limits. The DoC is described in Article 16 of EC1935/2004.
Did you know that you can trace this statement all the way from end user to supplier? The DoC is therefore an important prerequisite to guarantee traceability.
Purpose of the Declaration of Compliance
- Verifying that food businesses have all required documentation in place and ensuring that the information contained therein is correctly applied.
- The correct and safe use of packaging materials and food products.
The requirements for a Declaration of Compliance vary by material category. A limited number of material categories are regulated at European level (such as for plastics in EU 10/2011).
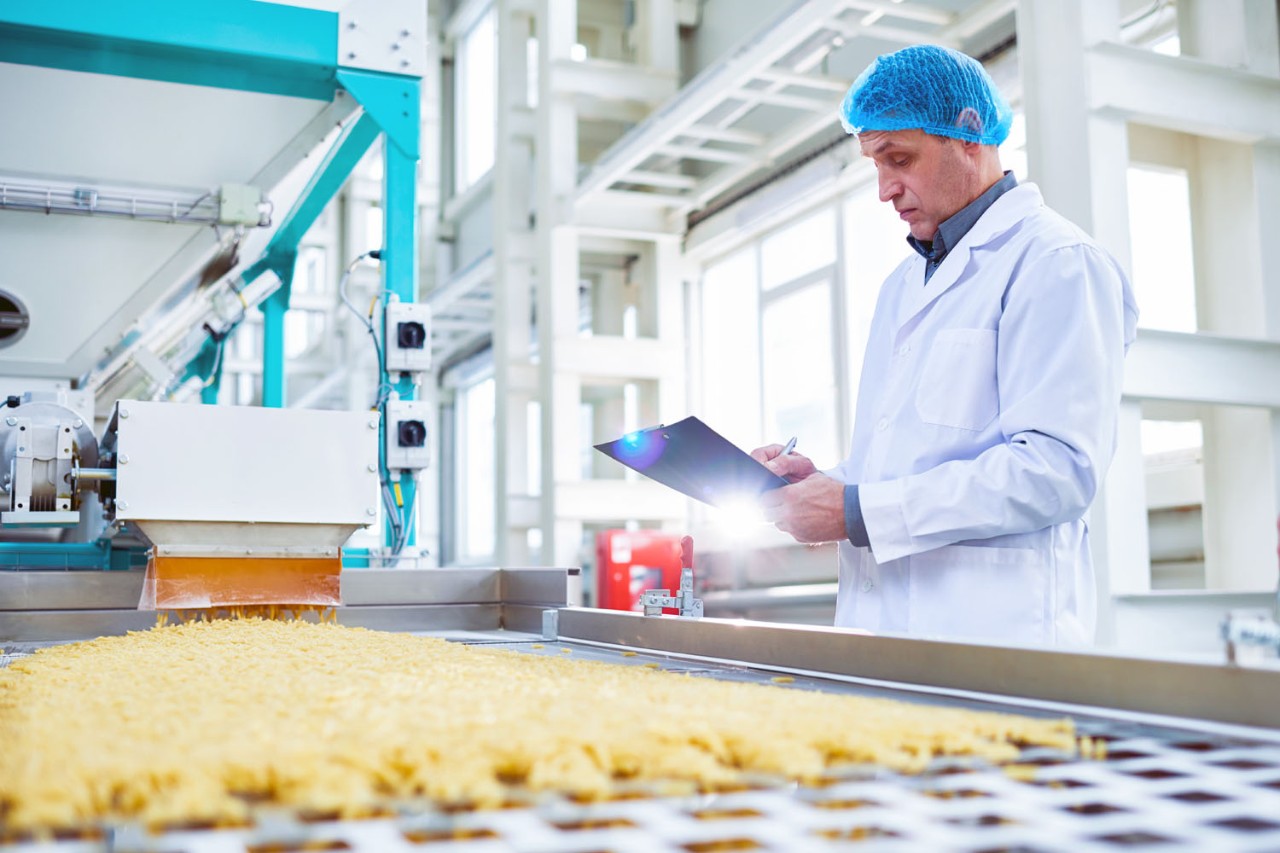
Extra regulations for special food contact materials
Article 5 contains a list of special food contact materials that must be manufactured in accordance with additional regulations (such as EU 10/2011 for plastics). These 'Good Manufacturing Practice' are listed below.
Good Manufacturing Practice [GMP]
In order to ensure that food contact materials do not pose a risk to consumers, regulations for good manufacturing practices have been established. This includes EC2023/2006, better known as: Good Manufacturing Practice. EC2023/2006 applies to all sectors and all stages of the production process. In addition to the three conditions mentioned in Article 3 of EC1935/2004, manufacturers must also have a quality-management system in place.
In EC023/2006, 'Good Manufacturing Practice' is defined as follows:
- 1. Quality-management system and quality policy
- 2. Management responsibilities for GMP are assigned (and documented) and staff are trained to work with food contact materials
- 3. Hygiene policy
- 4. Documentation, labelling and traceability
- 5. Production
- a. Material specifications for raw materials
- b. Preventing contamination
- c. Documented operating procedures, policies in place when changes occur
- d. Storage of goods, packaging and transport
- 6. Quality control and specifications
- 7. Work performed outside the production zone is subject to a written contract describing the GMP
- 8. Customer complaint handling, product recalls and incident management
- 9. Regular internal and external audits
Read more about EU 10/2011 | Read more about EC2023/2006
EU 10/2011
EU 10/2011 is better known as the plastics regulation. This comprehensive EU regulation describes how plastics should be manufactured, but also contains a list of substances that may be used for the production of such plastics. Other materials for which similar regulation exists are: ceramics (EG84/500), generated cellulose (EG2007/42), recycled plastics (EG228/2008) and active and intelligent materials (EG450/2009).
EU 10/2011 applies to:
- Materials, objects and parts made entirely of plastics
- Materials and objects composed of multiple layers of plastics (bonded by adhesives)
- Plastic materials and objects printed with coatings or overlays
- Plastic gaskets in lids (EG2002/72)
The following requirements apply for the Declaration of Compliance:
- Name and address of manufacturer
- Product identification (description, item number, etc) to ensure traceability
- Date of the declaration
- Confirmation that items comply with EC1935/2004 and EU 10/2011
- Information on migration limits and substance specifications
- Information on food additives; the additives should be named to avoid overconcentration.
- Specifications for use
- What type of food product is this material suited for?
- How long may materials be in contact with food products?
- At what (maximum) temperature is the material suitable for coming into contact with food products?
- At what ratio has the material been tested and found suitable?
What about the rest of Europe?
EC1935/2004 only calls for a separate regulation for plastics. This means that EU members are free to make their own regulations for the other listed materials. In this way, manufacturers not only have to comply with EC1935/2004, but also take into account the different regulations that apply in the European Union. Moreover, each country enforces these regulations differently.
For example:
- France requires stainless steel to contain at least 13% chrome.
- The organoleptic test described in Article 3 is mandatory in Germany, whereas in France it is only required for ‘high-risk’ materials.
- In 2017, Belgium implemented a new law that defines how varnishes and coatings that come into contact with food should be handled.
The Commodities Act
In the Netherlands, food safety is described in the Packaging and Consumables Commodities Act Decree. This is further described in the Packaging and Consumables Regulation. Although EC1935/2004 is leading for the Commodities Act, a number of additional rules have been added:
- The regulation states that 12 out of 17 materials listed in EC 1935/2004 (including plastics), are permitted in the production of packaging or utensils that come into direct contact with food.
- The decree describes what a Declaration of Conformity should look like for those materials that are not already defined in the European legislation.
FDA
Before EC1935/2004 was implemented, it was often still acceptable to only comply with FDA legislation. Since the European law was introduced, this is no longer the case. This does not mean that FDA and EC1935/2004 regulations are similar, or that the FDA enforces the same rules as in Europe.
Food Safety Modernization Act
The FDA is the food safety authority in the United States. The FDA implements its own legislation and is best known for the 2011 Food Safety Modernisation Act. The act includes 7 rules:
- Production safety: Regulations for the production of fresh fruit and vegetables.
- Preventive control for food intended for human consumption: Every food facility is obliged to carry out a risk analysis and implement preventive control measures.
- Independent party accreditation: This enables independent parties to carry out food facility audits.
- Foreign Supplier Verification Programmes: Importers from the United States will have to check foreign products for safety.
- GMP and risk analysis for animal feed
- Strategies to avoid (intentional) contamination
- Hygienic transport of food products
Dutch companies are obliged to carry out a Food Safety Plan and to be able to show it to the American importer.
Food contact materials
Sections 170-199 of the FDA regulations describe food-safe packaging materials for use in the food industry. These include:
- Plastics
- Paper and cardboard
- Polymers
- Additives
- Adhesives
A part of the FDA regulations is the Food Contact Notification (FCN). This tool allows companies to register new materials. The FCN states how to handle migration testing and toxicology reports.
Read more FDA

Contact
Direct contact
Want to speak directly with one of our employees or specialist? Don’t wait and get in touch
General contact
Get in contact with us. Please fill in our online form and we will contact you as soon as possible.
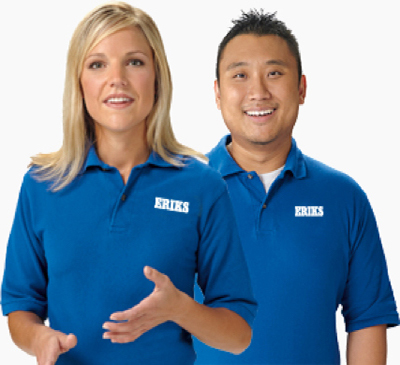