In this article
Streamlining Plant Turnarounds: A Roadmap for Success
Chemical plant turnarounds involve significant risks and require dealing with tight timelines, communication barriers, and stringent safety measures. As a Maintenance Manager, your duty is to execute vital tasks safely and efficiently during shutdowns while addressing the specific challenges of your chemical plant.
Turnarounds represent a considerable share of maintenance costs, and each day of halted production can result in significant financial losses, making it crucial to adhere to the schedule and manage expenses effectively. Integrating onsite services into your turnaround strategy can help tackle these challenges head-on and streamline the entire process, leading to substantial cost savings and a more successful plant turnaround.
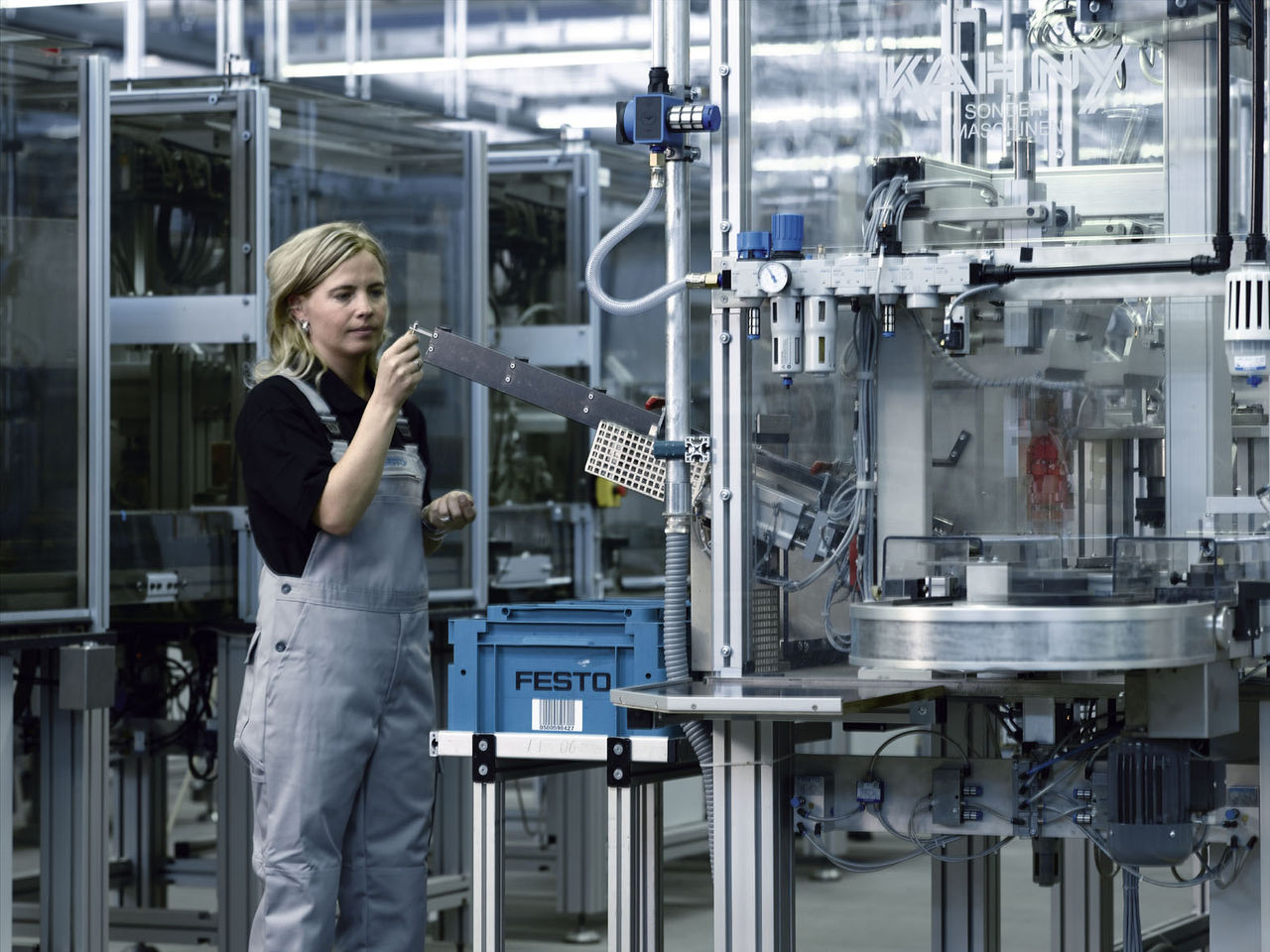
Comprehensive Preparation with Onsite Services
A successful turnaround hinges on meticulous planning and execution. Incorporating onsite services into your preparation process ensures you have accurate information on stock items (such as gaskets, flanges, valves, pumps, bearings and/or belts), staff, training, certification, warranties and activities to be performed. Inaccurate information could lead to increased downtime, while correct data enables more effective pre-planning.
Onsite service providers like ERIKS can also support you during the shutdown by documenting the ranges of devices and providing them at the end of the service for updating the nomenclatures. This accurate data enables more effective pre-planning and ensures the success of your turnaround.
Onsite service providers offer the expertise needed to create a detailed overview of the turnaround process, allowing you to limit the scope of work and minimize time and costs. By partnering with a service provider, you can also identify maintenance tasks that can be completed beforehand or postponed, ensuring only essential work is carried out during the turnaround.
By partnering with a service provider like ERIKS, you get access to a range of services, including training in good tightening practices to reduce leaks and awareness of galvanic corrosion, for instance, for increased safety and cost efficiency. Our dedicated internal teams work closely with you from the upstream preparation phase to ensure a successful turnaround.
When preparing for your turnaround with the help of onsite services, make sure to define the following:
- Detailed cost estimate
- Shutdown dates & expected timeframe
- Goals & objectives
- Scheduled work criteria
- Stock requirements
- Core teams & additional staff
- Dynamic risk assessment
Leveraging the expertise and support of an onsite service provider in your turnaround preparation can streamline the process and reduce costs while ensuring safe and efficient execution.
Thorough Planning and Walk-throughs
Proactive planning is crucial for a successful turnaround. Integrating onsite services into your planning process helps create a clear and efficient framework for all turnaround activities, ensuring information is aligned and resources are optimally utilized.
As a Maintenance Manager, assessing your team's knowledge, skills, and experience is essential for allocating responsibilities and tasks effectively. An onsite service provider can support you in this process by providing expert personnel, such as Field Engineers, to supplement your team's capabilities.
For a proactive approach, start planning your turnaround well in advance, ideally 6 months to a year, depending on the size and age of your plant. This allows time for adjustments, training, or addressing unforeseen issues.
Onsite services, such as ERIKS Application Engineers, can further streamline your operations by providing technical analysis and support throughout the turnaround preparation process. Working closely with your team, they can manage tasks such as flange calculations, finding more effective solutions, overseeing stock, and identifying better alternatives when necessary.
By incorporating onsite services into your planning and walk-through stages, you will benefit from their expertise and support, ensuring a more efficient, cost-effective, and successful turnaround.
Partner with a Trusted Onsite Service Provider
As ERIKS, we understand that minimizing downtime is imperative to your operations, particularly when significant financials are involved. We are more than just a reliable service provider - we are your strategic partner committed to ensuring the success of your turnaround.
Cultivating a trusting relationship with us allows you to take full advantage of our in-depth equipment knowledge and insights into your plant. By involving us from the start and throughout the planning phase, we guarantee our continuous support for a smooth and efficient turnaround process.
At ERIKS, we offer comprehensive solutions, not just parts delivery. We specialize in services that include the provision of pre-commissioned items for turnarounds, such as flange inspection, calculation, and flange management. Our team collaborates closely with you, working tirelessly to deliver the best solutions on time and with precision, according to your specific needs.
Optimize Stock Management
Effective stock management is more than just a necessity—it is the lifeblood of cost-efficient and seamless turnaround operations. Partnering with us means entrusting your stock management to a dedicated team of experts who prioritize your efficiency.
Our unique Plug & Play Solutions are designed with your convenience in mind. We supply 20 ft containers, filled to the brim with all the materials necessary for your turnaround. We collaborate closely with you to determine the precise gaskets, stud bolts, tools, valves, drive components, and maintenance products you will need, in the right sizes and quantities. This ensures immediate availability of essential materials right at your doorstep, facilitating smooth operation.
But our commitment doesn't stop there. We recognize that maintaining stock levels during the shutdown period can be a daunting task. That is why we stand ready to deliver any missing or customized products swiftly, allowing you to stick to your shutdown schedule while focusing on other pressing tasks.
In addition, we provide referencing facilities and categorization of items according to their criticality, specificity, and lead time needs. Imagine having a roadmap with five categories, each representing the criticality of an item—this could be your reality with ERIKS.
And to further streamline your turnaround operations, we can set up kits and benchmarks ensuring prompt item availability. Our goal is to ease the process and help you navigate your turnaround efficiently.
Outsourced Turnaround Management for a Smoother Process
Turnarounds often involve large numbers of contractors working on-site for the first time, along with staff performing non-routine tasks. This can create daunting safety challenges for Maintenance Managers to oversee. Outsourcing turnaround management to a reliable team can significantly ease this burden and streamline the process.
We support plant shutdowns at various chemical plants each year, making it our priority to get your operations up and running as quickly and safely as possible. Our experienced turnaround management team works closely with on-site personnel, providing valuable knowledge, expertise, and support.
In the event of unexpected issues, we offer real-time advice and employ systematic, disciplined approaches to ensure your turnaround runs smoothly. Available 24/7 to assist on-site, our wide range of products and application know-how in sealing technology, power transmission, flow technology, and tools makes us a reliable partner for outsourcing maintenance turnarounds.
By entrusting your turnaround management to a reliable outsourced team, you can alleviate safety concerns, enhance efficiency, and ensure a successful and cost-effective process.
Evaluate Your Turnaround for Continuous Improvement
Gaining valuable insights from past experiences is key to making better decisions for future turnarounds. Whether your plant has a dedicated TA Team or assembles one every 2-4 years, it is essential to systematically document and analyze previous turnarounds for easy access and review by future teams.
Having comprehensive data on past turnarounds enables you to identify successful processes, areas that need improvement, and valuable information for other department managers, directors, and stakeholders.
When evaluating your turnaround's effectiveness, consider the following questions:
- Was the turnaround completed on time and within budget, with priority work accomplished?
- Are debriefing documents and turnaround summary reports readily available?
- Were KPIs met or adjusted, and if so, how?
- Did communication channels work effectively, without friction?
- Were progress and delays documented and displayed throughout the process?
- Were feedback surveys completed and analyzed?
- Did the evaluation highlight opportunities for change?
Taking the time to review and learn from each turnaround helps streamline processes for future projects, ensuring a smoother handover and an improved learning curve for other TA Teams. This ongoing evaluation ultimately leads to more efficient and cost-effective turnarounds, driving continuous improvement and success for your plant.
Embrace Flexibility: Preparing for the Unplanned in Your Turnaround
While thorough planning is essential for a successful turnaround, it is equally important to be prepared for the unexpected. A Bill of Materials (BOM) is typically completed and delivered on time, but unplanned equipment failures can still occur, especially during start-up after powering down.
To minimize the impact of such unforeseen challenges, ensure your schedule allows for some flexibility and cultivate strong relationships with your suppliers. At ERIKS, we have a deep understanding of equipment and potential issues that can arise during a turnaround. By partnering with us, we can help you anticipate, plan for, and mitigate unexpected problems as effectively as possible.
The Final Word on Efficient Turnarounds
In conclusion, the successful execution of a chemical plant turnaround involves an intricate balance of thorough preparation, effective stock management and the ability to learn from past experiences. As your strategic partner, ERIKS provides comprehensive support, in-depth expertise, and innovative solutions that facilitate a seamless and efficient turnaround process.
Our unique offerings, including Plug & Play Solutions and stock management expertise, ensure immediate availability of essential materials and streamlined operations. Furthermore, our experienced turnaround management team provides round-the-clock assistance, ensuring safety and efficiency.
Your plant's turnaround success is our priority. Trust in our expertise, lean on our support, and let us navigate this journey together to ensure a smooth, efficient, and successful turnaround.
Subscribe to our newsletter:
For the latest industry news and updates.