In this article
Seal optimisation with Finite Element Analysis
Seals are crucial within any production process to ensure efficient and safe operation of machines, devices and their components. A seal works optimally when the dimensions of the seal itself, the groove in which it is placed and the counter parts are perfectly matched. The choice of material is also a determining factor. With Finite Element Analysis, we show our clients how the seal will perform within their application and production environment. The ideal tool for a fast and cost-efficient development process.
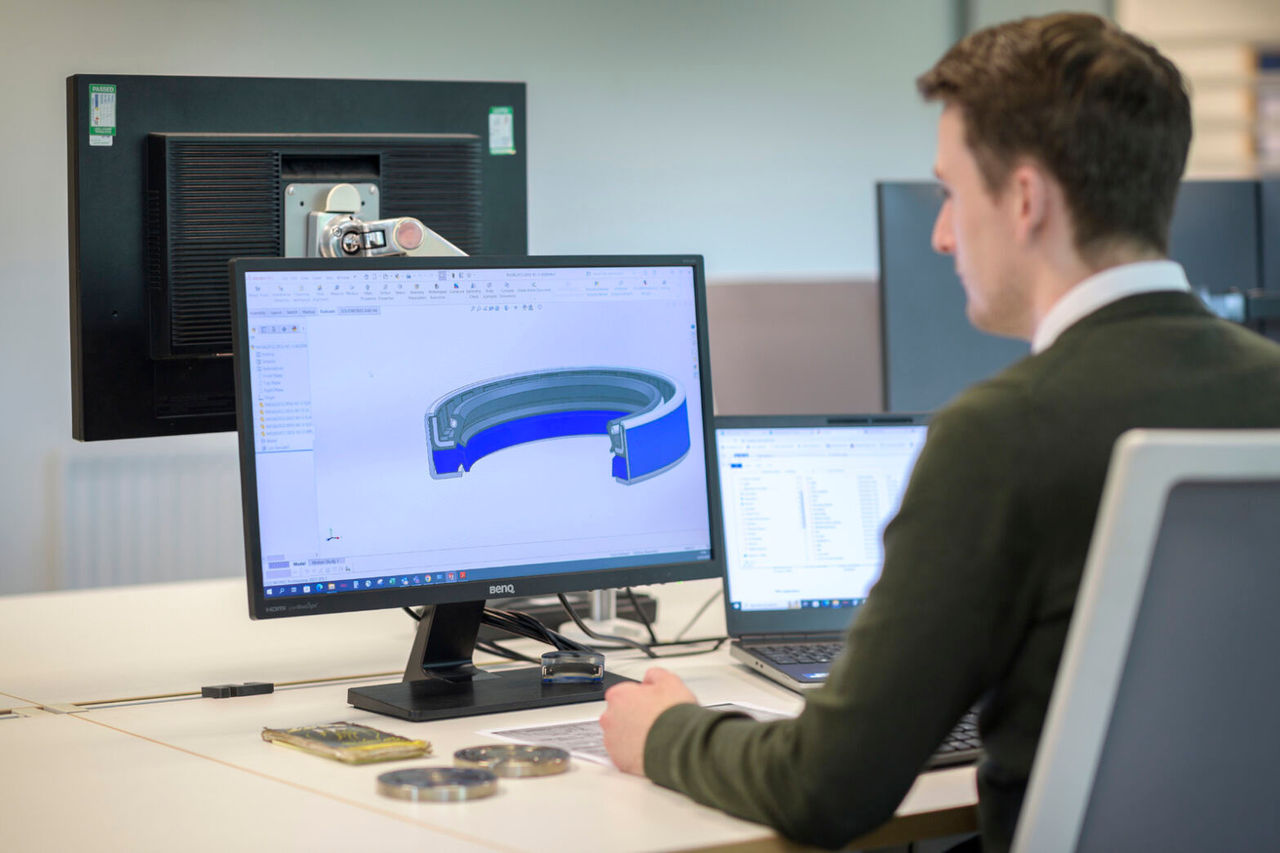
How does Finite Element Analysis work?
To answer customers' questions about whether seals will work well within their production environment, Finite Element Analysis (FEA) is the solution. This advanced software makes it possible to simulate the behaviour of the rubber seal without having to physically test it. To successfully perform a simulation, a 3D model of the groove and counter parts within the structure is already sufficient. Based on the medium, temperature and pressure within the application, we select a number of rubber materials suitable for sealing. The combination of the 3D model and the material model forms the starting point of the simulation.
Tailored Solutions via Extensive Data Analysis
Finite Element Analysis is suitable for measuring different materials with varying properties under varying production factors. This ensures customisation, so you always develop the most suitable seal for your application. Depending on the complexity of the design, it is possible to add specific data to the simulation to test the seal's behaviour even better. Think of friction, viscoelastic behaviour and thermal expansion. An example is gauging the installation force: what reaction force do the parts exert? This is particularly relevant for plastic components, where excessive force during installation can lead to deformation.
Data predicts how your seal responds to future conditions
With FEA, you can also determine the range of a seal within an application. For an O-ring, this is usually quite straightforward, but when it comes to more complex shapes, FEA is a perfect tool to gain insight into this. Testing how rubber reacts at different temperatures is also an important part of FEA. When temperatures fall and rise, rubber shrinks or expands. Rubber expands when you heat it to 200 degrees, but also shrinks several percent when you let it cool down again. For a mould maker, for example, this information is very important before developing the product. With FEA, you make shrinkage simulations that perfectly mimic the behaviour of the rubber in that process.
The benefits of FEA
The simulation software quickly calculates different scenarios. This enables an iterative design process to achieve the best end result. FEA thus ensures clear benefits at every stage of the development process.
Efficient and cost-effective design process
Since the simulations require only minimal-sized rubber slabs or buttons, this approach ensures a swift development of the optimal seal. By working with simulation software, you almost always arrive at the optimum seal for your application. A first-time-right result of your seal will thus save you considerable costs.
Optimal quality of the end product
Our comprehensive material model database guarantees the optimal and reliable selection of the most suitable material for your application. Any combination of available material, production environment and application can be tested with FEA. So that you always choose the right seal for your application.
How does ERIKS help develop the right seal?
At ERIKS, our Finite Element Analysis includes a comprehensive suite of test models that consider all variables to ensure optimal sealing.
- behaviour in the groove
- geometric distortion and compression
- compound choice
- fatigue of the material
- material stress
- the design
- the influence of temperature and pressure changes
- tolerances
In some industries, companies are also well capable of performing calculations through their own FEA, especially when it comes to dynamic installations. ERIKS supports these processes by sharing input with available material models.Upon successful calculations, seals are designed using materials from ERIKS. Without performing the calculations ourselves, we can still optimally support customers in the development process.
Subscribe to our newsletter:
For the latest industry news and updates.