In this article
Design for Six Sigma: From customer demand to proven solutions
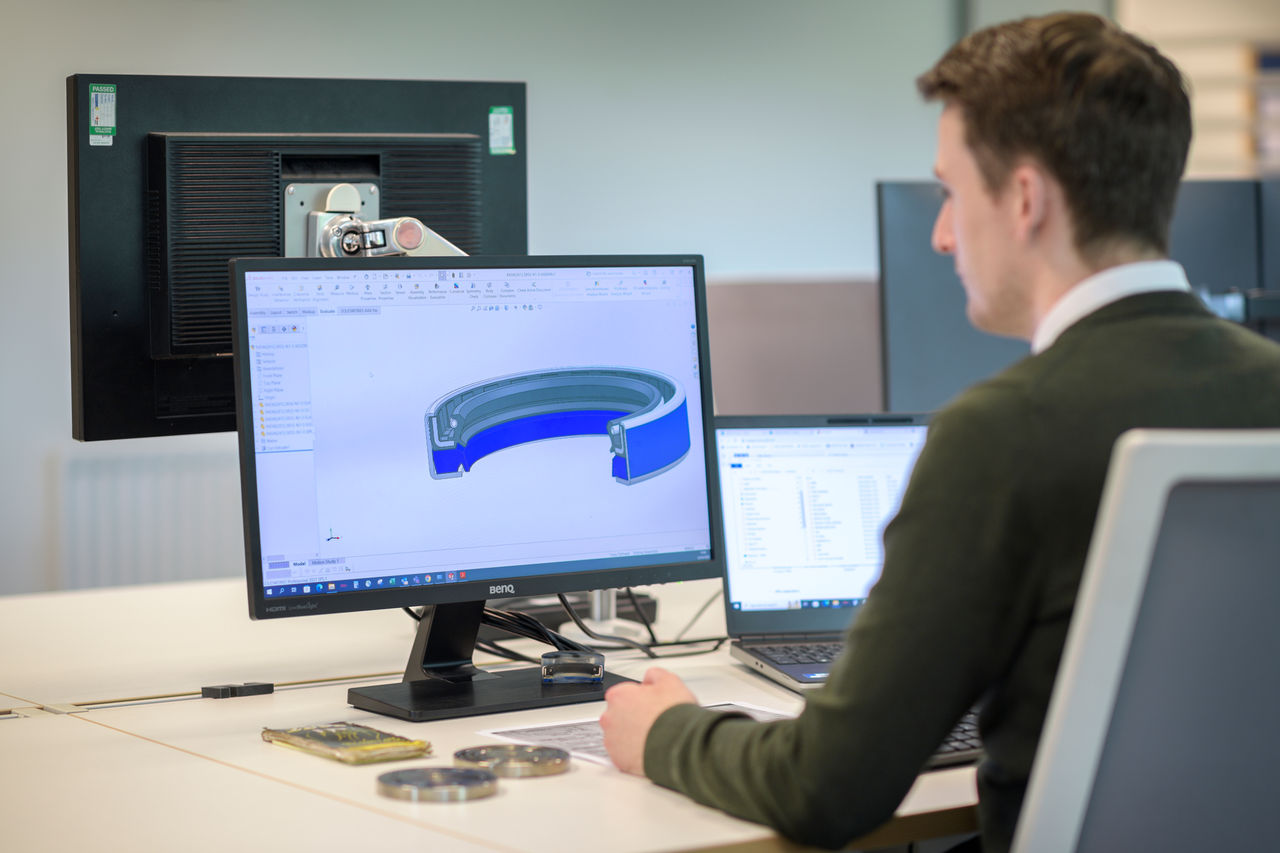
At ERIKS, we adopt the Design for Six Sigma (DfSS) approach across the organisation. This systematic method enables us to develop new products and production processes that perform at a Six Sigma quality level. For our customers, this results in the design and delivery of tailored solutions that align with their needs and expectations. Job van de Sande, Head of Engineering, explains why ERIKS has chosen DfSS and the added value this approach provides for our customers.
Why ERIKS chooses DfSS
ERIKS often delivers customised solutions for complex customer challenges. Most of our work originates from specific customer requests. Whether it’s selecting an existing product or component, modifying it (what we call customisation), or co-engineering, where we collaboratively undertake a complete engineering process with the customer.
Since many projects at ERIKS begin with a customer query, it’s vital to thoroughly understand their needs and expectations. This enables us to translate these requirements into a high-quality, efficient end product. By employing the DfSS methodology, we can fully meet the stringent standards required in the industry.
“The choice for DfSS allows us to accurately translate our customers’ challenges into specific product and process designs,” Van de Sande explains. “Other methodologies, such as APQP, are widely used in industries like automotive, but ERIKS has chosen DfSS because it places the customer’s voice at the center. With a deep understanding of the Voice of the Customer (VOC), we precisely define the customer’s core needs and translate them into technical specifications. Throughout the project, we repeatedly verify these specifications to ensure compliance, not only for the first product but also for the hundredth or even the ten-thousandth product in the series. This leads to a reliable production process and the development of a robust product.”
DfSS as a way of working
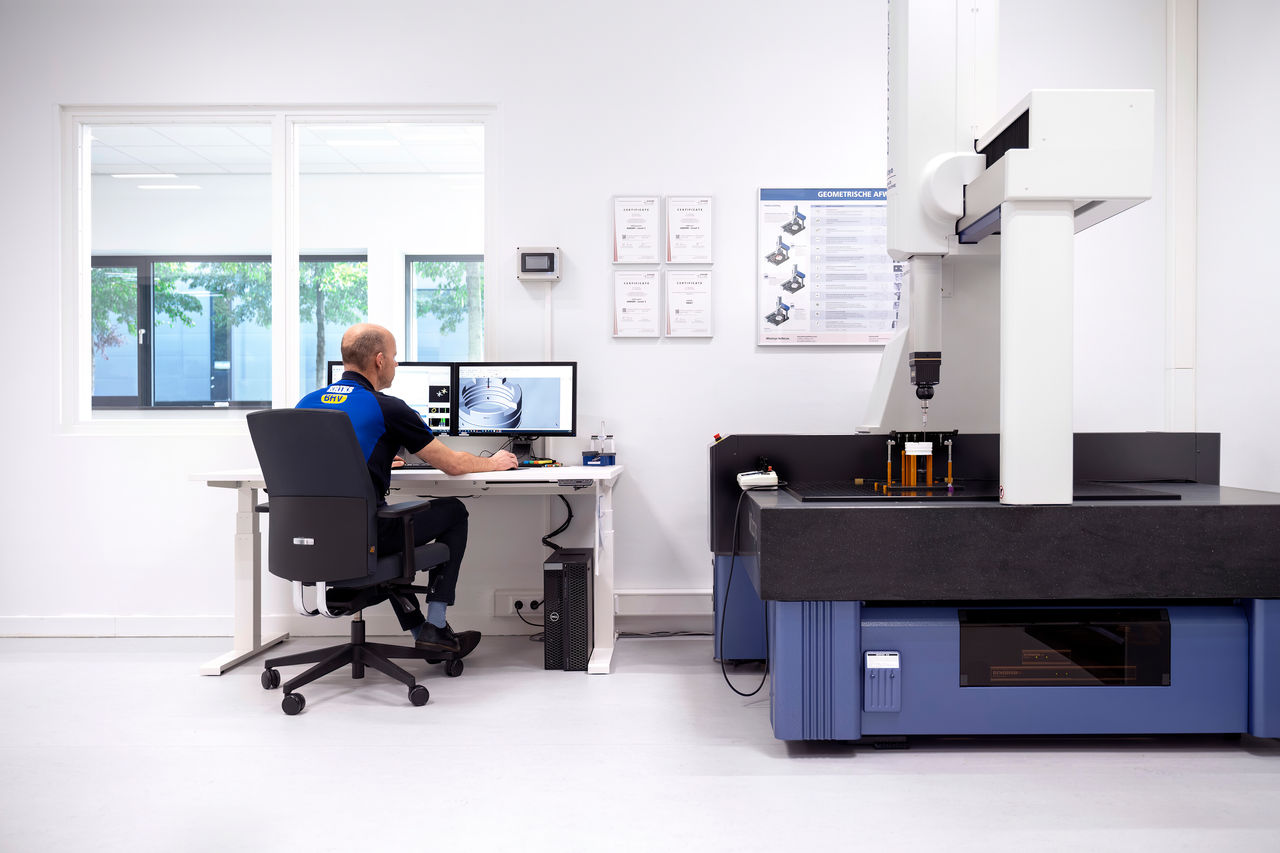
At ERIKS, DfSS is more than just a philosophy. It has been fully integrated into our team structures, planning, project, and documentation tools. It is central to our Quality Assurance Manual and Quality Management System (QMS), ensuring that DfSS is deeply embedded in our core processes.
Van de Sande highlights the importance of DfSS as a driving force across the organisation. “By standardising the process with DfSS in our project tools, our engineers can focus on the significant variability in product designs, processes, and production conditions. Devoting attention and time to these aspects results in a higher-quality end product. DfSS ensures that risks are identified and minimised early, leading to fewer revisions and lower operational costs. Furthermore, the use of DfSS methodologies helps increase efficiency and drive continuous improvement, aligning with ERIKS’ core values of customer satisfaction and innovation.”
Integrating DfSS into ERIKS’ QMS provides a standardised, structured approach to quality control, which is crucial in sectors such as Food, Pharma, semicon, and machinery manufacturing. “By explicitly adopting DfSS as a development standard, we not only enhance the predictability of project outcomes but also ensure compliance with strict quality standards and regulations,” Van de Sande explains. “This reinforces our position as a reliable, high-quality partner, demonstrating our focus on maximising customer value in terms of quality and solution longevity, not just on minimising costs.”
The added value of DfSS for customers
The benefits of DfSS extend beyond internal quality control and process optimisation. It also offers clear value to our customers by ensuring higher product quality and reliability.
Higher-quality products
Since DfSS emphasises the “first time right” principle, quality and reliability are integrated into the design phase from the outset. By effectively applying risk analyses, simulations, and statistical optimisations, such as Failure Modes and Effects Analysis (FMEA), Finite Element Analysis (FEA), and Design of Experiments (DOE), we optimise product performance.
With the improved quality of the end product, DfSS minimises costs associated with rework, waste, and warranty claims. As a result, customers benefit from lower overall costs and increased reliability of delivered products.
More efficient development cycles
DfSS leverages the “V-Model” design approach, which focuses on isolating, developing, and testing critical sub-components. By iteratively developing and testing sub-components before the assembled system, costly redesigns are avoided, significantly reducing development time.
This approach enables our engineers to respond quickly to changes in customer requirements while ensuring a faster time-to-market.
DfSS strengthens data-driven innovation
In the rapidly changing industries where ERIKS operates, innovation is increasingly driven by data. Van de Sande explains how DfSS promotes a data-driven approach to design and innovation, further enhancing solution reliability and quality.
“DfSS inspires engineers to back their designs with data, ensuring solutions are repeatable, reliable, and robust. The tools within DfSS are geared towards this goal. While we rely on technical drawings and concepts, statistical validation proves that our solutions are optimal and durable. Simulations, rapid prototyping, and statistical analysis combine technical intuition with hard evidence, ensuring that the best solutions are developed.”
DfSS: the standard at ERIKS
ERIKS prioritises DfSS as the sole design methodology, fully committing to it as the industry standard. This dedication to a consistent, standardised approach builds trust with customers and ensures seamless guidance throughout the process.
“There are many companies that still mix their own methodologies with industry standards,” says Van de Sande. “At ERIKS, we don’t. This commitment is a strength because our customers approach us with complex challenges in specific industries. To gain their trust, we must adhere to industry norms rather than rely on proprietary methods. DfSS is simply one of the best methodologies available.”
ERIKS and DfSS: a future-proof combination
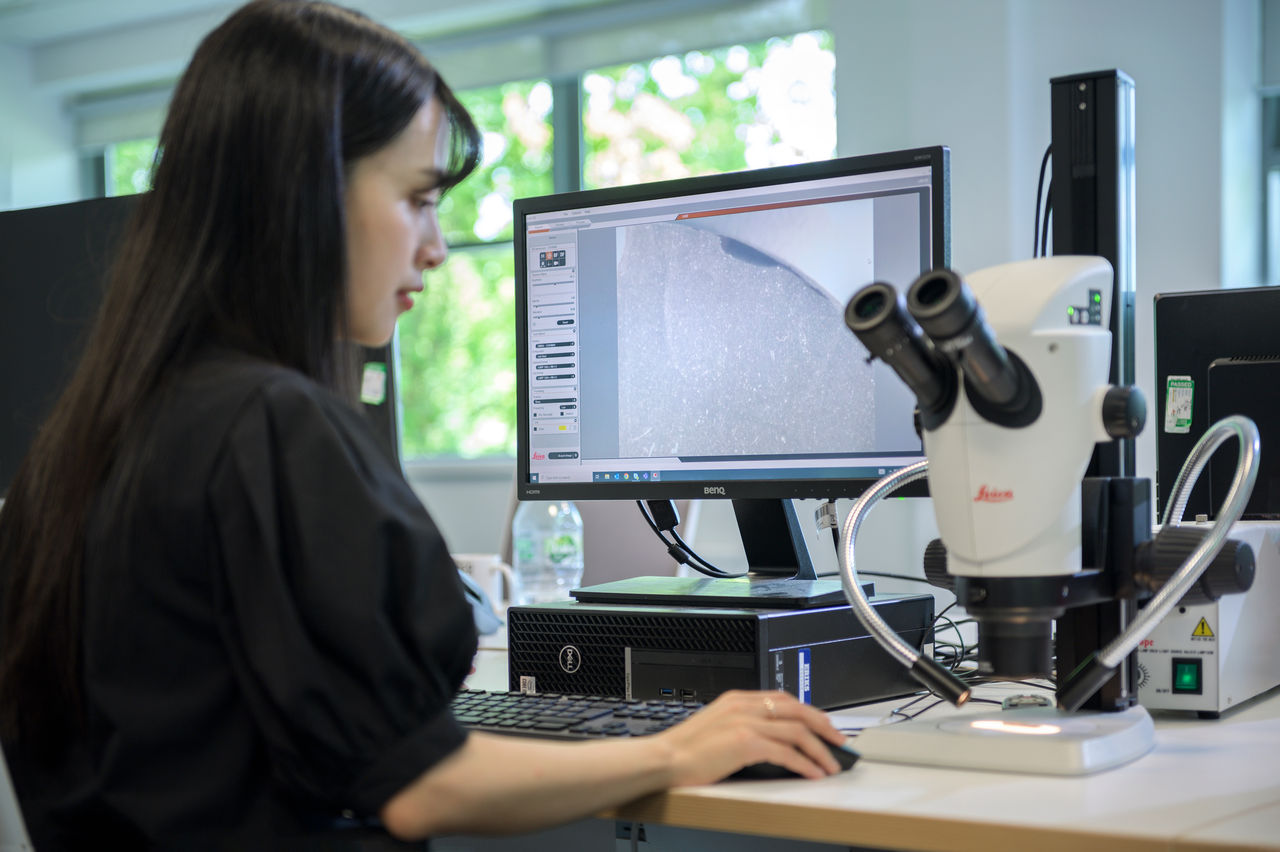
ERIKS’ adoption of DfSS is an investment in customer satisfaction, efficiency, and innovation. By listening to customers and working with standards like DfSS, ERIKS effectively translates customer demands into reliable, tailor-made solutions. For us, DfSS is more than a methodology; it’s a strategy for creating lasting customer value, with innovation, data analysis, and customer focus at its core.
“With all ERIKS business units using the same methodology, we enhance collaboration across units and borders, ensuring everyone understands the steps taken and those still required. With DfSS, we continuously demonstrate to our customers that their needs are understood, the best solutions are delivered, and designs are backed by data and best practices.”
Subscribe to our newsletter:
For the latest industry news and updates.