Seals: 4 factors to select the right rubber material
Consider pressure, medium, temperature and time to choose the best kind of rubber for your seal
Rubber is a special material. Not only because it can take any shape, but also because of its diverse properties. That’s why it’s a definite favourite among seal materials. However, rubber is a collective name, as there are dozens of polymers and even more compounds. So how do you choose the right rubber for your seals? There are four factors to take into account.
The importance of the right seal is often underestimated. Unjustly so, because making the wrong choice has severe consequences. In the design phase of a machine or component this results in rework, higher costs and a longer time-to-market. In an application that is already up and running, you risk leakage, failure or even accidents. And nobody wants that.
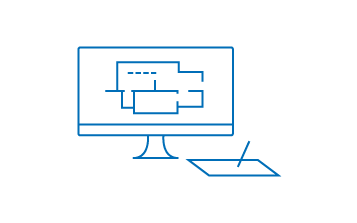
Medium, temperature, pressure and time
The four factors that determine the type of rubber seal you need are:
- Medium
- Temperature
- Pressure
- Time
Medium, temperature, pressure and time say a lot about the requirements the seal must meet. These factors also have a major influence on the performance and design of the rubber seals. Other aspects such as the shape, operating time and, for example, quality brands are also important. Would you like to know more about this? Download the Sealing Guide.
Always having the right seal for your design?
Download the Sealing Guide and discover the 5 key pointers that will make sure your seal always works.
- An existing or new design
- The application of your machine or component
- Medium, temperature, pressure and time
- Operating time
- Specific requirements such as traceability and certification
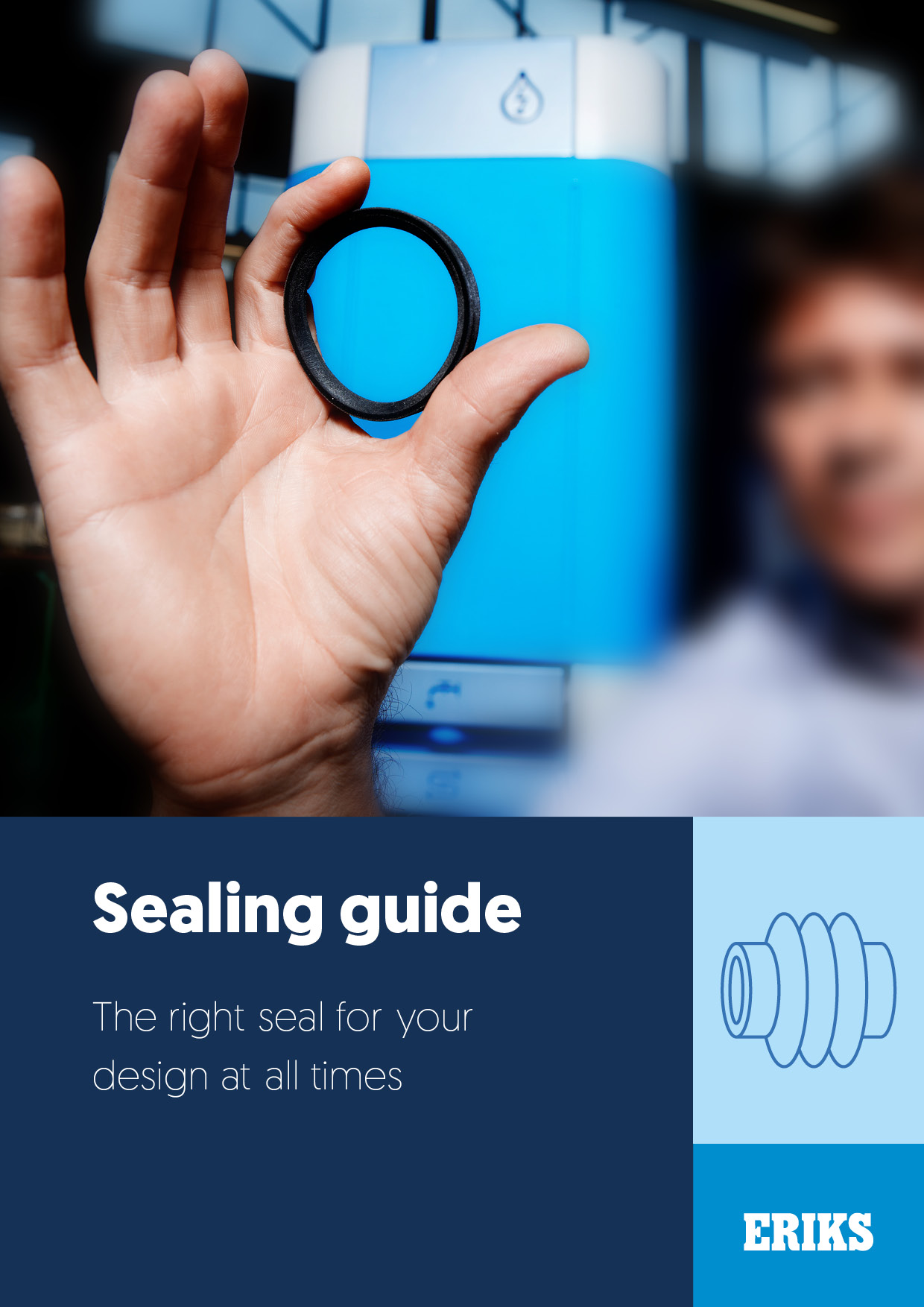
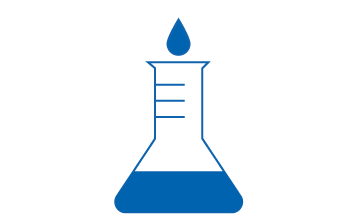
Medium: what does your seal come into contact with?
A rubber seal comes into contact with various substances - called media. When the machine is running, but also during the cleaning process, for example. Not every compound can tolerate all media, so this factor plays an important role in making the right choice.
Media consists of 3 main categories:
- Liquid
- Gas
- Solids
Each kind of rubber reacts differently to different substances when it comes to abrasion resistance, gas permeability, swelling, etc.
When choosing a suitable material always consider all media the seal will come into contact with. For example cleaning materials, lubricants and any media in the immediate vicinity of your application.
Temperature: how hot or cold will it be?
The temperature is also of great influence on the functioning of a seal and tends to vary due to internal (application of the machine) or external influences (climate or cleaning with hot steam). Does the seal come into contact with high or perhaps extremely low temperatures? To what extent and how often does the temperature change? The answer to these questions will bring you closer to the ideal seal.
However, temperature is not an isolated entity; the combination of temperature, time and media is usually the determining factor.
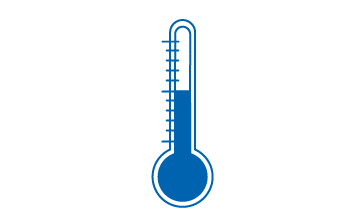
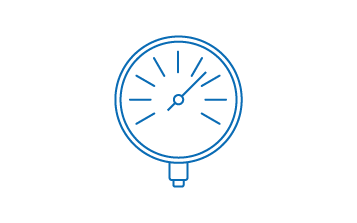
Pressure: how high is it?
Specific rubber seals can, once fitted, withstand very high pressures of up to hundreds of bar. Just think of hydraulic seals. But beware: not all materials perform at the same level under high pressure. This results in the risk that the seal will no longer function properly or that it will wear out quicker than expected. Also, consider how often and for how long the seal will be under pressure. In order to find the material you prefer, you have to know the pressure exerted on a seal.
Higher pressure often goes hand in hand with a higher hardness of the material you need. Medium, temperature and time often determine the choice of the polymer type, but pressure often determines the hardness of the polymer type.
Just like with temperature, the combination of pressure and time plays an important role.
Time: for how long do temperature and pressure apply?
In combination with temperature, pressure and medium, time also has an important influence on the choice of a seal. Here, you look at the time the seal is exposed to operating and peak temperatures. This means you need to be aware of the temperature a component can be exposed to, but also how often it’s exposed to that temperature. It makes a big difference if the seal has to seal 10 minutes a day under a certain temperature, or day and night.
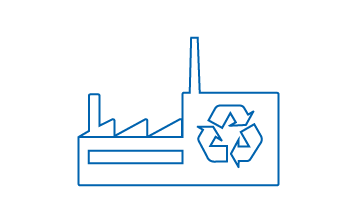
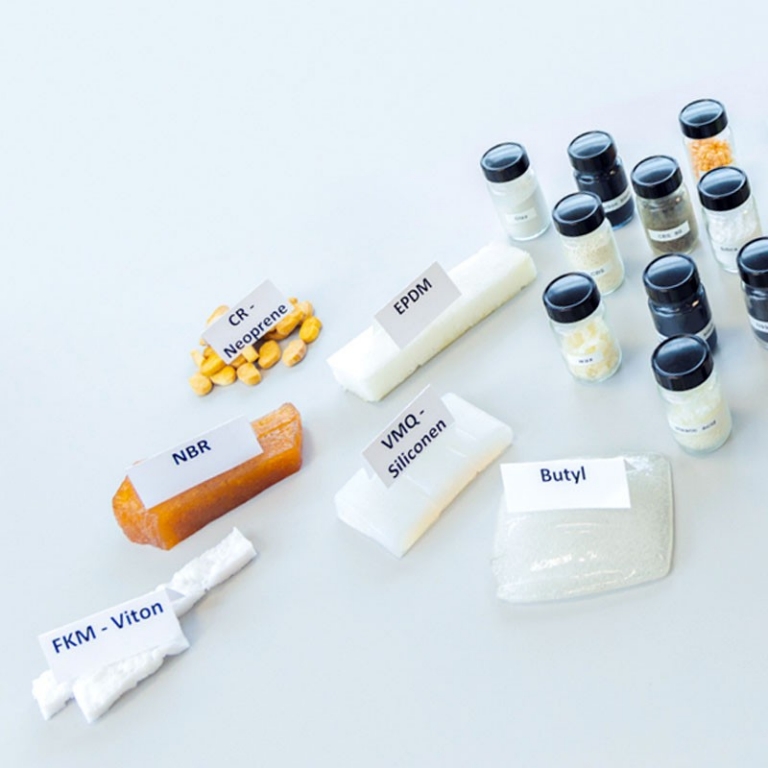
Choosing the right rubber seal
As you can see, there are quite a few factors that influence the choice of the right material for a seal. Have you thought about medium, temperature, pressure and time? Then you've already taken some great steps. But that's not all. Shape, operating time and the required certificates are just a few elements that influence the choice of a seal.
Always the right seal for your design
Download the Sealing Guide and discover the 5 key pointers that will make sure your seal always works.
- An existing or new design
- The application of your machine or component
- Medium, temperature, pressure and time
- Operating time
- Specific requirements such as traceability and certification
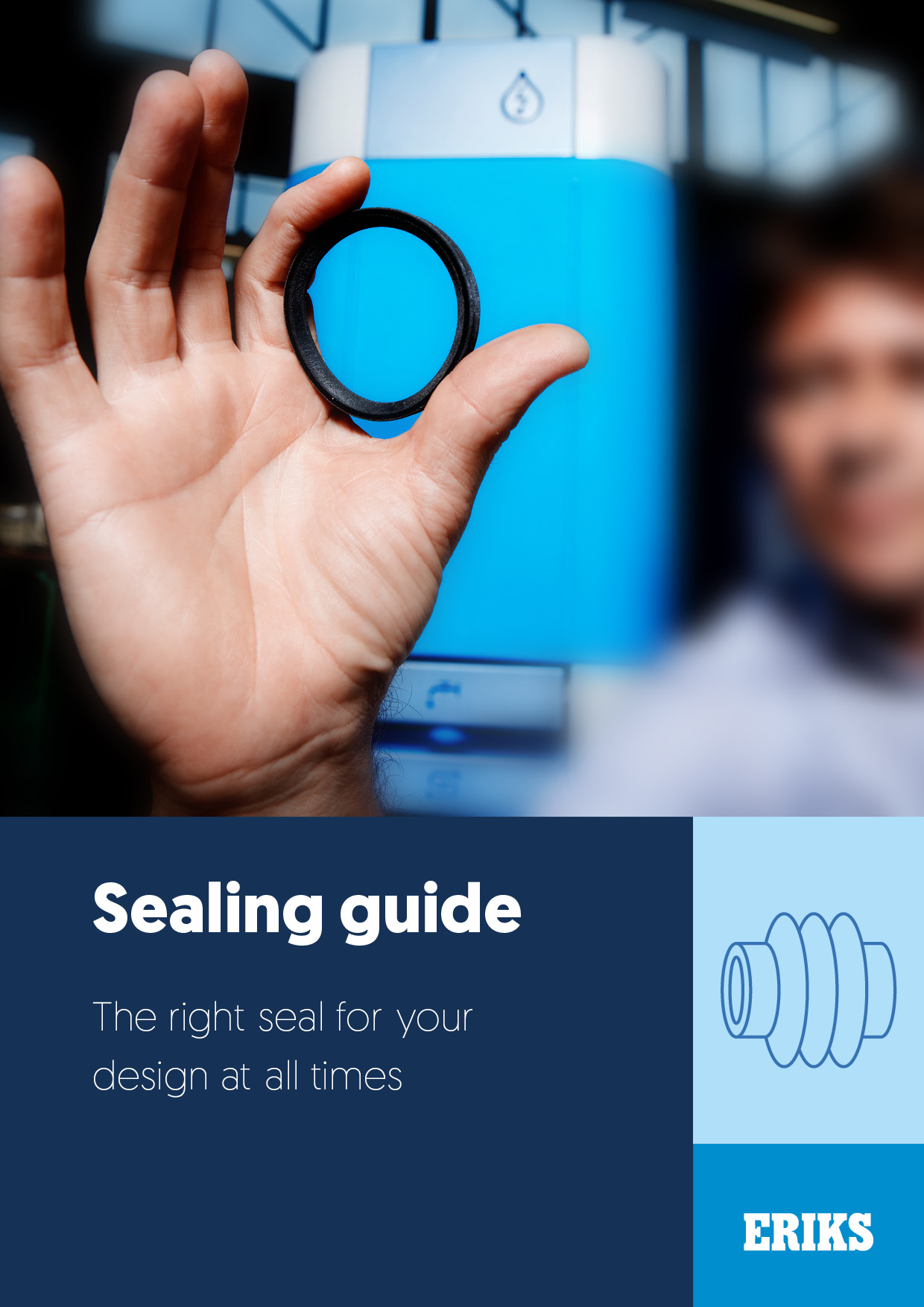
Related articles
Kontakt
Direktkontakt
Sie möchten mit einem unserer Mitarbeiter oder Experten persönlich sprechen? Zögern Sie nicht, kontaktieren Sie uns
Allgemeiner Kontakt
Nehmen Sie Kontakt mit uns auf. Bitte füllen Sie unser Online-Formular aus, wir werden Ihnen schnellstmöglich antworten.
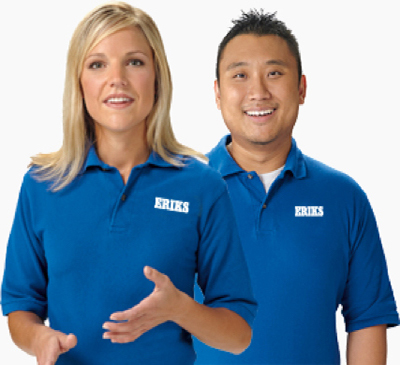