In this article
Engineering of Assemblies: expertise for rapid product development
One of the most important parts within the industry is the development of machines used in production or supporting business processes. Almost every machine consists of multiple parts that need to be assembled into a single unit to work optimally. In this article, we will tell you more about this process of Engineering of Assemblies. And we highlight some industries in which it plays an important role.
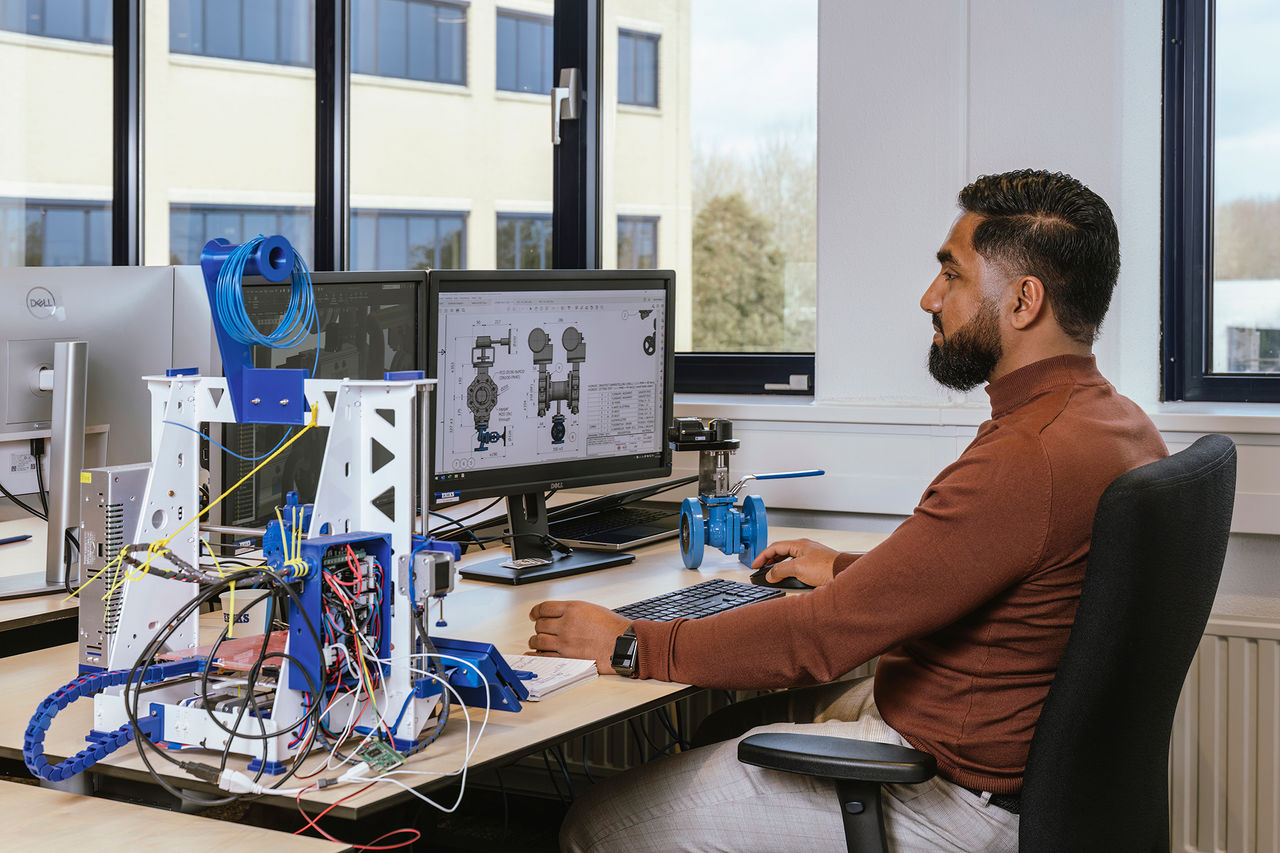
Engineering of Assemblies: From Design to Customer Needs
Engineering of Assemblies combines individual components to form a final product that aligns with the customer's specifications. It is often a complex process in which design, engineering, manufacturing and logistics are defining components. The start of any successful Engineering of Assemblies process is carefully coordinating with the customer what the assembled product is needed for. Understanding the production environment and associated production factors is a second step. Next, it is up to the assembly engineer to define the exact function of the final product and how the individual parts should function together. Based on the desired materials, dimensions, tolerances and design, the engineer can select the right parts. After which the production process can start to connect all the parts together in the right way.
Engineering of Assemblies can be part of the development of a new product to be launched on the market. A professional, correct design of individual parts is very important in this. Engineering of Assemblies can also be applied to support OEMs in producing machines that are part of their customers' production or business process. Engineering of Assemblies in the second case is much more about selecting the right parts with the right specifications. So that the final product fully meets the customer's needs and requirements.
The biggest challenges within Engineering of Assemblies
There are many factors that influence the Engineering of Assemblies process. This brings several challenges that every assembly engineer faces at some point during the assembly and development of the product. There are some generic challenges that an assembly engineer may face:
Customer knowledge of their own production environment - Most customers find the production part less interesting, they are often (logically) only interested in the solution they need. This also means that they are not always as knowledgeable about all the production factors that affect the composition of individual parts in the assembly process. A challenge that requires more initiative from the assembly engineer to map the customer's production environment as well as possible.
Time is valuable - The duration of the assembly process can vary quite a bit. When a production environment calls for a complex application, it usually takes more time to select parts that meet the requirements. Time is extremely valuable when the production process comes to a standstill due to a machine failure. If a new machine needs to be assembled at short notice, delivery times can be quite challenging. If a new machine is designed and developed, it requires more time anyway. The design usually goes back and forth several times, a lot of testing with different materials and functionalities is required. Usually, time is a given, but it can be a challenge when the customer has a deadline when the new machine has to be delivered at a certain time.
Brand consistency - It is desirable to use parts of the same brand within a specific assembly process. However, it frequently happens that an assembled machine or device (by necessity) consists of parts from different brands. In practice, this can cause problems. Consider parts that meet the set standards, but the materials of each part have different tolerance values. When you put parts from different brands together, you usually don't have data when something goes wrong. You also want to be able to go back to the same supplier if it turns out that a particular part needs replacing again after a few years. Integrating parts from multiple brands can then cause delivery problems.
Engineering of Assemblies in practice
Engineering of Assemblies takes place in almost every industrial sector and within every production environment. At ERIKS, Engineering of Assemblies is used as widely as possible. And we support all kinds of suppliers and companies in developing machines and equipment that meet their requirements and the demands their production environment places on the end product. Hydraulic Hoses and Lubrications are two business units where Engineering of Assemblies is regularly involved.
Lubrication System Engineering
Lubrication is essential for any production environment to keep machinery running properly. From idling machines to vehicles used for transportation. With applications in the food industry to steel production. This is because every clutch that rotates needs oil or grease to function properly. The Central Lubrication Systems division sells parts or complete installations for, for example, hydraulic presses and gear pumps. Basically everything the customer needs to have their machinery properly lubricated. This unit preferably sells complete installations to the customer, first purchasing individual parts which are then assembled according to the customer's requirements.
What does a Lubrication System actually look like? The process starts with the type of medium required. Is it oil, grease or is it something in between? It is also important to consider the location of the application where lubrication is required. Since ERIKS supplies products worldwide, the temperature of a production environment can vary considerably. A next step is to select the best pump for the application. This could be a gear pump or a pistol pump. Also part of the system is a number of variable speed drives (feeders) that monitor and control how much bearings or couplings need to be lubricated. The operation of the system requires a pressure gauge, relief valves to control the pressure and sensors that keep track of when the tank in which oil or grease is stored needs to be replenished. The system can also be fitted with a timer, where the system operates independently, pumping a dose of oil or grease into the system every 24 hours, for example.
The department may pick up only a single part of this or work with the entire system. Advice is also given on how companies can best set up the lubrication system themselves. In this, ERIKS supports them with technical data, such as how long the pump can be on before pausing and how long this pause lasts before switching it on again.
Hydraulic Hoses Customization
A hose is never sold separately as it has no value to the customer. You also need a ferrule (cap made of metal/adhesive sleeve) and a fitting. Everything has to be attached to each other. Only then you have a solution that matches the customer's requirement: a hydraulic system. These systems are found in every industry where high pressure plays a role. They are regularly used in production environments where oil is pumped. But they are also used when, for example, water, gas or air must be moved under high pressure.
The assembly process of a hydraulic hose is fairly straightforward. Basically, the hose , ferrule and fitting form a hydraulic system. A big advantage of hydraulic systems is that standards are widely used. These are necessary because standards in a high-pressure production environment ensure a safe working environment. As mentioned earlier, it happens that the hose, ferrule and fitting, which all meet the same standards and can be applied within the same production environment, can come from three different brands. However, a hydraulic system with components from the same supplier is desirable.
Case studies
For Varian, a supplier of medical instruments, we assembled PTFE hoses for their new range of modern devices. It was a big challenge to meet all requirements. When evaluating the correct type of hose, various PTFE hoses were tested here using a special test procedure. A special thermal oil is pumped through these hoses. This is radiatively irradiated. The selected hose does not diffuse, this means that there is no oil leakage and therefore represents the best result for our customer in this application. The engineering process itself was fairly straightforward, as we were sent the right parameters and were able to assemble the right size of hose and corresponding fittings in them. The small size of the hose shows that we are able to realise customised applications within any industry and sector. Regardless of the dimensions and scope of the project.
Another customer, Jackcontrol, is a specialist in microtunnelling. They use a jacking system to dig small tunnels for pipelines and canalisation. We support them with the assembly of hoses for tunnelling projects. For us, the biggest challenge at the beginning of this collaboration was developing a production line capable of assembling hoses of the required large sizes. That means you need space, manpower. We were able to achieve that very well. Another challenge has to do with the 'cutting tolerances'. These are based on DIN standards. The DIN tolerances in this case are higher than what is usable for the customer. That means we have to produce the hoses smaller than DIN indicates. It called for an adjustment in the production process that allows us to customise the assembly even more and supply the customer with hoses that exactly meet the required dimensions.
ERIKS delivers added value in Engineering of Assemblies
ERIKS has extensive experience in Engineering of Assemblies. At every stage of the development process, we have the know-how to carry out assembly successfully. Our technical expertise, in which we carry out many tests together with the customer and support them in developing the right technical solution, is a powerful tool in this. In addition, we have a very large network. We can help think about the required solutions at the start of the project, we have direct access to all parts, we assemble the parts ourselves into one system and we can deliver the end result anywhere in the world.
A good example is the recent delivery of a large lubrication unit, with cooling and heating elements. The system was destined for Namibia, but distribution was handled entirely by ERIKS in different European countries. We contributed to the design and then ERIKS Germany picked up the rest of the process and also eventually organised the transport. A perfect collaboration in design, assembly, production and logistics!
Subscribe to our newsletter:
For the latest industry news and updates.