In this article
Environmental monitoring saves energy and costs
Sustainability has become an important part of any business strategy. This is partly necessary due to tighter legislation and regulations, but in particular also due to the growing awareness among industrial companies that they can produce much more sustainably. They often don't know that they can also make substantial cost savings in the process. With our environmental monitoring solutions, we support companies in making their production environment more sustainable with the right energy-saving solutions.
Sustainability requires insight
When it comes to sustainability, the will is often there, but only the insight to make the right decisions to develop a sustainable or even more sustainable production environment is often lacking. Certainly for companies with complex and extensive production facilities, it often proves difficult to translate production data into concrete solutions that contribute to increased sustainability. With the result that people stick to existing processes and the ambition to become more sustainable fades more into the background. Whilst the opportunities for more sustainable and more cost-effective production are usually plentiful at those very companies. Environmental Monitoring offers a solution.
Environmental impact
Environmental Monitoring is a broad term. The main aim is to measure the impact that different machinery or parts of the production process have on the environment. Energy consumption and CO2 emissions are determining factors in this. The monitoring process analyses data obtained from various inspections over a particular period of time. The results may trigger changes to be made in the production process. Small adjustments in the technology used or using different materials/components in the production process often have a major impact. And can also deliver substantial cost savings.
Another important aim of Environmental Monitoring is compliance with applicable legislation and regulations. The ambitious sustainability targets from the Paris Climate Agreement, as well as the government's reluctance in recent years to encourage industrial sustainability, are now accelerating the implementation of legislation and regulations in this area. Monitoring processes carefully track whether the production process (or parts thereof) comply.
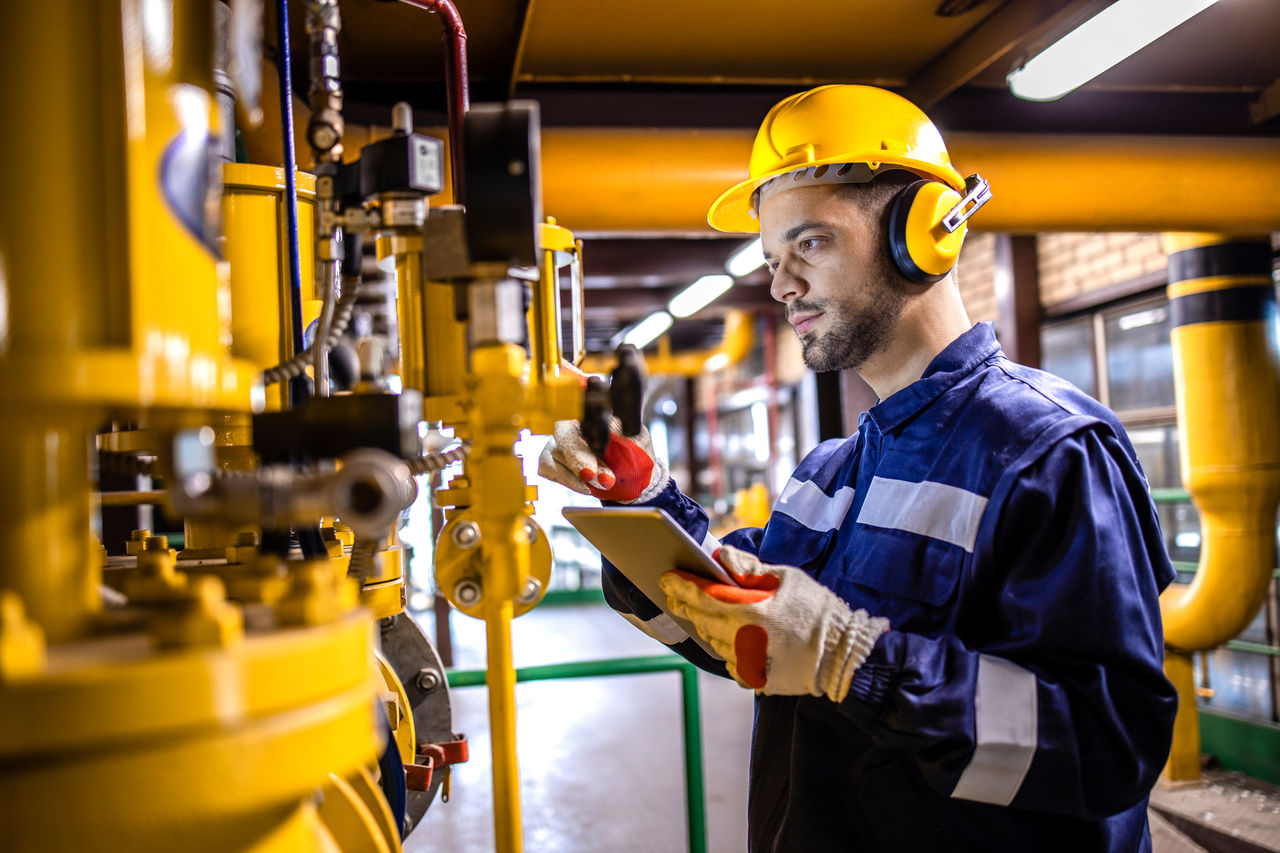
Processes with the most impact
Reduced energy consumption contributes most to sustainability: both for the environment and the lower energy costs and taxes you pay as a producer. Environmental Monitoring, therefore, focuses on machinery parts and processes where energy plays an important role, such as:
- Steam systems with steam traps
- Compressed air systems
- Pumps and hoses
- Electric motors
- Conveyor systems
Steam systems with steam traps
Steam systems are an important part of the Environmental Monitoring process. Indeed, much of the energy lost in a production facility is caused by faulty steam traps. If a steam system is not monitored regularly, chances are that after three years, about a quarter of the steam traps will lose steam. This leads to higher energy bills and a heavier burden on the environment. By checking steam traps regularly, you make substantial savings on energy consumption.
A periodic Steam Trap Survey investigates how steam traps are functioning in your production environment. If necessary, leaking steam traps can be replaced immediately. It also takes a critical look at using the right steam trap for your application. A different type of steam trap can contribute to more energy-efficient production. Steam specialists use a steam trap survey to map out your entire plant in this way.
Compressed air systems
What companies often fail to realise is that air in a production facility is very expensive. Research also reveals that air leakage is the leading cause of energy loss within industry. During inspections, ERIKS specialists regularly come across air leaks averaging 20% of capacity. While in properly functioning compressed air systems, this percentage should never exceed 5%. All the more reason, therefore, to carry out regular air leakage inspections to keep expensive air in your systems and prevent energy loss.
An air leak inspection is only successful if the complete compressed air system is checked thoroughly. By assessing which air leaks contribute most to the air loss, repair work can be organised according to priority. Conducting this inspection periodically will not only keep down the number of leaks and associated repair work, it will also reduce downtime and reduce your energy costs substantially.
Pumps and hoses
We often see incorrect pump sizes being used. An oversized pump does not function as optimally as it could and consumes much more energy than necessary. The correct (smaller) size ensures substantial energy savings. This is because the consequence is that you use a smaller motor to power the pump. An investment that often pays for itself within a year. A periodic check on the functioning of the pumps in your systems not only increases the safety of the production process; by replacing pumps in a timely manner, you produce a lot more effectively and energy-efficiently.
Periodic inspection of the hoses used in your production environment is another important part of Environmental Monitoring. ERIKS' Field Service Engineers carry out complete hose inspections and tests that check whether the hoses are still in good condition and whether they function optimally within the application in which they are being used. Results regularly show that other hoses respond more efficiently to the medium, temperature and pressure, thereby saving energy and reducing environmental risks.
Conveyor systems
Conveyor systems that are outdated and require a lot of maintenance consume a lot of energy. By regularly checking the efficiency and energy consumption of your conveyor systems, adjustments can be made in time and, if necessary, parts can be replaced that optimise operation. This is because these systems are mostly driven by geared motors: small electric motors that have built-in drives with worm screw gears. Gear units are increasingly fitted with helical gears and have a much higher efficiency, saving considerable energy.
Replacement with an energy-efficient system, where less maintenance ensures less downtime, is another cost-effective solution. The great advantage of a designed conveyor system from ERIKS is that all parts of the drive train fit together well. Enabling you to minimise energy consumption. Periodic checks ensure that this remains the case.
Energy saving in practice
To implement sustainability as efficiently and successfully as possible within a production environment, companies need a partner that combines all knowledge into concrete solutions. ERIKS not only carries out scans and monitoring processes to identify where energy can be saved, we also have the technology and process solutions available in-house to implement this sustainability at customers' premises. This makes ERIKS the partner of choice for many major companies to work with for a sustainable, energy-efficient future.
Monitoring of existing processes
In 2016, ERIKS started its first steam trap surveys for a major customer with an extensive, complex production site with several plants. This was still on a small scale and took place in a few plants. Five years later, we presented a larger and more comprehensive plan, which led to the decision that the services to identify the potential savings could not be paid from the maintenance budget but from a budget allocated specifically for that purpose. We then scheduled and implemented various services. We rolled these out across the entire site, 11 plants in total. The Steam Traps Survey has now been undertaken at eight plants; we continued with this in early 2023.
Initial scans revealed that not every plant had an optimally functioning steam system. There were defective steam traps and parts that had to be replaced for more energy-efficient alternatives. From 2022, as a Strategic Service Supplier, we actually started replacing and making their steam systems more sustainable. The result? We have already delivered over €1.5 million in (potential) savings in one year through reduced steam losses. A similar amount can be saved annually up to 2030, provided that the parts are also replaced in time. The challenge with this client is that in many plants, production continues day and night. Once every few years, one might be idle only to be restarted after a few days. So much work has to be done in those few days that replacing steam traps is sometimes left untouched.
In 2022, we also carried out the first air leakage inspections, during which we also detected air leaks. The pilot phase for this is ongoing. But with the findings we have made so far, we are already seeing many opportunities to make savings. Targeted solutions can fix leaks and then contribute to energy-efficient production. Consider the replacement of valves, which are actuated with air to seal it all off. We also see small air pipes with couplings running in each facility that dry out and become loose. With the proposed improvements, we can save over €13 million by 2030 by reducing air loss.
Substantial cost savings through reduced energy consumption
While there is still much to be gained in using energy-efficient motors, they are not yet in use at most production facilities. Energy-efficient motors are not only found in the installation but also in buildings, for example, in the ventilation or cooling systems. When increasing sustainability, a company almost always chooses to install solar panels first. But if you compare the average output of solar panels in kW to the increased efficiency of energy-efficient motors, the savings you can make by using more efficient electric motors are three times higher!
Project teams at ERIKS are currently working hard to see where quick wins can be achieved and how adjustments in the production environment can lead to reduced energy consumption, reduced CO2 emissions and a positive impact on the company's stated environmental objectives in the long term. After all, the most sustainable energy is saved energy. If the full potential of proposed sustainability solutions is exploited, this customer could make over €115 million(!) in cost savings by 2030.
Want to know more about environmental monitoring and how it can help to make your production environment sustainable or more sustainable? Then feel free to contact one of our experts.
Subscribe to our newsletter:
For the latest industry news and updates.