In this article
Food grade materials in your food-safe production process
Food safe production should be self-evident in the food industry. But what do we mean by 'food safe' ? And what is meant by ‘food-grade’ - a term commonly used in the context of food safety? This article will explain the various concepts and the importance of clear laws and regulations for materials and processes within the food industry.
Food-safe material is not enough in itself
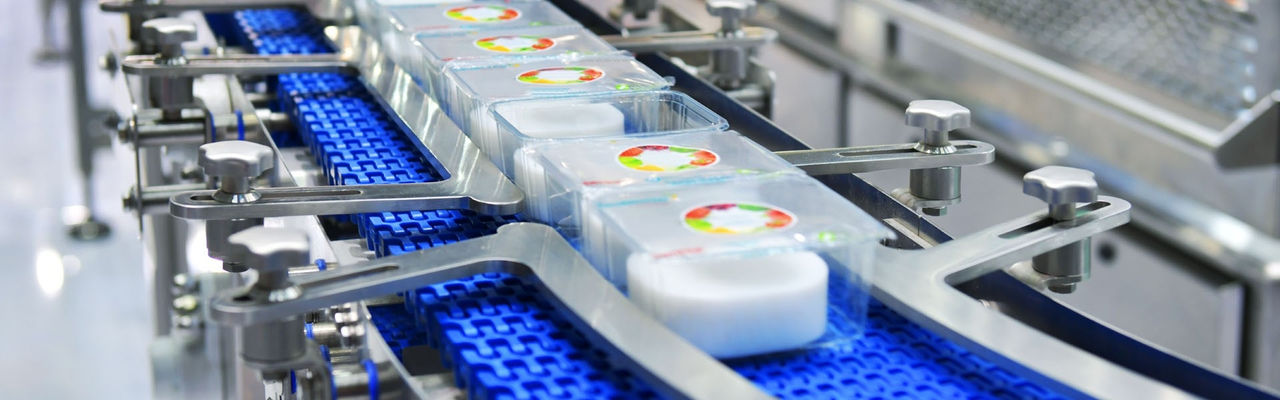
At ERIKS, we are often asked to supply a ‘food-safe’ material. When we supply food producers with processed plastic which is used in their production environment and comes in contact with food, our product always conforms with the applicable EC1935-2004 regulations. It can be described as a ‘food-grade material.’ This means that the material is suitable for coming in direct contact with food. That is different from the concept of ‘food-safe’, which means that the food-grade material and the manufacturer's end product are suitable for final consumption and do not pose a food safety hazard. This is an important distinction because, as a producer in the food industry, you can buy food-safe materials for your production process, but if your production process is not carried out according to GMP (Good Manufacturing Practice) requirements, the end product may still not be food-safe.
Laws and regulations in the food industry
If you are a producer operating in the food industry, there is really only one regulation that applies throughout Europe, and that is EC1935/2004. This regulation lists the requirements which materials must comply with when they come in direct contact with food. For example, a plastic product supplied by ERIKS should comply with regulation EC1935 if it can come into contact with food anytime during the production process. Uniformity of laws and regulations is certainly a great benefit to internationally operating companies. The arrival of EC1935 has significantly increased efficiency within the (international) logistics chain, and the risk of contamination and other food safety hazards have sharply decreased.
Within EC1935/2004, ‘sub-laws’, such as EC1935/2004 - 10/2011, have been developed for different materials. This legislation focuses specifically on plastic. The main reason for the focus on plastic in EC1935/2004 is that increasingly more types of plastic are coming into contact with food. And the regulations provide a framework for all producers in the food industry:
- General provisions that all materials must comply with
- Full traceability of materials
- Requirements for material identification
- Designations, labelling of products
- A Document of Compliance (DOC) with the appropriate migration tests that proves the materials used do not cause any alterations to the food.
Good Manufacturing Practice
As a supplier of materials used in the food industry, ERIKS is always committed to full compliance with the regulations and supplying food-grade materials. We carry out all our processes according to the Good Manufacturing Practice (GMP), which falls under EC1935/2004. It is impossible to determine a product's quality just by analysing the composition. GMP ensures that you record in detail how and under what conditions a product is made. All raw materials, intermediate products and end products are checked during the production process, and the process is rigorously monitored. By doing this, you map out the entire production chain, the quality of the materials is continually monitored and safeguarded, and the material used is always traceable.
The purpose of GMP is to safeguard the correct processing of materials and products. This quality check assures the consumers that a product complies with the set quality standards, is correctly labelled and conforms to legal requirements. We believe that quality control alone is not enough to ensure compliance with the highest quality standards. Building quality and reliability in every single product should be standard practice within every organisation.
Show me your certificate…
The Netherlands Food and Consumer Product Safety Authority (NVWA) monitors compliance with EC1935/2004 laws and regulations. Enforcement takes place on a random basis, which means that most companies don’t have a great urgency to meet the regulations. What often becomes a real eye-opener for manufacturers is when a recall occurs with major consequences. A well-known recent example is the recall in 55 countries of Mars bars in which particles of plastic were found. In addition to the considerable operational costs, this also had a significant negative impact on the manufacturer's reputation.
It is noticeable that when this kind of thing occurs, there is always an immediate surge of interest in food safety and requests for certificates. But this surge ebbs away again just as quickly. At ERIKS, we always check if our clients have the necessary certificates. If they say they do, we always check if this information is correct. Many manufacturers will say they ‘got the materials from the supplier.’ In doing so, they ignore the fact that the certificate belongs to the material supplied, but they are responsible for any changes to the material during the production process.
ERIKS stands for safe food production
At ERIKS, we see that insufficient compliance and lack of proper certificates are rarely intentional. Within large manufacturing companies, there are often only a handful of people concerned with food safety, and this is at a time when most producers in the food industry are struggling to keep up with the demand for food products. Faster production, less downtime and higher output are essential for these companies. More work is expected from the machines, and this can result in less maintenance or shorter maintenance time due to more thorough cleaning. Extra steam or caustic soda can then cause problems, for example. More wear and tear on material increases the risk of non-food-safe production.
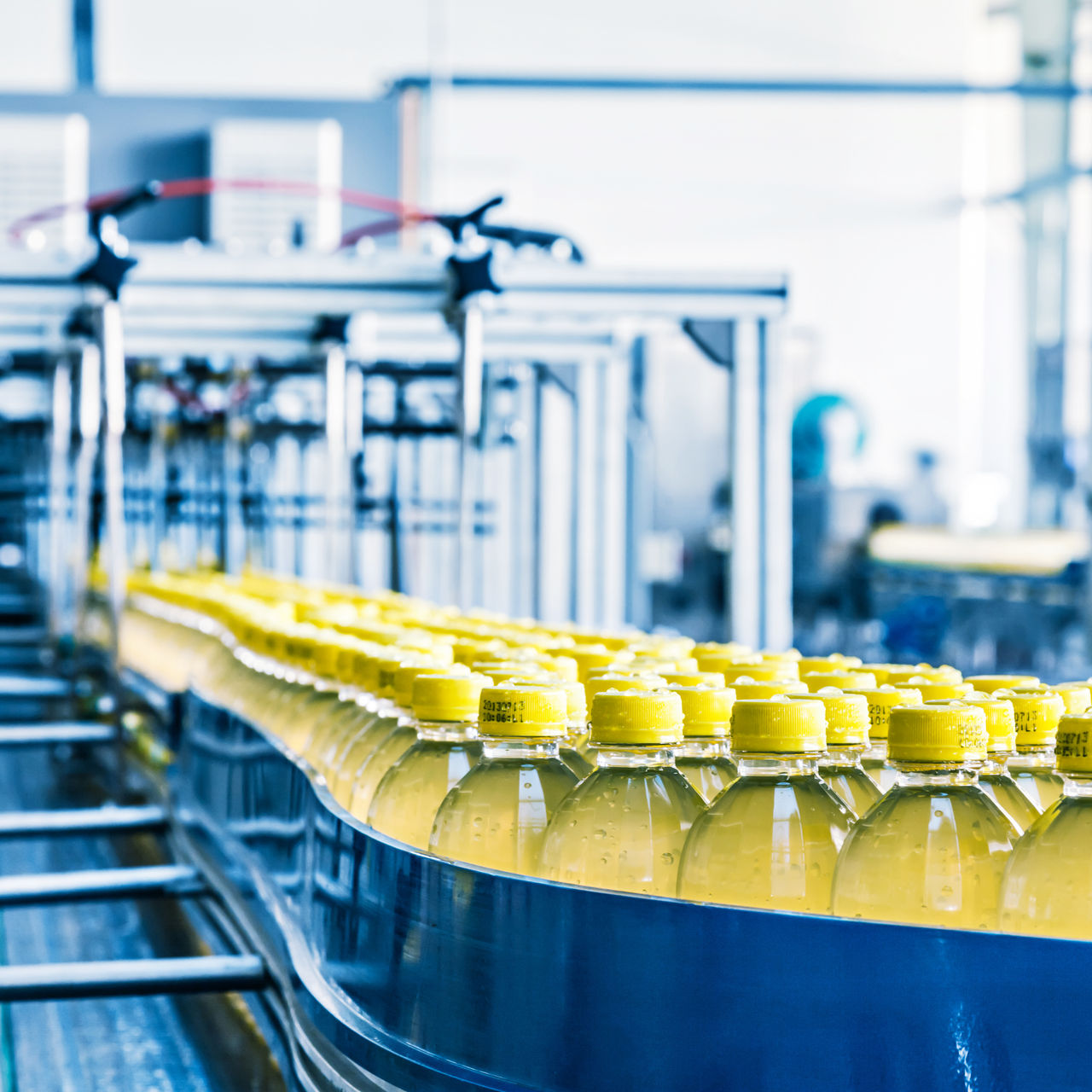
ERIKS has developed a step-by-step plan to create support and prioritise food safety. Logistics, quality control, purchasing and sales departments should all be involved in the process. Every department receives its own instructions for setting up the food-grade process efficiently. This creates a team of experts who know exactly what to do when a delivery comes in. If a certificate is missing during the food-grade check, the material will be set aside until the certificate has been arranged. Simulating a recall situation is another good way to experience its effects organisation-wide. By telling buyers and engineers how we organised our food-grade process, we hope they will be just as dedicated to it as we are!
Would you like to know more about food-grade materials and how we can support you in setting up a successful quality-control process for food safety? Don’t hesitate to contact one of our ERIKS experts, we'd love to talk to you!
Subscribe to our newsletter:
For the latest industry news and updates.